會員登錄
MEMBER LOGIN
技術論壇
TECHNOLOGY FORUM
六十年來我國鑄鐵材料的發展
發布時間:
2016-03-14 00:00
來源:
(作者:張伯明)
摘要:我國是鑄造生產大國,2010年鑄件年產量已近4 000萬噸,連續11 年位居世界首位遙鑄造新材料,新技術不斷得到推廣和應用,鑄件質量逐漸提高,我國的鑄造業正在向鑄造強國挺進。本文簡要論述了鑄鐵材料的發展歷程、現狀以及未來發展趨勢。詳細介紹了我國在灰鑄鐵、球墨鑄鐵等溫淬火球墨鑄鐵(ADI)、蠕墨鑄鐵、可鍛鑄鐵以及特種性能鑄鐵方面的發展及應用情況,并指出了未來的發展方向。
關鍵詞:鑄鐵;發展;現狀;趨勢
中圖分類號:TG143
文獻標識碼:A
文章編號:1001-4977(2012)01-0001-10
60年前,新中國成立之初,我國基本沒有工業,鑄造也僅是為修配服務的手工作坊,鑄件的總產量僅幾十萬噸。隨著國家經濟的發展、工業體系的建立,鑄造業已發展到今天的能為現代化建設服務的以一大批機械化和部分自動化企業為骨干的鑄造工業。至今鑄造廠總數逾3萬個,從業人員近300萬,鑄件年產量近4 000萬噸,能用各種鑄造方法生產各種材質的鑄件,不僅基本滿足了國內的需求,還有近 10%的出口。今后將在適應經濟全球化的要求下,積極開發與采用先進技術與裝備,從產量、質量、經濟、節能、節材、環保以及工人勞動條件等方面考慮,走規模化、綠色生產之路,保障鑄造業的可持續健康發展,向鑄造強國挺進。
鑄造金屬材料占金屬材料總量的1/10~1/7。鑄鐵材料占據鑄造金屬材料的主導地位,歷年的統計表明,鑄鐵材料占 70%以上,也就是鑄鐵材料約占整個金屬工程材料的 5%左右,起著舉足輕重的作用[1]。
表1列出了能收集到的我國統計資料,從表1可以看出鑄鐵材料和整個鑄造業一樣取得了長足的進步,比60年前翻了幾十倍。
表1 我國鑄鐵件生產情況
最早真正從礦石煉鐵澆注鑄鐵件的是我們中國。公元前513年就澆注出了重270 kg 的鑄鐵刑鼎,比歐洲早了 1900 年。鑄鐵最初的應用是替代銅用在藝術品、炊具以及犁鏵等農具上,18 世紀西方工業革命后才真正把鑄鐵應用在工業領域做蒸汽機零件、鐵軌、橋梁、輸水管道上,形成了近 20 個世紀的鐵器時代。技術的進步和產品的精化要求工程材料有更好的性能,于是在鑄鐵的基礎上人類又研究出了鋼及有色合金等其他金屬材料、高分子材料、陶瓷材料與復合材料,從而也打破了鑄鐵材料一統天下的局面。零件的形狀不同,使用的工況不同,對制造零件的材料要求也就不同,因此各種工程材料之間的競爭是必然的。但是鑄鐵材料由于其鑄造性能好、重量幾乎沒有限制、導熱性好、減振性好、尤其是切削加工性能好的優點,至今仍在世界鑄造材料中保持絕對優勢(見表2),其占有量達到 72%以上。有人還根據球墨鑄鐵、等溫淬火球墨鑄鐵、蠕墨鑄鐵在當今的發展與應用,稱新的鐵器時代即將到來。
1 灰鑄鐵
灰鑄鐵至今仍是鑄造材料中產量最大的基礎材料。雖然片狀石墨的存在使其具有一定的脆性,但其具有最好的鑄造性能、熱導性能、減振性能與切削加工性能,所以技術進步體現在灰鑄鐵上是力求提高其基體組織中的珠光體含量,從而提高其抗拉強度。19世紀60年代灰鑄鐵的抗拉強度僅在60~80 MPa,后來在使用40%~80%廢鋼時達到了200 MPa,1922年美國發明孕育鑄鐵后才使灰鑄鐵件抗拉強度達到 350~380 MPa。
