會員登錄
MEMBER LOGIN
技術論壇
TECHNOLOGY FORUM
球磨機襯板失效分析與選材The ball mill lining board failure analysis and selection
發布時間:
2022-05-12 14:53
來源:
王定祥WANG Dingxiang
摘要:從球磨機工作原理、球磨機襯板磨損的影響因素出發,對球磨機襯板得失效與磨損機理進行了分析,分別對應用于水泥建材、冶金礦山及水利電力球磨機襯板的選材與工業應用進行了闡述,為球蘑機襯板正確選材提供了提供了依據。
Abstract:From the ball mill principle ball mill lining board wear the impact factors of lining board of ball to failure and the wear mechanism are analyzed,and the corresponding used for cement building materials metallurgy mine and water conservancy power ball mill of lining board of the material selection and industrial application were introduced,for the ball nebrodensis chenban right select material provided to provide the basis
關鍵詞:球磨機、 襯板、 失效分析、 磨損機理
Keyword:ball mill、lining board、failure analysis、abrasionmechanism
國民經濟的高速發展與科學技術的飛躍進步,耐磨材料新品種不斷地應用于實際的工業生產中。球磨機是廣泛應用于水泥建材、冶金礦山、水利電力、化工、煤炭等工業部門的粉磨設備,球磨機襯板是其主要消耗件,襯板的失效仍然是造成經濟損失的嚴重因素。本文對球磨機襯板進行失效分析,對球磨機襯板磨損的影響因素與失效分析機理進行探討,介紹的各種球磨機襯板材料,提供了正確選材的根據,以提高球磨機襯板的使用壽命、獲得較好的經濟效益。
1、球磨機工作原理:水泥建材、冶金礦山、水利電力、化工、煤炭的主要粉磨設備分為球磨機、簡稱磨機。它是一個兩端帶有支承裝置的圓筒體,內裝研磨體(又稱研磨介質)和被磨的物料(如石灰石、礦石或煤等),其總裝入量為筒體有效容積的25-45%。筒體繞水平的中心軸線回轉,筒體內的研磨體和物料在離心力和摩擦力作用下被筒體襯板提升到一定的高度,然后脫離筒體瀑瀉或拋落,物料循環地在筒體內運動受到研磨體不斷地沖擊、輥軋擠壓和研磨作用而被粉碎成為一定粒度要求的產品。物料從筒體一端的空心軸進入,而粉磨后的產品經筒體另一端空心軸排出。筒體內物料的移動是給予壓力來實現。筒體能夠回轉是由電機帶動減速機,減速機傳動筒體上的大齒輪實現的。干法磨時物料排出筒體被輸送出去。濕法磨時,物料被水流帶走。
球磨機的一般構造見圖1[1]。一倉階梯襯板在ф4.5×15.11m球磨機內安裝位置見圖2,ф4.5×15.11m球磨機襯板安裝外部情形見圖3,ф4.5×15.11m球磨機二倉分級襯板在筒體內情形見圖4。圖2磨機內三人中間為筆者。
圖1、球磨機的一般構造
1一進料裝置 2一支承裝置 3一回轉部分 4一出料裝置 5一傳動裝置 6一研磨體
作者簡介:王定祥(1936-),男,教授級高級工程師,主要從事金屬熱處理、耐磨材料的研究、應用與開發六十多年。聯系電話:13625325443,郵箱:wangdx256@163.com
圖2、一倉階梯襯板在ф4.5×15.11m球磨機內安裝位置
圖3、ф4.5×15.11m球磨機襯板安裝外部情形
圖4、ф4.5×15.11m球磨機二倉分級襯板在筒體內情形
球磨機中主要磨損件是襯板與磨球。襯板是球磨機筒體和進出口料端蓋的保護板,承受研磨體和物料的沖擊與研磨。襯板的磨損與工況條件,破碎物料以及襯板形狀結構與材料本身的性能及磨損特性有關。
2.球磨機襯板磨損特性的相關因素
(1)襯板的相對耐磨性與襯板金屬材料本身的硬度呈線性關系,淬火回火耐磨合金鋼隨硬度呈線性關系:
ε=ε0+b(H-H0)
ε---耐磨合金鋼的相對耐磨性
ε0---耐磨合金鋼退火后的相對耐磨性
b---耐磨合金鋼化學成分系數
H---淬火后硬度
H0---退火后硬度
由此可見,襯板的硬度愈高耐磨性愈好
(2)襯板的磨損率與球磨機直徑成正比[2]
η=D.1.5
式中 η-球磨機襯板磨損率
D-球磨機直徑
由此可見,球磨機直徑越大,襯板被磨損的愈多。
(3)襯板選材與襯板形狀結構有關
國外球磨機襯板塊小而厚,有利發揮耐磨材料性能,使用壽命長。國內球磨機型號較老,襯板塊大而薄,在使用新型耐磨材料時如不改變形狀結構就容易開裂。因此采用新型耐磨材料就有一個襯板形狀結構合理設計問題。溝槽襯板比階梯襯板提高使用壽命30%以上。
(4) 襯板選材與對物料的粉磨工藝有關
球磨機喂料量必需保持穩定。喂料量過大物料細度不夠,不合要求,喂料量過少,則造成磨球直接砸襯板的機會增多容易造成襯板開裂。因此襯板要選用高硬度、高韌性的材料。
(5)襯板金屬材料的硬度與物料硬度的相互關系
選擇襯板金屬材料硬度按下列公式
Hm=(0.8-1.25)Ha
式中 Hm-襯板金屬材料磨損后的硬度
Ha-被粉磨的物料硬度
由此可見,只有襯板金屬材料磨損后的硬度超過發被粉磨物料硬度的0.8倍,為高速磨損區,超過1.25倍時為低速磨損區;等于0.8-1.25倍為磨損區。襯板金屬材料磨損后的硬度必須超過被粉磨物料硬度的0.8倍才耐磨。
(6)襯板的磨損與磨球硬度的關系
在球磨機內磨球、襯板與物料組成一個磨料磨損系統,磨球與襯板是一對摩擦副,物料在一對摩擦副當中被粉碎。周文龍等人[3]對不同硬度磨球分別與鉻合金鋼襯板、高鉻鑄鐵襯板組成摩擦副對磨球磨損、襯板磨損以及摩擦副磨損情況在CHM-1型試驗機上進行試驗做了大量工作得出了磨球硬度比襯板高HRC2-5為最佳匹配而對襯板不造成過多磨損的結論。當磨球材料與硬度不變,襯板硬度的升高磨損下降。
不同硬度磨球與鉻合金鋼襯板配副時襯板磨損、磨球磨損及摩擦副磨損情況見圖5及圖6。不同硬度磨球與高鉻鑄鐵襯板鑄鐵襯板配副時襯板磨損、磨球磨損及摩擦副磨損情況見圖5 。圖5之1 與圖6之1可以看出鉻合金鋼襯板與高鉻鑄鐵襯板在與HRC30-65的磨球配副時磨損失重情況,隨著磨球硬度的升高襯板磨損增加。這說明磨球硬度升高使物料的磨損程度向襯板轉移,這說明磨球硬度過高削弱襯板抗磨損能力。圖5之2與圖6之2 可以看出HRC30-65的磨球與鉻合金襯板及高鉻鑄鐵襯板配副時隨著磨球硬度的升高磨損減少,這說明硬度較高的磨球抗磨性好,磨損降低。圖5 之3與圖6之3可以看出鉻合金鋼襯板及高鉻鑄鐵襯板與HRC30-65磨球配副時總磨損失重情況。結果表明隨著磨球硬度的增加摩擦副的磨損降低到一定值后隨著磨球硬度的升高再增加,摩擦副的磨損存在一個最低區。鉻合金鋼襯板,硬度為HRC43-45與磨球配副時摩擦副最低磨損的磨球硬度范圍為HRC53-58,磨球比襯板硬度高約HRC13。高鉻鑄鐵襯板,硬度為HRC5R3-55與磨球配副時摩擦副最低磨損的磨球硬度范圍為HRC55-60,磨球比襯板硬度高約HRC2-5。由此可以得到磨球與襯板組成摩擦副時磨球硬度比襯板硬度要高HRC2-5的結論。
(7)襯板的耐磨性還要襯板金屬材料有足夠的韌性
襯板材料的硬度不是經過熱處理后獲得影響耐磨性的唯一因素。襯板金屬材料要有足夠的韌性。硬度表示金屬低抗物料的入侵度,而韌性則表示金屬吸收能量而不致斷裂的性能。根據倉次的不同,工作部位不同而選材。粗磨倉襯板金屬材料的韌性要求比細磨倉要高。
(8)襯板的使用性能與襯板金屬的金相組織有關
襯板金屬化學成分的合理設計以及通過熱處理獲得優良的金相組織是提高襯板使用性能的重要因素。在干法磨機中低合金鋼、中合金鋼襯板具有馬氏體+碳化物的金相組織比僅有馬氏體組織的耐磨性好;相同鋼種晶粒細的比晶粒粗的耐磨;如果殘余奧氏體太多,例如大于11%,可能導致開裂。 在濕法磨機襯板具有低碳馬氏體組織抗腐蝕磨損性能要好,硬度也不低,其使用壽命比高錳鋼可提高30%至一倍以上。在鉻系合金同一牌號中碳化物種類形態、大小、分散度以及在基體組織所占比例對使用性能產生很大影響,其使用壽命可差別1-2倍。
(9)襯板不宜選用高錳鋼的原因
工業上使用高錳鋼做耐磨鋼具有一定的耐磨性要從高錳鋼的加工硬化機理解釋。在球磨機襯板實際工況條件下使用過的高錳鋼觀察不到加工硬化區域存在馬氏體,用加工硬化產生馬氏體轉變來解釋高錳鋼的耐磨性是不適宜的。高錳鋼在室溫形變過程中分三個階段。第一階段是滑移階段,此時滑移在一個滑移系內進行。第二階段,當高錳鋼由于非常高的應力作用,高錳鋼進一步形變,為減少位錯產生的內應力,位錯相互作用形成了胞狀結構即亞晶粒。當材料受到超過這個階段的應變,位錯被釘札住了,滑移不能再進行,斷裂就開始。高錳鋼在形變過程中位錯相互作用形成亞晶粒而產生了加工硬化,使硬度上升,因而提高了耐磨性。
高錳鋼不宜制作球磨機襯板的原因是在工況條件下造成的加工硬化作用不充分,使用壽命低。還在于,它在制作球磨機襯板時屈服強度低,容易產生塑性流變,襯板在使用過程中發生與筒體圓柱面的反向翹曲,其反向翹曲力大于螺釘的抗拉強度,就使螺釘被拉斷,于是襯板離開筒體而掉下。此種情況在尺寸較大的花紋襯板中常常遇到,例如在水泥廠時有發生。再者,這種塑性流變使襯板使用后和襯板螺釘粘結在一起,拆換襯板十分困難。高錳鋼制做水泥球磨機筒體襯板磨損后硬度為HRC34,初始硬度為HRC20;火電廠磨煤風扇磨高錳鋼沖擊板初始硬度為HRC20,殘體硬度為HRC28-38。均遠低于物料硬度,因而不耐磨。
3、球磨機襯板的失效形式基本可分為四種。一是斷裂失效;二是變形失效;三是磨損失效;四是腐蝕磨損失效。
(1)斷裂失效:襯板斷裂就成廢品。襯板在生產制造過程可形成裂紋,在使用中也可開裂。襯板斷裂給操作和維護帶來很大麻煩。磨機迴轉時襯板受到研磨體和物料的較大的沖擊力鑿削襯板,研磨體在下落時砸擊或滾壓,物料尖角切削襯板,當襯板強度不能承受鑿削沖擊所產生的高應力而斷裂。這是非正常失效,在生產制造及使用中應該防止的。
(2)變形失效:主要在高錳鋼做襯板的工況條件下容易出現。高錳鋼襯板在研磨體和物料的高應力鑿削沖擊下產生塑性流變,襯板厚度尺寸減小,周邊尺寸加大,襯板之間的間隙不夠充填,導致相鄰襯板頂撞而向離開筒體方向突起,引起緊固螺栓拉斷,造成襯板脫落。原因之一是高錳鋼的屈服極限低未達到“國標”要求;另一原因在水泥磨機中因熟料溫度高于200℃以上,未能控制在要求的140℃以下,不良工況造成高錳鋼強度及屈服極限的降低。這是非常正失效。變形失效在濕法磨機以及使用高鉻鑄鐵和合金鋼襯板時未見發生。
(3)磨損失效:磨損失效是襯板失效的最主要的形式,在一般情況下,都是由于正常磨損而失效的,它是不可避免的,它消耗的金屬材料最大.球磨機襯板在工況條件下,受研磨體和物料對本身的沖擊、滾動和滑動作用,受用溫度變化的影響,致使襯板表面材料磨損。對于濕法磨機來說,襯板還要受到腐蝕和水的侵蝕作用,濕法磨機襯板比干法磨機襯板磨蝕更快。磨機襯板的磨損過程是很復雜的,受系統中各種因素的影響,磨損機理與整個粉磨特性有關,系統中參量的變化導致磨損機理復雜。目前用幾種磨料磨損及腐蝕磨損來解釋。磨料磨損分以下三類:
①鑿削式磨料磨損:物料被粉磨成大顆粒磨料,有些磨料具有尖銳的棱角。磨料從襯板材料表面鑿削下金屬屑,材料的表面有嚴重的鑿槽或犁溝,形成鑿削式磨料磨損。鑿削式磨料磨損的微切削模型[4]見圖7。
由圖可見,磨料作用在襯板表面上的力P,分為法向力N和切向力T。法向力使磨料壓入表面,切向力使磨料向前推進。對表面切削,形成切槽(即鑿槽、犁溝)及切屑。在切槽底部及兩側是變形區。抵抗這類磨損,需要材料具有良好的韌性和高的硬度,以低御物料的切入。
②高應力疲勞磨粒磨損
磨機筒體做回轉運動,研磨體和物料在提升過程中與襯板產生相對流動和滑動,襯板表面受物料接觸處交變應力的輥碾作用,導致表面疲勞剝落。當研磨體和物料提升至最高點向襯板拋瀉沖擊時,襯板仍作圓周運動,迫使研磨體和物料改變原有運動方向,物料被粉碎成磨料,尺寸較大磨料繼續被碾碎,致使襯板微觀表面在高應力接觸作用的同時伴有沖擊拉伸,導致襯板表面產生微裂紋,繼續擴展使表面金屬剝落。對于韌性好的襯板材料在高應力接觸作用下塑性變形產生疲勞,在多次變形情況下,造成亞表層裂紋的形成與擴展,使表面金屬削落。對于脆性襯板材料由表面產生微裂紋導致碎裂與剝落。
物料或磨研體與襯板平面接觸時內部剪應力見圖8[5]。當物料或研磨體與襯板平面反復接觸,在最大剪應力處材料因疲勞而出現裂紋,裂紋擴展而剝落。磨損量隨α的增大而增加,而α值的大小,則隨載荷或物料、研磨體的半徑的增加而變大。如屬于純滾動時,最大剪應力發生在距表面為0.6a的深度內。
式中 α---物料或研磨體半徑
W-----載荷
R-----球的半徑
m1,m2---泊松比
E1,E2---縱向彈性模量
圖8 物料或研磨體對襯板表面接觸時內部剪應力