60 年前,我國鑄造業基本 都 是生產HT150和HT200的牌號。第一個五年計劃引進的產品,無論是汽車、拖拉機還是其他產品,多采用HT200及以下的牌號。改革開放初期,為適應國外內燃機缸體、缸蓋采用HT250的情況,國家在“六五”期間還組織中國農業機械化科學研究院與中國一拖集團有限公司、鄭州機械研究所與二汽、沈陽鑄造研究所與一汽進行了專題攻關。60年的努力,我們的成就可以歸納為以下幾個方面。
(1) 制定了和國際標準相當的國家灰鑄鐵件標準。一些骨干企業基本掌握了生產各種牌號灰鑄鐵的能力。例如一汽鑄造廠現能批量生產HT300的6DL德國道依茨發動機缸體[2],并儲備了HT350的生產技術。
(2) 充分認清了孕育的好處。掌握了各種孕育技術,并開發出適應于不同鑄件的孕育劑。首先是生產各類灰鑄鐵的鑄造企業都采用了沖入法包內孕育,其次是一些骨干企業在“六五”后都陸續采用了隨流孕育、型內孕育等后孕育方法,消除了鑄件棱角的白口,改善了斷面均勻性,從而提高了切削性能,過去很多企業使用的退火爐都已基本不用。在“六五”后,鑄造企業與鐵合金廠合作,開發了含鋇、鍶、鋯、碳等各類孕育劑,以適應生產不同的鑄件,打破了過去單一使用SiFe75的局面,做到了專業化、系列化、商品化。
(3)認識到提高鐵液溫度的重要性。鑄件的質量與其熔煉溫度有著密切的關系。提高鐵液熔煉溫度至臨界溫度以上,能提高鐵液的純凈度、減少氧化程度、減少鐵液含氣量、消除生鐵的遺傳性、細化石墨,確保足夠高的澆注溫度,從而能大量減少氣孔與夾雜等缺陷的生產[3]。
60年前,我國鑄鐵熔煉基本都使用三節爐熔煉,沒有電爐,后來引進推廣了原蘇聯的三排大風口沖天爐。國內的鑄造工作者又針對國內焦炭情況,花費了大量精力研究推廣了各種爐型的三排或多排小風口沖天爐。盡管原主管的機械部提倡抓大爐提高溫度,但由于使用冶金焦、土焦以及焦鐵比的限制[4],在20世紀50到80年代,全國沖天爐的熔煉溫度都處在1 380~1 430 ℃水平。20世紀80年代,在考察國外鑄造企業后,原機械部、農機部和冶金部一起,在我國研制成功了鑄造焦,并制定了相應的標準,加之當時開發的兩排大間距沖天爐,從而在任何爐型下都可使熔煉溫度達到1 450~1 480 ℃。同時在二汽鑄造廠的引領下,用感應電爐熔煉鑄鐵及沖天爐電爐雙聯熔煉技術在國內得到推廣。現在骨干企業的熔煉溫度都可保證在1 480~1 500 ℃,較之過去有了極大的提高。
(4)合成鑄鐵熔煉技術的應用。國外發達工業國家都使用合成鑄鐵熔煉技術,他們有大量便宜的廢鋼,故使用高溫電爐熔煉加增碳劑或外熱式熱風爐,回爐料以外的金屬料都用廢鋼,利用底焦高溫燃燒增碳的技術來獲得合適成分的鐵液。在同樣的化學成分下,它的抗拉強度要比用生鐵低溫熔煉的鑄鐵高1-2個牌號。國內從“六五”開始攻關,首先在二汽研究合成鑄鐵熔煉技術,如今在有廢鋼和電爐熔煉條件的鑄造企業也都開始應用此項技術,國內不少企業也為之開發了各種類型的增碳劑。
表2 2009年世界10大鑄件生產國的鑄件產量 /萬 t
(5)掌握了低合金化的熔煉技術。Cr、Cu、Sn、Mo、Ni等元素都有增加并細化基體組織中珠光體的作用,從而能有效地提高抗拉強度。尤其是廢鋼應用量的增大,可充分利用廢鋼中合金元素的作用。于是通過研究,掌握了利用高碳當量加合適的孕育工藝(合適的孕育劑與后孕育方法),配合低合金化生產的技術,得到了既滿足抗拉強度的要求又能得到縮松少、切削性能好的灰鑄鐵。