③低應力擦傷磨料磨損 襯板是在應力不超過磨料的壓碎強度時產生的,襯板金屬材料表面產生擦傷劃痕形成低應力擦傷磨料磨損。
(4)腐蝕磨損 球磨機襯板在腐蝕工況條件下表面因磨損與腐蝕共同作用出現的磨料耗損現象稱為腐蝕磨損。以腐蝕介質的性質不同分為化學腐蝕磨損和電化學腐蝕磨損。化學腐蝕磨損中最常見的是氧化磨損。氧化磨損是材料表面在腐蝕介質中形成氧化膜然后又不斷地被磨去而使材料損耗現象。電化學腐蝕磨損是金屬材料在腐蝕的電介質溶液中形成電化學反應的磨損行為。腐蝕機理以構成電偶來解釋。在腐蝕介質作用下襯板材料被機械磨損后露出新鮮表面,鐵(Fe)先去電子而荷正電,構成陽極區;水分子與氧結合獲得電子后生成OH-1,構成陰極區,構成電偶。這樣使襯板表面產生電位差,反應式為:
Fe Fe2+2e陽極
1/2O2+H2O+2e 2OH- 陰極
在腐蝕介質中襯板與被磨物料(礦石)表面氧化并吸附OH-構成陰極區。襯板不斷磨損露出新鮮表面,新鮮表面與物料接觸構成電偶,襯板中Fe不斷失去電子成為正離子向陰極游離構成材料的損耗,襯板就被腐蝕磨損。如果在腐蝕介質中加入防腐蝕劑,能使襯板表面形成鈍化膜,這種“鈍化膜”使襯板電位升高,降低了電流流動,從而減緩了腐蝕。襯板金屬面與不同種類腐蝕介質之間形成電化學腐蝕的不同電偶,不同電偶還與腐蝕介質的PH值有關。襯板、研磨體、物料(礦石)在腐蝕介質中也形成腐蝕不同的電偶,導致襯板研磨體腐蝕的加劇。電化學腐蝕的電偶還存在其他形式、如金屬多組織中相與相之間、成分偏析引起的同相晶粒之間、晶粒與晶界之間、應力分布不同的同相晶粒之間、晶界與晶界之間均存在電極電位差。磨損加速腐蝕:磨損使襯板表面產生塑性變形、增加位錯、產生裂紋等均使電極電位降低,使腐蝕加速。磨損使材料表面產生、犁溝、切削、變形和剝落,增加材料表面積和表面粗糙度,使腐蝕加速。腐蝕介質的攪動使襯板表面迅速補充新的腐蝕介質,使腐蝕加速。腐蝕加速磨損。襯板表面因腐蝕產生的疏松孔洞及腐蝕產物等于被磨損掉;腐蝕使金屬材料表面粗糙,晶粒被腐蝕降低材料的結合強度而加速磨損。襯板得腐蝕磨損往往既有化學磨損又有電化學腐蝕磨損。濕法磨改干法磨襯板磨損減少60%,濕法磨磨球比干法磨磨損大2-3倍。
磨機襯板的磨損往往不能用一種磨損機理解釋,磨損工況條件錯綜復雜,往往是以一種或二種磨損機理為主而輔以其他。
4、 水泥磨機襯板筒體襯板失效分析[6]
對水泥用球磨機筒體的高錳鋼襯板以及高鉻鑄鐵(鋼)襯板的磨損失效件對磨損形貌特征、磨屑、應力狀態變形特征等進行分析,斷定磨損的失效機制。將對ф2.2×6.5m水泥磨的一倉及二倉,在ф2.4×13m水泥磨的一倉,分別高錳鋼襯板及高鉻鑄鐵(鋼)襯板作了工業性對比試驗,并進行失效分析。
(1)幾種水泥球磨機筒體襯板的試驗材料特性和工作條件
試驗磨機規格、倉次及筒體襯板牌號、力學性能、金相組織及形狀尺寸等見表1;筒體襯板試驗的磨機工作參數見表2;磨機入磨物料配比及物理性能見表3;筒體襯板試驗磨機研磨體級配、直徑和質量見表4;
(2)磨損試驗結果 筒體襯板實際磨損試驗的結果。見表5
(3)水泥球磨機筒體襯板的宏觀失效特征及組織形態分析
表1 試驗磨機規格倉次及筒體襯板牌號、力學性能、金相組織及形狀尺寸等
編號 |
磨機規格(m) |
牌號 |
熱處理工藝 |
力學性能 |
金相組織 |
襯板形狀 |
襯板尺寸(mm) |
襯板質量kg |
|
HRC |
ak |
||||||||
1 |
ф2.4×13 |
ZGCr13SiMo |
970℃淬油,480℃回火 |
50-57 |
0.95 |
回火馬氏體+共晶碳化物+二次碳化物+少量殘余奧氏體 |
大波形 |
307×494×40 |
53 |
小波形 |
307×244×40 |
26 |
|||||||
2 |
ф2.2×6.5 |
ZGCr13SiMo |
970℃淬油,480℃回火 |
50-57 |
0.6-1.0 |
回火馬氏體+共晶碳化物+二次碳化物+少量殘余奧氏體 |
大階梯 |
308×244×20/70 |
45 |
小階梯 |
308×244×20/70 |
22 |
|||||||
3 |
ф2.2×6.5 |
ZGMn13 |
1050-1080℃水韌 |
HB207-219 |
|
奧氏體 |
大階梯 |
308×494×20/70 |
45 |
小階梯 |
308×244×20/70 |
22 |
注:ak值為10×10×55mm無缺口試樣沖擊值單位為J/CM2
表2 筒體襯板試驗的磨機工作參數
編號 |
磨機規格(m) |
工藝流程 |
試驗倉位 |
總倉數 |
有效容積(m3) |
研磨體充填率(%) |
轉速 |
功率(KW) |
臺時產量(t/h) |
粉磨細度(4900孔篩余量) |
運轉率 |
1 |
ф2.4×13 |
開流 |
第一倉 |
3 |
11.928 |
27.66-30.73 |
19.3 |
800 |
21 |
“325”礦400#水泥7-9% |
90% |
19.5 |
“425”礦500#水泥4-6% |
||||||||||
2 |
ф2.2×6.5 |
開流 |
第一倉 |
2 |
10.32 |
|
22 |
380 |
9 |
5-8% |
90% |
表2 筒體襯板試驗的磨機工作參數
表3 入磨物料配比及物理性能
編號 |
物料名稱 |
平均配比(%) |
硬度(HV) |
容量(kg/m3) |
|
1 |
熟料 |
325# |
35 |
450-600 |
1.67×103 |
425# |
50 |
||||
礦渣 |
325# |
60 |
|
|
|
425# |
45 |
||||
石膏 |
325# |
5 |
36-40 |
1.30×103 |
|
425# |
5 |
||||
2 |
熟料 |
45-50 |
450-600 |
1.67×103 |
|
礦渣 |
40-45 |
|
|
||
石膏 |
5-6 |
36-40 |
1.30×103 |
表3 入磨物料配比及物理性能
表4筒體襯板試驗磨機研磨體級配、直徑和質量
編號 |
材料 |
裝入鋼球直徑與質量(mm/t) |
平均球徑(mm) |
總量(t) |
||||
1 |
碳素鋼 |
ф70/1.4 |
ф80/4.11 |
ф90/5 |
ф100/5 |
|
ф88.8 |
15.5 |
2 |
高鉻鑄鐵 |
ф50/1 |
ф60/2.5 |
ф70/3 |
ф80/3 |
ф90/0.87 |
ф52/68 |
10.37 |
表5 筒體襯板磨損試驗結果
編號 |
材料 |
運轉時間(h) |
水泥產量(t) |
磨損率(g/t水泥) |
相對耐磨性(倍) |
備注 |
1 |
ZGCr13SiMo |
11712 |
354086 |
1.62 |
10.95 |
襯板生產廠唐山水泥機械廠使用廠上海水泥廠整倉裝機。 |
2 |
ZGCr13SiMo |
766 |
7277 |
|
|
①襯板生產廠唐山水泥機械廠,使用廠天津水泥廠②在運轉時取樣做磨損試驗。 |
①高錳鋼襯板磨損表面微觀形貌分析 高錳鋼是塑性材料,磨損微觀形貌是塑性變形特征。從對圖9及圖10ф2.2×6.5m水泥磨第一倉及第二倉襯板掃描由相片看,都具有犁溝,剝落坑及顯微裂紋。犁溝都有方向性。而第一倉的犁溝比第二倉寬而,鑿削使顯微切削掉金屬成犁溝邊緣因擠壓而隆起也可看到殘存的犁屑,此是塑料材料的象征。因沖擊疲勞使金屬剝落形成密集的剝落坑;顯微裂紋要少些。第一倉平均球徑與物料對襯板的作用力要大,襯板所承受的應力要大,襯板微觀形貌表現為犁溝為主,形成犁溝所卷起的犁屑在研磨體與物料的不斷作用下而剝落,形成密集的剝落坑,其溝底被沖擊形成疲勞裂紋,裂紋的擴展與延伸也使襯板表面金屬剝落,因此,高錳鋼在第一倉磨損失效機制是以鑿削式磨料磨損機制為主,高應力疲勞磨料磨損為輔。而第二倉襯板承受鑿削式作用力比第一倉要小些,犁溝淺而短,溝邊隆起高度小。顯微裂紋多,坑薄坑小。襯板在研磨體與物料產生的高應力疲勞作用下產生疲勞裂紋多。裂紋的擴展與延伸形成顯微切削使襯板表面金屬剝離。因此第二倉襯板磨損失效機制是以高應力疲勞磨料磨損為主,鑿削式磨料磨損為輔。
②高鉻鑄鋼襯板磨損表面微觀形貌分析 高鉻鑄鋼ZGCr13襯板在ф2.2×6.5m水泥磨一倉電鏡照片見圖11。高鉻鑄鋼是脆性材料,沒有塑性變形。高鉻鑄鋼金相組織是馬氏體+共晶碳化物+二次碳化物+殘余奧氏體,硬度HRC50-57。高鉻鑄鋼中的碳化物是(FeCr)7C3,顯微硬度為HM1300-1800,它比(FeCr)3C硬度為HM800-1100高。基體上碳化物的硬度比馬氏體高。從電鏡照片可以看到犁溝、凹坑及顯微裂紋。犁溝旁邊沒有象高錳鋼磨損表面那樣的隆起邊緣,也沒有殘留的犁屑,這是脆性材料形貌特征。犁溝有呈“T”字形貌,也有呈“人”字形貌。凹坑是共晶碳化物與二次碳化物剝落形成的,共晶碳化物顆粒剝落形成大坑,二次碳化物形成小坑。高應力疲勞裂紋表現為坑底裂紋及坑埂裂紋。磨損失效過程表現為襯板在研磨體與物料的作用下,表面首先形成犁溝,這是鑿削掉比碳化物硬度低的馬氏體基體金屬而形成的。鑿削向前進行對小于犁溝深度二次碳化物,削離遇到比犁溝深度高的碳化物則被擋住或拐彎。高應力疲勞作用使凸出的碳化物有的被粉碎,有的向坑底與坑埂施壓形成坑底裂紋與坑埂裂紋,碳化物與馬氏體的結合力減弱,裂紋的擴展與延伸,使碳化物被剝去一層。這樣,馬氏體基體又凸出來。研磨體與物料的繼續鑿削,馬氏體又形成犁溝。過程如此循環,襯板表面金屬一層一層被磨損消耗。因此高鉻鑄鋼襯板的磨損失效為鑿削式磨粒磨損及高應力疲勞磨粒磨損兩個機制同時進行。
5鐵礦濕式溢流型球磨機襯板磨損失效分析鐵礦是濕法球磨機,襯板磨損機制有鑿削式磨料磨損與高應力疲勞磨粒磨損等機制以外,還有腐蝕磨損。對東鞍山燒法廠ф2.7×3.6m濕式溢流球磨機高錳鋼襯板與筒體襯板具有濕法特征的磨損形貌分析如下。
(1)、東鞍山燒結廠磨機規格、物料組成及硬度見表6。
表6 東鞍山燒結廠磨機規格、物料組成及硬度
磨機規格m |
赤鐵礦 |
石英鐵礦 |
褐鐵礦 |
石英 |
||||
W% |
顯微硬度(HM) |
W% |
顯微硬度(HM) |
W% |
顯微硬度(HM) |
W% |
|
|
ф2.7×3.6m濕式溢流球磨機 |
45 |
766-1097 |
13 |
567-549 |
2 |
397 |
40 |
1197-1314 |
表6 東鞍山燒結廠磨機規格、物料組成及硬度
(2)、端襯板磨損失效分析
①物料經入料端進入球磨機經粉碎到出料,入料端物料粒度大,出料端物料粒度小,端襯板因物料粒度不同磨損情況不同。入料端襯板磨損要大,出料端襯板磨損要小。
②入料端襯板不同部位的磨損形貌不同[6]
球磨機運轉時物料入料端高錳鋼襯板的不同部位磨損情況不同,拆下殘體磨損表面測定硬度顯示為四個區,如圖12。(A)(B)大端部位由于研磨體與物料降落產生相對滑動在表面犁削,受沖擊較小,磨損表面硬度大致在肖氏硬度Hs53.5,主要屬于犁削式磨料磨損。(C)(D)小端受到研磨體與物料側沖擊力大,(C)(D)部位的加工硬化能力大,(C)磨損表面達Hs60,(D)部位受力較(C)部位小些,磨損還是要比(A)(B)部位嚴重磨損表面硬度為Hs54。由此(C)(D)部位的磨損主要屬于高應力疲勞磨粒磨損。
圖12 端襯板殘體硬度測定部位及磨損形貌
(3)筒體高錳鋼襯板磨損失效分析[6]
鑿削式磨料磨損與高應力疲勞磨料磨損 由于進料端與出料端物料粒度不同,將造成同機各部位筒體襯板的磨損情況不同,顯然靠近入料口部分的襯板比靠近出料口部分襯板磨損量要大。見圖13。
a)進料部位筒體襯板 b)出料部位筒體襯板
圖13 進料與出料部位筒體襯板磨損特征
從磨損形貌分析是鑿削式磨料磨損與高應力疲勞磨料磨損相結合的磨損機制。
(4)腐蝕磨損筒體高錳鋼襯板腐蝕磨損特征見圖14。
圖14 腐蝕磨損特征19000×
筒體高錳鋼襯板的腐蝕磨損因物料在鐵礦濕法磨中礦漿濃度、礦漿腐蝕性因素、固體含量、固體顆粒粒度及形狀、礦漿溫度、特別是影響礦漿腐蝕性因素的物料物質組成、性質、形成礦漿的化學成分(PH值、藥劑、氣體)與性質以及粉碎介質的化學成分、力學性能及金相組織等有關。按化學腐蝕機制及電化學腐蝕機制加速了磨損加劇,出現腐蝕磨損。圖25可見,犁屑被腐蝕掉已不存在,犁溝剝落坑邊經腐蝕趨平坦,腐蝕面有點蝕。在磨損面的凸出物在形成的“電偶”中為陽極而被腐蝕加速了磨損。
球磨機襯板常用耐磨鋼鐵材料牌號、化學成分、生產工藝參數示例、力學性能及應用示例。見表7
表7 球磨機襯板常用耐磨鋼鐵的牌號、化學成分、生產工藝參數示例、力學性能及應用示例
序號 | 生產工藝參數示例 | 金相組織 | 力學性能 | 應用示例 | |||
出鋼溫度 | 澆注溫度 | 熱處理 | HRC | akn(J/cm2) | |||
℃ | ℃ | ||||||
1 | 1610 | 1540 | 900℃水淬 | 板條M+少量針狀M | 48 | αku(J/cm2) | 火電廠球磨機襯板 |
200℃回火 | -52 | ≥20 | |||||
2 | 1610 | 1540 | 1020℃水淬 | 板條M+Ar | 48 | αku(J/cm2) | 火電廠球磨機襯板 |