(6)初步了解了國外在熔煉灰鑄鐵時常用的一些冶金質量指標。同樣成分的灰鑄鐵,處理方法不同,其性能也就有差異。為了確定工藝及冶金措施的良好程度,國外的鑄造工作者提出了成熟度、硬化度、相對強度、相對硬度、品質系數等指標,其宗旨在于獲得高強度、低硬度的灰鑄鐵,從而既能發揮材質性能又便于隨后的機械切削加工。通過多年的努力,在一些骨干企業開始應用這些指標來生產高品質的灰鑄鐵。
60 年來 盡管灰 鑄鐵的產量與生產技術取得了很大的進步,但從整體生產技術水平來說,還比國外發達國家落后 30 年。這主要表現在三個方面。
首先,灰鑄鐵的熔煉溫度還比國外低50~70 ℃。國外用電爐、沖天爐(包括冷風沖天爐)始終要求熔煉溫度在1 500~1 550 ℃,雙聯保溫溫度在1 480~1 500 ℃。高溫熔煉的重要性和必要性,已有很多文獻可供參考[5]。
其次,我們鑄鐵工作者在實踐中還沒真正體會到,灰鑄鐵件的力學性能既取決于鐵液的化學成分與孕育方法,也取決于冷卻速度[6]。化學成分與處理方法相同的鐵液,在澆注不同鑄件時會產生不同的力學性能。因此正確的做法是要對每一種生產的鑄件,必須要通過試驗,確定相應的化學成分,從而才能保證所需的鑄件本體力學性能。這對于專業鑄造廠特別重要。對于從屬于主機廠的鑄造廠,則因常年生產固定品種,可以把同樣牌號的鑄件根據壁厚分成不同的類別,最終再確定合適的化學成分。鑄件的牌號不同、結構不同,如果要求每種鑄件的成分都不同,這無疑會給生產帶來很大的麻煩。所以應向國外學習,即采用基鐵熔煉制度:熔煉設備按工廠生產的鑄件類型設計一種成分的基鐵進行熔煉,然后在澆注前,在澆包內采用添加沖壓廢鋼精料、拋丸過的生鐵塊、銅片(絲)、鎳塊、各種中間合金,如鉻鐵、錳鐵、鉬鐵等材料以獲得適合鑄件的成分進行澆注。
第三,我們鑄件性能的穩定性太差,難以保證均勻一致性。在零件的生產中,往往切削加工的費用要高于鑄件本身的費用。為降低切削成本就必須要提高切削速度,而鑄件性能的均勻一致性對切削有決定性的影響。鑄件的硬度取決于性能要求,現代的切削技術對于高硬度鑄件的加工已不是問題,而鑄件硬度不均勻會嚴重影響加工性。鑄造企業為確保鑄件本體性能與隨后的切削性能,就要嚴格控制化學成分,一般要求灰鑄鐵碳當量的波動≤0.05%。
為說明這三點差距,表3、表4分別列出了德國一個專業鑄造廠和一個主機鑄造廠的實例。主機鑄造廠生產160種鑄件,抗拉強度要求≥220 MPa,他們把鑄件分為四組。兩廠都使用沖天爐電爐雙聯熔煉工藝,表5列出了兩廠使用的基鐵的成分。
表3 德國某專業鑄造廠對某些鑄件化學成分的控制規定
表4 德國某拖拉機鑄造廠對鑄件化學成分的要求
表5 基鐵成分
2 球墨鑄鐵
從20世紀30年代起,德、英、美的鑄造工作者,在用不同元素處理鐵液時就發現了石墨能從片狀轉變成球狀。1947 年英國人 H.Morrogh 發現,在過共晶的灰鑄鐵鐵液中,加入鈰和其他稀土元素,并以Si-Mn-Zr合金孕育,如果鐵液中的Ce的含量在0.02%以上,石墨則呈球狀[7]。1948 年美國A. P. Gangnebin研究在鐵液中加入鎂,隨后用硅鐵孕育,在鐵液中 Mg 含量≥0.04%時,可得到球狀石墨[8]。從此,球墨鑄鐵以其抗拉強度高、韌性好的優異性能進入了大規模的工業生產。