180℃回火 | -52 | ≥62 | |||||
3 | 1610 | 1540 | 1000℃淬水, | M | 48-52 | 60-80 | 水泥球磨機襯板、隔倉板、篦板 |
200℃回火 | |||||||
4 | 1620 | 1550 | 950℃淬油,240℃回火 | M | 44-48 | 60-100 | 水泥球磨機隔倉板、篦板 |
5 | 1570-1580 | 1460-1480 | 900℃淬油, | 板條M | >50 | aku/(J/cm2) | 冶金礦山球磨機襯板 |
250℃回火 | 43-57 | ||||||
6 | 1520 | 1420 | 880℃淬火 | M+Ar | 50 | 70-80J | 火電廠球磨機襯板 |
-1530 | -1440 | 260℃回火 | -52 | ||||
7 | 1520 | 1420 | 930℃淬油 | M+Ar | ≥45 | KN2 | 火電廠球磨機襯板 |
-1530 | -1440 | 250℃回火 | ≥20 | ||||
8 | 1520 | 1420 | 930℃淬油, | M+Ar | 51-57 | 60-90 | 大型水泥球磨機襯板、隔倉板、磨頭襯板、篦板 |
-1530 | -1440 | 250℃回火 | |||||
9 | 1600 | 1420 | 900℃淬鹽水,240℃回火 | M(無Ar) | ≥50 | ≥50 | 中、小型水泥球磨機襯板、隔倉板、篦板 |
-1440 | |||||||
10 | 1530 | 1420 | 930℃淬油 | M+Ar | ≥50 | KN2≥25 | 冶金礦山球磨機襯板 |
250℃回火 | |||||||
11 | 1600 | 1480 | 950℃淬火,280℃回火 | M+Ar | ≥46 | ≥40 | 大型水泥磨隔倉板 |
-1500 | |||||||
12 | 1610 | 1540 | 980℃淬油 | 板條M+Ar | ≥42 | KV2≥12J | 冶金礦山球磨機襯板 |
250℃回火 | |||||||
13 | 1540 | 1480 | 950℃淬火, | M+Ar | 48-52 | 50-70 | 水泥球磨機隔倉板 |
-1580 | -1500 | 280℃回火 | |||||
14 | 1530 | 1420 | 980℃噴霧或淬油,300℃回火 | M+Ar | ≥48 | KN2≥20 | 冶金礦山球磨機襯板 |
15 | 1540-1580 | 1440 | 950℃噴霧 | M+C+Ar | 30-50 | 30-50 | 冶金礦山球磨機襯板 |
300℃回火 | |||||||
16 | 1540 | 1440 | 950℃噴霧, | M+C+Ar | 48-53 | 30-50 | 水泥球磨機襯板 |
-1580 | 300℃回火 | ||||||
17 | 1530 | 1440 | 930℃淬油 | M+Ar | ≥50 | KN2 | 火電廠球磨機襯板 |
260℃回火 | ≥12 | ||||||
18 | 1480-1500 | 1440 | 980℃噴霧 | M+C+Ar | 50-55 | ≥20 | 冶金礦山球磨機襯板 |
300℃回火 | |||||||
19 | 1430 | 1440 | 980℃噴霧,380℃回火 | M+C+Ar | 50-55 | ≥20 | 水泥球磨機襯板 |
-1500 | |||||||
20 | 1500-1520 | 1540-1580 | 920℃淬水或淬油 | M+B | 53-57 | aku/(J/cm2) | 冶金礦山球磨機襯板 |
250℃回火 | ≥2.3 | ||||||
21 | 1510 | 1410 | 930℃噴霧 | M+C+Ar | ≥50 | KN2 | 火電廠球磨機襯板 |
300℃回火 | ≥10 | ||||||
22 | 1500 | 1470 | 980℃淬油 | M+C+Ar | 54-60 | Ak/J | 冶金礦山球磨機襯板 |
380℃回火 | ≥6 | ||||||
23 | 1600 | 1540-1580 | 1020℃淬油 | 板條M | 46-52 | akn /(J/cm2) | 冶金礦山球磨機襯板 |
250℃回火 | 55-86 | ||||||
24 | 1440 | 1350 | 950℃空冷, | M+C | 48-53 | 2.0-3.0 | 生料磨及水泥磨細磨倉襯板 |
-1500 | -1400 | 260℃回火 | |||||
25 | 1460 | 1360 | 980℃淬火 | M+共晶C+二次C+Ar | ≥56 | 火電廠球磨機襯板、磨球 | |
-1480 | -1380 | 300℃回火 | |||||
26 | 1460 | 1440 | 980℃淬油,260℃回火 | M+C+二次C+B+Ar | ≥56 | 4.0-6.0 | 水泥球磨機襯板 |
-1500 | -1500 | ||||||
27 | 1460 | 1360 | 980℃淬油,480℃回火 | M+共晶C+二次C+Ar | 58-60 | 4.0-6.0 | 水泥球磨機襯板、立磨機輥立磨磨盤襯板 |
-1560 | -1400 | ||||||
28 | 1460 | 1370 | 980℃淬火,480℃回火 | M+共晶C+二次C+Ar | 58-60 | 4.0-6.0 | 水泥球磨機襯板 |
-1560 | |||||||
29 | 1460 | 1370 | 980℃淬火 | M+共晶C+二次C+Ar | ≥58 | 火電廠球磨機襯板,雙進雙出球磨機襯板、球環磨得上下磨環與磨球、平盤磨的沖擊板、爐勾、護甲和葉輪 | |
-1480 | 480℃回火 | ||||||
30 | 1460 | 1370 | 980℃淬火,480℃回火 | M+共晶C+二次C+Ar | 58-60 | 4.0-6.0 | 水泥球磨機襯板; 火電廠球磨機襯板,雙進雙出球磨機襯板、球環磨得上下磨環與磨球、平盤磨的沖擊板、爐勾、護甲和葉輪 |
-1560 | |||||||
31 | 1500 | 1360 | 1050℃空冷或吹風,500℃回火 | M+共晶C+二次C+Ar | 58-60 | 5.0-9.0 | 水泥廠立磨磨盤襯板、立磨磨輥、立磨磨盤襯板;火電廠球磨機襯板,雙進雙出球磨機襯板、球環磨得上下磨環與磨球、平盤磨的沖擊板、爐勾、護甲和葉輪 |