我國是在1950年研究成功球墨鑄鐵的。當時用壓力加鎂球化法用純鎂處理球墨鑄鐵,并在1958年以鐵代鋼的口號下形成全國性推廣的高潮。20世紀50年代末,在我國開發和應用稀土的號召下,開發出了稀土鎂球墨鑄鐵。1965年無錫柴油機廠研制出沖入法球化方法,從而在全國范圍內促進了球墨鑄鐵的應用。從無到有,球墨鑄鐵60年的進步可歸納為幾個方面。
(1)作為一種新型工程材料,球墨鑄鐵的發展是令人驚異的。1950年世界球墨鑄鐵才5萬噸,中國是零,而至2010年,世界球墨鑄鐵產量近2 000萬噸,而我國已達990萬噸,占世界總量的49.5%。
(2)球墨鑄鐵的應用領域不斷擴大。20世紀70年代,一汽、二汽用球墨鑄鐵開始替代可鍛鑄鐵,至今球墨鑄鐵件已占載重車鑄鐵零件的50%~60%。以新興鑄管集團為代表,建立了一批離心球墨鑄鐵管廠,2010年,我國球墨鑄鐵管產量達到了 352.4 萬噸。在短短的20年中,球墨鑄鐵做到了100%取代灰鑄鐵管被廣泛應用于供水行業,2010年在全國41萬公里的供水管中占26.1%,并作為供水行業公認的首選材料以及老系統的改造中(全國37%的總管線要改造),其使用比率將越來越大。在生產工藝上,國內也完成了100%采用離心工藝替代連續拔管工藝趕上了世界先進水平。現在DN80~DN1200的管子都采用水冷金屬型離心工藝,DN1400~DN2600 都采用熱模法離心工藝。
新興鑄管集團的產量在2010年已超過150 萬噸,已成為世界領頭羊。離心球墨鑄鐵管的出口也超過 70 萬噸,成為我國鑄件出口的主力。抗拉強度在600~900 MPa、伸長率在 3%~6%的球墨鑄鐵已被廣泛應用于內燃機的曲軸上,年產超過20萬噸,曲軸超過1 000萬支,也即我國內燃機的 50%都采用球墨鑄鐵曲軸。現在球鐵曲軸可用在4 000馬力的機車內燃機上,最大的曲軸重3.3 t,最大斷面厚度為椎280 mm。近年發展起來的風電鑄件多以球墨鑄鐵為主,每 MW 風電需球墨鑄鐵件15 t,故我國每年需風電球墨鑄鐵件20萬噸以上,大都采用QT400-18AL牌號的球墨鑄鐵,要求-20 ℃甚至-40 ℃的低溫沖擊韌度,并要求無損探傷檢查。
(3)開發出了各種球化處理方法。除傳統的壓力加鎂及隨后大量推廣的沖入法外,為獲得高的鎂合金吸收率及減少處理時的溫降和改善勞動條件、減少污染,國內先后開發出了蓋包法、轉包法、喂絲法、噴鎂法等先進處理工藝并得到了應用和推廣。
(4)系列化生產了球化劑與孕育劑。由于改革開放前的體制所限,鑄造廠使用的球化劑基本上是自己摸索、自己配制。國家在“六五”期間對“三劑”系列化商品化做了攻關,取得了豐碩的成果。現在的“三劑”都可由專業生產廠提供,并可根據特殊需要進行適當的調整。至今除轉包法與噴鎂法外,基本都使用稀土鎂球化劑,通常Mg含量為7%~9%,RE含量為6%~8%。
稀土元素的脫硫、脫氧能力比鎂強,但球化能力不如鎂,而且增加白口傾向,破壞石墨的圓整度,因此它的用量應僅限于消除干擾元素的作用。國外用轉包法生產球墨鑄鐵時,加入的 1#稀土量也僅為0.003%,所以早在20世紀80年代,中國稀土學會在召開的二次會議上明確指出,應降低稀土在球化劑中的含量。隨著現在生鐵質量的提高,尤其是高純生鐵的問世與推廣,完全可以進一步降低稀土元素含量,這樣既可節約資源也能降低球墨鑄鐵的生產成本。