-1380 | |||||||
32 | 1500 | 1360 | 1020℃淬火,450℃回火 | M+共晶C+二次C+Ar | 58-60 | 6.0-9.0 | 水泥球磨機隔倉板、立磨磨輥、立磨磨盤襯板;火電廠球磨機襯板,雙進雙出球磨機襯板、球環磨得上下磨環與磨球、平盤磨的沖擊板、爐勾、護甲和葉輪 |
-1380 | |||||||
33 | 1520 | 1420 | 1080℃淬水 | A | KV2/J | 冶金礦山球磨機襯板 | |
≥118 | |||||||
34 | 1520 | 1420 | 1100℃淬水 | A | HBW210-270 | ≥60 | 冶金礦山及水泥球磨機襯板 |
35 | 1520-1540 | 1420-1440 | 1100℃淬火 | A | 冶金礦山球磨機襯板 | ||
36 | 1520-1540 | 1420-1440 | 1100℃淬水 | A | 冶金礦山球磨機襯板 | ||
37 | 1520 | 1420 | 1100℃淬水 | A | 冶金礦山球磨機襯板 | ||
38 | 1520-1540 | 1420-1440 | 1100℃淬水 | A | 冶金礦山球磨機襯板 | ||
39 | 1520-1540 | 1420-1440 | 1100℃淬水 | A | 冶金礦山球磨機襯板 |
序號 | 生產工藝參數示例 | 金相組織 | 力學性能 | 應用示例 | |||
出鋼溫度 | 澆注溫度 | 熱處理 | HRC | akn(J/cm2) | |||
℃ | ℃ | ||||||
1 | 1610 | 1540 | 900℃水淬 | 板條M+少量針狀M | 48 | αku(J/cm2) | 火電廠球磨機襯板 |
200℃回火 | -52 | ≥20 | |||||
2 | 1610 | 1540 | 1020℃水淬 | 板條M+Ar | 48 | αku(J/cm2) | 火電廠球磨機襯板 |
180℃回火 | -52 | ≥62 | |||||
3 | 1610 | 1540 | 1000℃淬水, | M | 48-52 | 60-80 | 水泥球磨機襯板、隔倉板、篦板 |
200℃回火 | |||||||
4 | 1620 | 1550 | 950℃淬油,240℃回火 | M | 44-48 | 60-100 | 水泥球磨機隔倉板、篦板 |
5 | 1570-1580 | 1460-1480 | 900℃淬油, | 板條M | >50 | aku/(J/cm2) | 冶金礦山球磨機襯板 |
250℃回火 | 43-57 | ||||||
6 | 1520 | 1420 | 880℃淬火 | M+Ar | 50 | 70-80J | 火電廠球磨機襯板 |
-1530 | -1440 | 260℃回火 | -52 | ||||
7 | 1520 | 1420 | 930℃淬油 | M+Ar | ≥45 | KN2 | 火電廠球磨機襯板 |
-1530 | -1440 | 250℃回火 | ≥20 | ||||
8 | 1520 | 1420 | 930℃淬油, | M+Ar | 51-57 | 60-90 | 大型水泥球磨機襯板、隔倉板、磨頭襯板、篦板 |
-1530 | -1440 | 250℃回火 | |||||
9 | 1600 | 1420 | 900℃淬鹽水,240℃回火 | M(無Ar) | ≥50 | ≥50 | 中、小型水泥球磨機襯板、隔倉板、篦板 |
-1440 | |||||||
10 | 1530 | 1420 | 930℃淬油 | M+Ar | ≥50 | KN2≥25 | 冶金礦山球磨機襯板 |
250℃回火 | |||||||
11 | 1600 | 1480 | 950℃淬火,280℃回火 | M+Ar | ≥46 | ≥40 | 大型水泥磨隔倉板 |
-1500 | |||||||
12 | 1610 | 1540 | 980℃淬油 | 板條M+Ar | ≥42 | KV2≥12J | 冶金礦山球磨機襯板 |
250℃回火 | |||||||
13 | 1540 | 1480 | 950℃淬火, | M+Ar | 48-52 | 50-70 | 水泥球磨機隔倉板 |
-1580 | -1500 | 280℃回火 | |||||
14 | 1530 | 1420 | 980℃噴霧或淬油,300℃回火 | M+Ar | ≥48 | KN2≥20 | 冶金礦山球磨機襯板 |
15 | 1540-1580 | 1440 | 950℃噴霧 | M+C+Ar | 30-50 | 30-50 | 冶金礦山球磨機襯板 |
300℃回火 | |||||||
16 | 1540 | 1440 | 950℃噴霧, | M+C+Ar | 48-53 | 30-50 | 水泥球磨機襯板 |
-1580 | 300℃回火 | ||||||
17 | 1530 | 1440 | 930℃淬油 | M+Ar | ≥50 | KN2 | 火電廠球磨機襯板 |
260℃回火 | ≥12 | ||||||
18 | 1480-1500 | 1440 | 980℃噴霧 | M+C+Ar | 50-55 | ≥20 | 冶金礦山球磨機襯板 |
300℃回火 | |||||||
19 | 1430 | 1440 | 980℃噴霧,380℃回火 | M+C+Ar | 50-55 | ≥20 | 水泥球磨機襯板 |
-1500 | |||||||
20 | 1500-1520 | 1540-1580 | 920℃淬水或淬油 | M+B | 53-57 | aku/(J/cm2) | 冶金礦山球磨機襯板 |
250℃回火 | ≥2.3 | ||||||
21 | 1510 | 1410 | 930℃噴霧 | M+C+Ar | ≥50 | KN2 | 火電廠球磨機襯板 |
300℃回火 | ≥10 | ||||||
22 | 1500 | 1470 | 980℃淬油 | M+C+Ar | 54-60 | Ak/J | 冶金礦山球磨機襯板 |
380℃回火 | ≥6 | ||||||
23 | 1600 | 1540-1580 | 1020℃淬油 | 板條M | 46-52 | akn /(J/cm2) | 冶金礦山球磨機襯板 |
250℃回火 | 55-86 | ||||||
24 | 1440 | 1350 | 950℃空冷, | M+C | 48-53 | 2.0-3.0 | 生料磨及水泥磨細磨倉襯板 |
-1500 | -1400 | 260℃回火 | |||||