60年來,我國在球墨鑄鐵方面取得的輝煌成績是有目共睹的。展望未來,球墨鑄鐵的產量以及占整個鑄件產量的比例還將大幅上升。在進一步發展過程中,筆者認為有幾點是值得注意的:首先是要努力提高球墨鑄鐵件質量的穩定性,這既和技術有關也和企業管理有關。技術上要保證獲得高的球化率,提高石墨球的圓整度,確保力學性能,尤其是伸長率的穩定和一致性。其次是要注意原鐵液的質量,包括提高鐵液熔煉溫度在1 500 ℃以上,保證球化處理溫度在1 480 ℃,高的鐵液純凈度,準確的成分,處理前盡量低的含硫量,使球化前的原始硫量在 0.03%以下。現在許多企業采用鐵液預處理,其目的也在于此。提高原鐵液的質量會提高成本,但可以從提高球墨鑄鐵件質量與降低球化劑消耗量來補償。第三是要使用高質量的原材料。鑄造也應像其他工業產品一樣,要生產好的產品,必須要使用高質量的原材料。中國鑄造協會制定了高純生鐵的標準,在 2011年7月1日起實施,這對提高球墨鑄鐵質量將起到十分重要的作用。表6是承德市保通鑄鐵型材制造有限公司利用當地的釩鈦礦石、采用弱氧化法在一個月中生產的31批高純生鐵的記錄。表7是常州華德機械有限公司采用這種生鐵生產的高鐵球墨鑄鐵件在三個多月中 60次生產的結果,從表中可以看出質量的穩定與一致性,誠然,從中也看出該廠的管理與控制水平。
3 等溫淬火球墨鑄鐵(ADI)
等溫淬火球墨鑄鐵也稱奧鐵體球墨鑄鐵,簡稱ADI。它是由球墨鑄鐵通過等溫淬火熱處理得到以奧鐵體(針狀鐵素體加富碳奧氏體)為基體的球墨鑄鐵。由于其具有高的強度(Rm可至1 600MPa),高的韌性(在Rm為800 MPa時仍有10%的伸長率),彎曲疲勞強度達420~500 MPa,接觸疲勞強度達1 600~2 100 MPa,高的比強度,與鋼相比又有密度小、減振降噪的優點[9],所以一經問世便受到了廣泛的關注,被認為是近代鑄鐵冶金的重大成就之一,現在又稱它為新鐵器時代的支撐之一。等溫淬火球墨鑄鐵的研究始于20世紀70年代,我國由鄭州機械研究所、6401廠和廈門汽車配件廠在1970 年就研究成功了此種新型球墨鑄鐵,并在1975年,汽車局就下令生產了5 000套ADI齒輪。但在1978年45屆國際鑄造年會首次宣讀ADI論文的是芬蘭KymiKymmene公司,我國曾藝成教授是在 1979年46屆國際鑄造年會上宣讀的論文,1984年美國召開了第一屆等溫淬火球墨鑄鐵的國際學術會議,盡管論文僅27篇,但參加人數逾200人,可見當時此種材料引起的轟動。為促進ADI在我國的研究與發展,在1986年,由鑄造學會鑄鐵及熔煉委員會召開了我國首次ADI學術會議。
表 6 保通超純生鐵
表 7 利用承德高純生鐵生產高鐵球墨鑄鐵件
作為一種新型工程材料,我國在 ADI 的研發和應用方面取得了顯著的成績。其產量基本上是以每年15%的速度在增長,至2007年世界產量已近30萬噸,其中美國20萬噸,歐盟2.5萬噸,我國6~8萬噸。ADI 的應用領域主要是汽車制造業,美國每輛重型卡車中使用500 kg以上的ADI零件[10]。回看ADI在我國發展的歷程,可以看到以下情況。
(1)我國是世界上最早發現等溫淬火球墨鑄鐵的三個國家之一。通過鑄造學會、稀土學會組織的五次專題學術研討會和一次產業化研討會,使廣大鑄造工作者了解掌握了ADI的基本知識、性能及其生產要點,為專業生產提供了技術基礎。至今已有不少企業從事ADI生產,還建立了兩個ADI專業生產廠,很多產品已經出口。由于ADI零件的應用必須通過設計部門的同意,所以國內CADI(HRC>56)的產量要比ADI的高,原因是此材質的部件是易損件,材質選擇由鑄造廠自己決定。為推廣 ADI 在我國的應用,我國已制訂了GB/T 24733-2009《等溫淬火球墨鑄鐵件》標準,于2010年9月1日起實施,為設計人員采用ADI件提供了充分的依據。這也表明我國ADI從試驗研究、開發應用,進入到了工業化生產階段。