25 | 1460 | 1360 | 980℃淬火 | M+共晶C+二次C+Ar | ≥56 | 火電廠球磨機襯板、磨球 | |
-1480 | -1380 | 300℃回火 | |||||
26 | 1460 | 1440 | 980℃淬油,260℃回火 | M+C+二次C+B+Ar | ≥56 | 4.0-6.0 | 水泥球磨機襯板 |
-1500 | -1500 | ||||||
27 | 1460 | 1360 | 980℃淬油,480℃回火 | M+共晶C+二次C+Ar | 58-60 | 4.0-6.0 | 水泥球磨機襯板、立磨機輥立磨磨盤襯板 |
-1560 | -1400 | ||||||
28 | 1460 | 1370 | 980℃淬火,480℃回火 | M+共晶C+二次C+Ar | 58-60 | 4.0-6.0 | 水泥球磨機襯板 |
-1560 | |||||||
29 | 1460 | 1370 | 980℃淬火 | M+共晶C+二次C+Ar | ≥58 | 火電廠球磨機襯板,雙進雙出球磨機襯板、球環磨得上下磨環與磨球、平盤磨的沖擊板、爐勾、護甲和葉輪 | |
-1480 | 480℃回火 | ||||||
30 | 1460 | 1370 | 980℃淬火,480℃回火 | M+共晶C+二次C+Ar | 58-60 | 4.0-6.0 | 水泥球磨機襯板; 火電廠球磨機襯板,雙進雙出球磨機襯板、球環磨得上下磨環與磨球、平盤磨的沖擊板、爐勾、護甲和葉輪 |
-1560 | |||||||
31 | 1500 | 1360 | 1050℃空冷或吹風,500℃回火 | M+共晶C+二次C+Ar | 58-60 | 5.0-9.0 | 水泥廠立磨磨盤襯板、立磨磨輥、立磨磨盤襯板;火電廠球磨機襯板,雙進雙出球磨機襯板、球環磨得上下磨環與磨球、平盤磨的沖擊板、爐勾、護甲和葉輪 |
-1380 | |||||||
32 | 1500 | 1360 | 1020℃淬火,450℃回火 | M+共晶C+二次C+Ar | 58-60 | 6.0-9.0 | 水泥球磨機隔倉板、立磨磨輥、立磨磨盤襯板;火電廠球磨機襯板,雙進雙出球磨機襯板、球環磨得上下磨環與磨球、平盤磨的沖擊板、爐勾、護甲和葉輪 |
-1380 | |||||||
33 | 1520 | 1420 | 1080℃淬水 | A | KV2/J | 冶金礦山球磨機襯板 | |
≥118 | |||||||
34 | 1520 | 1420 | 1100℃淬水 | A | HBW210-270 | ≥60 | 冶金礦山及水泥球磨機襯板 |
35 | 1520-1540 | 1420-1440 | 1100℃淬火 | A | 冶金礦山球磨機襯板 | ||
36 | 1520-1540 | 1420-1440 | 1100℃淬水 | A | 冶金礦山球磨機襯板 | ||
37 | 1520 | 1420 | 1100℃淬水 | A | 冶金礦山球磨機襯板 | ||
38 | 1520-1540 | 1420-1440 | 1100℃淬水 | A | 冶金礦山球磨機襯板 | ||
39 | 1520-1540 | 1420-1440 | 1100℃淬水 | A | 冶金礦山球磨機襯板 |
注:1、金相組織表示符號:M-馬氏體 Ar-殘余奧氏體 C-碳化物 B-貝氏體 A-奧氏體
2、表中幾種沖擊韌性的表示方法:1)αKU及αKN沖擊吸收能表示為J,沖擊韌性值KU為有缺口試樣試驗值,KN為無缺口試驗值。如αKU≥62J/cm2或αKN=58-86J/cm2;2)KN2或KU2:沖擊吸收能量的表示為J,U代表有缺口試樣的幾何形狀,N代表無缺口試樣,下標數字2表示擺錘刀刃半徑(單位mm)。例如:KN2≥25或KU2≥80。
7襯板選材與應用
(1)水泥廠球磨機襯板的工業應用
水泥廠球磨機有生料磨(即原料磨)與水泥磨(即熟料磨)。生料磨的物料主要是石灰石,而水泥磨物料有熟料、礦渣、石膏等硬度比石灰石高很多。在對襯板的新產品研制方面主要是針對水泥磨,水泥磨的新材質襯板都可以用于生料磨。相同材質用于生料磨使用壽命為水泥磨的四倍左右。因此用于水泥磨的各倉襯板材質均可對應用于生料磨。
從水泥廠球磨機襯板的磨損失效形式屬鑿削式磨料磨損,高應力疲勞磨料磨損及低應力擦傷磨粒磨損。可知水泥磨第一倉襯板要求高韌性、高硬度的、高抗磨材料,第二倉襯板要求高硬度、適當韌性的高抗磨材料。因此第一倉使用合金鋼及高鉻鑄鐵(鋼)材質較多,第二倉使用高鉻鑄鐵材質較多。合金鋼材質也可用于第二倉,但比高鉻鑄鐵使用壽命短。高鉻鑄鐵使用在第一倉時對于襯板設計塊小而厚的條件下可以使用,塊大而薄則可能導致開裂,存在一個襯板形狀設計與材質相匹配的問題。低鉻鑄鐵如BTMCr2有用于生料磨的,也可用于小型水泥磨第二倉的,由于沖擊韌性低,容易發生斷裂,耐磨性又不如高鉻鑄鐵所以現在用高鉻鑄鐵取代了它。高錳鋼在水泥廠球磨機中做襯板幾乎不用了,僅有用ZG120Mn13Cr2的。該鋼種中含ω(Cr)=1.5-2.5%,力學性能中屈服強度高,避免了襯板在使用過程中因發生塑性變形拉斷緊固螺栓而脫離筒體掉下的事故。中合金鋼ZG42Cr2Si2MnMoRE鋼在從日本進口的ф4.5×15.11m水泥磨第一倉使用壽命11年,該鋼種在國內設計的大型球磨機內做襯板一般使用3-6年,這是因為在磨機設計時對襯板形狀結構不同所致,進口的襯板塊小而厚,國產的襯板塊大而薄,在磨損率相同的情況下,薄的襯板使用壽命要比厚的短。高鉻鑄鐵(鋼)襯板使用比中、低合金鋼襯板壽命長,ZGCr13SiMo鋼襯板在從日本進口的ф4.5×15.11m水泥磨第二倉使用20年以上。一般大型水泥磨第一倉襯板BTMCr15使用壽命6-8年,BTMCr20、BTM26使用壽命8-10年。高鉻鑄鐵(鋼)襯板在水泥磨第二、三倉在十二年以上至20年。
(2)火電廠球磨機襯板的工業應用
球磨機襯板的磨損機理,因為球磨機用煤含有水份,球磨機入口處熱風為300-400℃,因此伴有氧化及腐蝕作用。因此球磨機的磨損失效機制是以鑿削式磨料磨損高應力疲勞磨料磨損及低應力磨傷磨料磨損為主,腐蝕磨損為輔。