(2)我國已具有工業化生產 ADI 的各種條件。ADI 生產的關鍵是等溫淬火熱處理工藝及其設備。我國最早研發,但生產后進的原因就在于當時沒有現代化的熱處理裝備。現在有浙江的嘉善三永電爐公司、南京新光英公司、上海寶華威、蘇州AP公司、遷西奧迪愛公司、AP長春公司都安裝有熱處理設備,他們可作為熱處理中心為每個具體零件制訂專有工藝(奧氏體化溫度和時間以及等溫淬火的溫度和時間)進行處理,為其他企業服務。
生產ADI的另一關鍵是首先要獲得優質的球墨鑄鐵毛坯件,石墨球必須圓整、球化級別必須在2級以上。如前如述,中國鑄協組織制定的高純生鐵標準,以及國內承德保通、武安龍鳳山以及濟南庚辰等企業都按此標準生產和提供生鐵,為生產好的球墨鑄鐵件打下了良好的基礎,而且他們自定的企業標準比行業標準更為嚴格。利用這種生鐵熔煉的鐵液純凈度較高、干擾元素少,十分有利于提高石墨圓整度與降低球化劑用量。此外,現在高質量球鐵件的生產企業大多采用了沖天爐感應電爐雙聯或感應爐熔煉,這就能保證提高鐵液純凈度、提高球化率及隨后的澆注溫度。
展望未來,ADI必將在我國得到迅速的發展。如果我們能趕上美國的水平,則可在短期內達到 50~70 萬噸的水平,要想實現這個目標,必須要重視以下幾個方面。
首先是要重視球墨鑄鐵毛坯件的質量。因球墨鑄鐵等溫淬火不能改變石墨形狀,只能通過改變基體組織來改變各種力學性能。如果石墨球化級別低、石墨球不圓整,則不可能達到標準所訂的各項性能。例如灰鑄鐵也可以等溫淬火,但其抗拉強度只能達到650 MPa,而且仍是脆性材料,伸長率接近零。所以好的球墨鑄鐵件通過等溫淬火才能獲得好的ADI鑄件。球化不好的球墨鑄鐵件,即使采用先進的等溫淬火設備也得不到合格的ADI鑄件。ADI的生產企業必須要采用純凈的原材料、良好的熔煉設備及球化工藝,在保證高質量的同時又有高的穩定性。
AOD、VOD 等爐外精煉方法提高了鋼液的純凈度,從而提高了鋼件的性能。那么對鐵液進行精煉將會有什么樣的效果,是一個值得探索和研究的問題。誠然,球化處理中,鎂、稀土等元素已有脫氧、脫硫的效果,但畢竟與專項精煉還是有差別。現在許多企業從事的預處理已使鐵液及最終的鑄件質量有所提高,但還是沒有深入探討對鐵液進行精煉處理的好處。至今,應該說等溫淬火球墨鑄鐵是鑄鐵中性能最好的鑄鐵材料,因此可以在生產ADI件中進行鐵液精煉處理的探索工作。
其次,一種工程材料的應用與發展,必須要有設計及產品技術管理人員的參與。鑄造行業生產ADI,利用其好的性能替代一些原有零件提高它們在使用中的安全系數是可以的,但還遠遠不夠。若采用優化設計,充分使用ADI的強度與韌性,代替鋼件,可以降低原鋼件重量的 20%,替代鋁件則可降低30%。因此必須要從設計人員開始,有意識地采用這樣新型工程材料來達到減重、節能和降低成本的效果。ADI 在美國得到廣泛推廣的原因在于他們的設計人員參與了工作。東風汽車廠在新設計的 5 t 越野汽車中,有14個45#鋼件,總重 630.62 kg,采用ADI并進行優化設計后減至380.66 kg,減重率為39.6%。現在一汽也正在進行類似的開發。