磨煤機襯板材質多年來用高錳鋼ZG120Mn13,水韌處理后的初始硬度為HBW180-220,在磨煤機的工況條件下襯板殘體僅HBW250-360,不能發揮充分的加工硬化抗磨性能,且有塑性流變問題致使襯板殘體不易拆下,因而逐漸被淘汰。目前襯板安裝多采用組合自固型安裝結構,不漏煤粉、整體性好,維護少,安全可靠,加上新材質的應用提高球磨機襯板使用壽命,使磨機出力得到大幅度提高。在煤的磨損指數Ke>3.5為強磨損煤的粉磨物料情況下,ZG40CrMnSiMoRE鋼襯板在ф3m以上磨機使用壽命約為2年,ф3m以下磨機使用壽命約為3年;ZG40Cr5Mo鋼襯板在ф3m以上磨機使用壽命約為4年,在ф3m以下磨機使用壽命約為5年;BTMCr20鋼襯板在ф3m以上磨機使用壽命為6年以上;在ф3m以下,磨機BTMCr20襯板使用壽命為7年以上。
(3)冶金礦山球磨機襯板的工業應用
在濕法磨機襯板方面目前仍然應用高錳鋼較多,主要原因是適用性廣泛,安全可靠,生產制造工藝簡便。近卅年來,我國在研發低、中、高各類合金鋼在濕法磨領域取得可喜的進展。這些合金鋼在金相組織方面有奧氏體、馬氏體、馬氏體+碳化物、馬氏體+貝氏體、板條狀馬氏體等等。在對高錳鋼進行改造的研究與應用當中,加入Cr、Mo、W、Ni、RE、B等合金元素。有的是為細化晶粒、固溶強化提高高錳鋼的初始硬度,提高強度,提高屈服極限,有的是為了提高加工硬度速率以增加形變過程中的硬度;有的是在高錳鋼奧氏體基體上增加抗磨損的彌散碳化物第二相;有的是提高彌散碳化物第二相的硬度等均可以有效的提高耐磨性能等等,均取得比高錳鋼ZG120Mn13耐磨性好的實際效果。因此形成ZG120Mn13Cr2、ZG120Mn13W1、ZG120Mn13Ni3、ZG90Mn14Mo等牌號。冶金部鋼研究院研制ZG90Cr6MoRE鋼[7]做襯板、金相組織為馬氏體+碳化物,在福建潘洛鐵礦做運轉對比試驗該礦礦石以磁鐵礦為主,伴生黃鐵礦、赤鐵礦等。礦石硬度F=8-14。在ф4×14m濕式自磨機做兩種形狀襯板與高錳鋼襯板做對比試驗使用壽命分別提高1.31倍和1.21倍。
衡陽有色冶金機械廠與北京鋼研究院研制兩種新材料:ZG70CrMnMoBRE采用水淬空冷為馬氏體+貝氏體組織;
ZG35Cr2MnSiMoRE鋼[8]水淬回火為馬氏體組織。都在承德鋼廠選礦廠濕式球磨機做襯板與高錳鋼襯板對比試驗兩種
襯板材料使用壽命比高錳鋼提高0.6-1倍。ZG23Cr8Ni2MoRE襯板鋼[9]市合肥水泥研究設計院等單位完成的安徽省“九
五”科技攻關項目,該鋼種經噴霧淬火回火后,為板條狀馬氏體組織。該材料襯板整機在馬鋼姑山鐵礦ф2.7×3.6m
濕法格子型磨機上安裝使用,經與高錳鋼襯板對比使用壽命提高1.07倍以上,其力學性能大于雙五十,HRC>50,akn
>50J/cm2。ZG42Cr2Si2MnMoRE鋼經熱處理后是馬氏體組織,在國內制造的大型水泥磨做筒體襯板使用壽命為3-6
年,比高錳鋼筒體襯板使用壽命提高2-5倍。ZG42Cr2SiMnRE鋼在鐵礦濕法球磨機比高錳鋼提高1.25倍[10]。由此可
見,同一鋼種在干法水泥生產中做球磨機襯板使用壽命高,而在鐵礦濕法磨做襯板使用壽命低。這是鐵礦濕法磨礦
石硬度比水泥熟料硬度高而且有腐蝕作用所致。從上述應用案例來看,金相組織是奧氏體基體的耐磨性最差,奧氏
體基體雖然抗腐蝕性好,然而由于初始硬度低以及加工硬化能力不足抗磨損性低仍然差。而對基體為馬氏體、馬氏
體+碳化物、馬氏體+貝氏體、板條狀馬氏體哪一個組織最好,仍然難以定論,這決定于金相組織的抗腐蝕性能及抗
磨損特性的綜合效果。目前在性價比合適的情況下研究一種鋼鐵耐磨材料在水泥磨中襯板那樣在鐵礦濕法磨中比高
錳鋼耐磨性成倍增長的品種是我們努力的方向。
(4)金屬磁性襯板的工業應用
當鋼鐵耐磨材料襯板在濕法冶金礦山球磨機做襯板很難取得在干法水泥磨做襯板比高錳鋼襯板耐磨性成倍增長的時候,視線轉到了其他方面。在非金屬襯板方面主要是以聚氨酯和橡膠襯板為標志,雖然它們在某些性能方面優于金屬型襯板,但因抗滑動磨損能力差,為防止刻痕和撕裂而產生的早期失效,要求磨礦介質不能混入金屬夾雜物,工藝要求條件嚴格在一定條件下使用,而使普遍推廣受到限制。在研究開發轉向復合襯板方面以瑞典斯克嘉(SKEGA)為代表的鋼蓋式橡膠磁性復合襯板獲得廣泛應用。而我國則研發了具有中國特色世界首創的金屬磁性襯板,在上世紀90年代開始,由中國冶金礦業總公司北京金發工貿公司,原沈陽光大科研所與本鋼歪頭山鐵礦聯合開發研制了我國第一代第一套金屬磁性襯板發展到今天使金屬磁性襯板技術創新、完善,在鐵礦球磨機上,使用壽命達6-10年,為高錳鋼襯板使用壽命的6-10倍,已具有世界領先水平。金屬磁性襯板是一種具有自身保護功能的襯板,有以下特點:質量輕、易安裝、使用壽命長、節約資源、改善環境、降低成本、安全可靠。金屬磁性襯板結構是由金屬體(外殼)、永磁體和彈性膠層三部分組成。金屬體是襯板主要組成部分,其作用是保護永磁體層不受外力沖擊,并有足夠高的機械強度與導磁率,而殼體要有很高的磁感應強度。永磁體是襯板核心部分,其作用除吸附金屬體外,還要將自身吸附在筒體和端蓋上。彈性膠層粘接金屬體和永磁體,自身的彈性也起到緩沖作用。工作原理是在襯板工作面上方一定空間形成磁場,在磁場強度作用下凡是磁鐵礦物均可吸附在襯板工作面上,形成厚20-40mm的保護層,保護層可以是球磨機在運轉中磨削下來的鋼球碎塊或磨小的鋼球,也可以在初裝時加入此類介質。這個保護層在球磨機運轉過程中不斷更新處于動態平衡之中,使所有直接磨損卻產生于介質之間,從而使襯板工作面很少磨損,達到高效減磨的目的。它與傳統高錳鋼相比有以下優點[11][12]①使用壽命長為傳統高錳鋼的10倍;②節省球耗8-10%③質量輕,只有傳統高錳鋼的40%,減輕安裝的勞動強度,減輕磨機負荷,節電5-7%④厚度薄,約為傳統高錳鋼的70%,可使磨機有效容積增加,也就提高了磨礦能力;⑤安裝方便不用緊固螺栓,靠磁力吸附在筒體和端蓋上,不漏礦漿,提高作業率1%,實現文明生產;⑥機械性噪聲降低,改善了工作環境;⑦提高球磨機的粉磨細度,提高了磨礦效率;⑧實現零維護、降低成本,安全可靠。
國產悍馬牌金屬磁性襯板在選礦廠ф5米以上大型磨機得到廣泛應用。金屬磁性襯板在鞍鋼、本鋼、唐鋼、宣鋼、武鋼、寶鋼、昆鋼、邯鋼、邢鋼、馬鋼等近百家選礦廠應用取得可靠的經濟效益與社會效益。
金屬磁性襯板不僅在冶金礦山,而且在有色金屬及建材行業也得到推廣應用。金屬磁性襯板將有廣闊的發展長景。而鋼鐵耐磨材料襯板因有其本身的特點不斷發展而長期共存。
參考文獻:略
附件下載:

-
地址:濟南市解放路134號 電話:0531-86401781 / 86952422 傳真:0531-86465075
郵箱:foundry-shandong@163.com 郵編:250013
版權所有 © 山東省鑄造協會 魯ICP備2021002429號
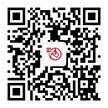
官方公眾號