CADI在耐磨件上得到進一步推廣,ADI在汽車底盤、曲軸、齒輪等零件上得到廣泛應用,市場經濟規律也使 ADI 產量迅速增長。國家標準的出臺為設計人員選用ADI打下了基礎,ADI在國外產品上的應用也會給設計人員提供借鑒,而我國鑄造工作者在穩定做出好的ADI件的同時,還要對這種新型材料進行大力的宣傳。
4 蠕墨鑄鐵
碳主要以蠕蟲狀石墨存在于基體中的鑄鐵,稱為蠕墨鑄鐵。早在1947年,英國人H. Morrogh在用鈰研制球墨鑄鐵時就發現了蠕蟲狀石墨,但當時被認為是處理球墨鑄鐵的失敗產物,沒有引起重視。1955年美國人J. W. Estes 和 Schneidenwind首次提出建議采用蠕墨鑄鐵,但沒有做進一步的應用研究,直至1976年美國Foote公司配制出Mg-Ti系處理劑,才使蠕墨鑄鐵走上工業化生產的道路[11]。
我國對蠕墨鑄鐵的認識,也是隨著球墨鑄鐵的出現而開始的,20世紀60年代,我國在用稀土鎂鐵合金制作稀土鎂球墨鑄鐵時,在鑄件斷面上常見這種蠕蟲狀石墨,但作為一種工程材料的應用是從1965年開始的。當時廢鋼缺乏,為獲得高強度機床鑄鐵件,研究不加廢鋼,僅用稀土硅鐵合金直接處理沖天爐出來的高碳當量鐵液獲得高牌號灰鑄鐵的途徑,發現具有蠕蟲狀石墨的鑄鐵其強度大幅度提高,從而得到了推廣應用。由于這種鑄鐵是用稀土處理而得到的,因而曾命名為稀土高牌號灰鑄鐵、稀土灰鐵等。1979年后,根據光學顯微鏡下看到的石墨形貌,并與國外的命名力求統一,國內開始統一使用蠕蟲狀石墨鑄鐵,簡稱為蠕墨鑄鐵。40多年來,蠕墨鑄鐵在我國的發展可以概括為以下幾個方面。
(1)我國是首先在工程上應用蠕墨鑄鐵的國家之一。20世紀60年代開始用于高強度機床鑄鐵件上,1975年無錫柴油機廠用蠕墨鑄鐵生產300發動機缸蓋,并于1983年批量生產車用柴油機缸蓋;1985年二汽開始批量生產蠕墨鑄鐵排氣管,現已有若干專業廠為國內外汽車行業提供蠕墨鑄鐵排氣管;1984年我國首家專業蠕墨鑄鐵生產廠在恒臺誕生,其后改名為淄博蠕墨鑄鐵有限公司,現已成為世界上最大的蠕墨鑄鐵生產廠,主要生產焦爐門框,2010年產量超過6萬噸。至今除上述所提產品外蠕墨鑄鐵件還廣泛應用于玻璃模具、汽車剎車轂及鋼錠模等產品上,我國年產量已超過50萬噸。
(2)1983年我國制定了首個蠕墨鑄鐵行業標準,2011年我國蠕墨鑄鐵件標準已在6月公布,并將在 2012年3月起實施。此標準基本采用了ISO標準,也即達到國際先進水平。
(3)開發了系列的蠕化劑產品及相應的蠕化處理方法,基本滿足了不同零件的生產要求。
如何更好地推廣應用蠕墨鑄鐵這一工程材料也是值得我們去思考的問題。首先是如何在車用內燃機缸體上得到廣泛應用。近十年來這一領域在國外得到了迅速發展,Audi、Benz、BMW、Ford 等汽車廣泛采用蠕墨鑄鐵缸體,它既可以滿足內燃機向大馬力、大轉矩、低排放、低油耗發展,提高點火峰壓,要求材料有高溫性能的要求,又能使缸體的比功率重量低于鋁合金缸體。2010年僅在西方國家蠕墨鑄鐵缸體的產量已超過10萬噸。因此,鑄造工作者作好技術準備的同時,要讓設計人員了解材料的性能并在設計時采用。其次是如何精確控制鑄件本體的蠕化率。蠕化率和鑄件的壁厚有關,也即同樣處理的鐵液在澆注不同壁厚的鑄件時會得到不同的蠕化率[12]。另外工件的工況不同,其要求的蠕化率不同。因此如何去按設計要求做到規定的蠕化率是我們鑄造工作者值得去研究的問題。例如內燃機缸體都規定其主要壁及關鍵部位的蠕化率要在80%以上,所以要采用合適的生產工藝與檢測裝備。現在Sinter Cast 公司的爐前控制技術已得到廣泛應用,其他的競爭對手也有相應的開發,作為研究最早、發表論文也最多的中國也應在這方面有所作為。最后是要提高鑄件質量的穩定性,使同一產品具有始終如一的質量水平,這就要求我們在生產技術、工藝管理上采取強有力的手段。
5 可鍛鑄鐵
可鍛鑄鐵是由白口鑄鐵經石墨退火后使石墨成團絮狀的鑄鐵,具有一定的韌性,但并不可鍛。可鍛鑄鐵分白心和黑心兩類。我國在戰國時期就掌握了用熱處理方法生產鋼面白口鐵錛。歐洲在1720-1722年發明了脫碳退火工藝生產白心可鍛鑄鐵,美國在1820年發明了黑心可鍛鑄鐵的生產方法。
我國生產的都是黑心可鍛鑄鐵。50年前在引進的汽車上得到了廣泛的應用。在球墨鑄鐵大力發展后,球墨鑄鐵的性能可以覆蓋、高于黑心可鍛鑄鐵,因此在20世紀70年代后,它在汽車上的應用被球墨鑄鐵替代,產量大幅度下降,現在僅限于用在線路金具與小口徑的管件上。現在國內生產可鍛鑄鐵最10萬噸,其次在廊坊和山西太谷有可鍛鑄鐵鑄造廠,2010年總產量在60萬噸。
60 年來,對于可鍛鑄鐵的研究集中在合理調整原鐵液成分、開發各種處理劑來進行孕育以及進行預熱處理,最終是為減少可鍛退火時間。由于我國不生產可焊的白心白口鑄鐵,黑心可鍛鑄鐵由于退火處理時間長、生產周期長、耗能多,現正被其他鑄鐵材料所替代,產量還會下降。
6 特種性能鑄鐵
除一般的力學性能外,使用在不同工況下的零件還需要一些特殊的性能,例如耐磨、耐熱、耐腐蝕、無磁、低膨脹等性能。具有這些特種性能的鑄鐵稱為特種性能鑄鐵。它們一般都含有不同比例的鉻、鎳、鋁等合金元素,或硅元素超出常用的范圍,因此也常稱為合金鑄鐵。這些鑄鐵中的石墨可以是片狀、球狀,也可以完全沒有石墨而是白口鑄鐵。為此,它的產量也沒單獨統計過。
耐磨鑄鐵在特種性能鑄鐵中占有很大的比例[13]。世界1/3~1/2的材料與能源消耗是由零件磨損造成的,而磨粒磨損又占其50%[14]。例如,我國在礦山、水泥、發電中的耐磨件消耗一年在300萬噸以上,其中鑄造磨球就超過100萬噸。全國有近1 000家企業生產鑄造耐磨材料,其中最大的寧國耐磨材料總廠年產量超過10萬噸。耐磨鑄鐵中使用量較多的合金元素是鉻。
耐熱、耐蝕的奧氏體鑄鐵也占有相當的比例,其主要添加元素是鎳和硅,被廣泛用于內燃機增壓渦輪及化工、石油行業。目前,國內已有世界高水平的高鎳鑄鐵生產企業。60年來,特種性能鑄鐵也是從無到有,產量從小到大,現在我國已有各種性能的鑄件供應市場,而且都制定了相應的國家標準。這是一個新的領域,隨著選材的精化,只要嚴格按照規范生產,此部分產量將能快速增長。
7 結束語
60年,在鑄鐵材料的發展史中只占很小的區間,但是新中國的成立,尤其是改革開放以來,我國在鑄鐵材料方面取得的成績遠大于過去的2000多年。今天我們已有各種品種的鑄鐵材料,生產技術也正在向世界先進水平靠攏,只要我們繼續努力開發,采用現代技術,穩定工藝,嚴格管理,我們的鑄鐵材料必將會迎來一個新的發展機遇。
(轉自:鑄造雜志)
附件下載:

-
地址:濟南市解放路134號 電話:0531-86401781 / 86952422 傳真:0531-86465075
郵箱:foundry-shandong@163.com 郵編:250013
版權所有 © 山東省鑄造協會 魯ICP備2021002429號
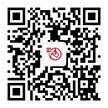
官方公眾號