會員登錄
MEMBER LOGIN
技術論壇
TECHNOLOGY FORUM
6MW 風力發電機組主機架、輪轂鑄件的研發和生產
發布時間:
2013-05-28 00:00
來源:
(浙江佳力風能技術有限公司,浙江杭州311241)
摘要:6MW 風力發電機組主機架、輪轂鑄件重達50 多噸,屬于特大型厚壁高韌性球墨鑄鐵件。本文分析了6MW 主機架、輪轂生產的技術難點,提出了解決方案,介紹了主機架和輪轂的鑄造工藝和生產情況,經理化檢驗和無損檢驗等,鑄件的各項技術指標完全達到相關技術規范的要求。
關鍵詞:特大型鑄件;高韌性球墨鑄鐵;厚大斷面球墨鑄鐵件;鑄造工藝
1 前言
近年來,風力發電在我國呈現出跳躍式的發展。據初步統計,2011 年,我國新增風電裝機容量接近1800 萬千瓦,總裝機容量達到6500 萬千瓦,已是世界上風電設備制造大國和風電裝機容量最多的國家,成為名副其實的風電大國。隨著陸地風場的不斷開發,我國又吹響了開發海上風電的進軍號,國內多家風電主機制造骨干企業都開始了海上風電機組的設計和生產。2011 年,我公司承接了一套6WM 風力發電機組主機架、輪轂鑄件的生產訂單,為國內某風電主機制造骨干企業的海上風電機組的樣機而生產的。這是我國制造的第一臺6MW風力發電機組。
6MW 主機架和輪轂的立體圖分別見圖1 和圖2。主機架鑄件重量58.48t,鑄件輪廓尺寸長5450mm、寬5400mm、高4580mm,鑄件主要壁厚100~120mm,最小壁厚90mm,最大截面厚度320mm;輪轂鑄件重量50.87t,輪廓尺寸長4485mm、寬3870mm、高4070mm,鑄件主要壁厚80mm,最小壁厚66mm,最大壁厚330mm。6MW 主機架、輪轂鑄件按照國家標準與歐盟標準設計、制造。其材料是牌號為QT400-18AL 的高韌性球墨鑄鐵,除了要求有良好的抗拉強度、屈服強度以及較高的伸長率外,還要求有良好的低溫沖擊韌性。對鑄件的金相組織也有很高的要求,不但要檢查附鑄試塊的金相組織,還要檢查鑄件本體的金相組織,要求球化率不低于3 級,鐵素體含量不低于90%,石墨大小4~6 級。除了理化檢驗之外,還要對鑄件進行磁粉探傷、超聲波探傷等無損檢測,對鑄件的內在質量、外觀質量以及壁厚尺寸等均有嚴格的要求。相關的驗收標準是,鑄件尺寸公差按照ISO8062 CT12;超聲波探傷按照:EN12680-3,2 級;磁粉探傷按照EN1369,2~3 級。
6MW 主機架、輪轂重量大,壁厚尺寸厚,形線復雜,屬于特大型球墨鑄鐵件,生產的技術難度較大。比如,主機架的平均壁厚約160mm,最大壁厚約400mm,是典型的厚大斷面球墨鑄鐵件。生產厚大斷面球鐵件常常出現石墨漂浮、石墨開花、碎塊狀石墨,以及石墨球數少、石墨尺寸大等問題。這些都直接影響到材料的力學性能,特別是低溫沖擊
性能。從鑄造工藝方面看,必須設計出適合的澆注系統和補縮系統,使鐵液充型平穩、快速,鑄件凝固均衡,補縮良好,防止鑄件出現沖砂、夾渣、縮孔、縮松等鑄造缺陷,獲得健全的鑄件,保證鑄件的內在質量和外觀質量能夠通過超聲波探傷和磁粉探傷的檢查。這需要解決很多技術難題。
2 生產工藝和主要生產設備
采用樹脂砂鑄造和電爐熔煉來生產6MW 主機架、輪轂。主要鑄造設備有l00t/h、60t/h連續式樹脂砂混砂機各一臺,7mx 8m、7mx 6m 振實臺各一臺,lOOt、80t、50t 行車各一臺,20t 一拖二中頻感應電爐一臺,30t 電動鐵水包2 個、20t 電動鐵水包1 個。
3 技術難點和解決方案
3.1 熔煉工藝
厚大斷面球鐵鑄件在澆注之后的冷卻凝固過程中,由于鑄件的壁厚尺寸大,冷卻速度緩慢,凝固時間長,在鑄件中容易出現球化衰退、石墨漂浮、石墨開花、石墨球數少、石墨尺寸大、碎塊狀石墨等問題。
一般認為,重稀土與輕稀土相比較,重稀土的抗球化衰退的作用更強,故提倡用釔基重稀土球化劑來生產厚大斷面球墨鑄鐵件。但對此也有不同的意見,認為在1300℃以下,重稀土的抗球化衰退作用并不比輕稀土強。我們決定采用經驗的做法,按照一定的比例,將重稀土和輕稀土的球化劑復合使用,來生產6MW 主機架和輪轂。
防止石墨漂浮的主要措施是控制好碳當量。風電球墨鑄鐵件,既風電鑄件的碳當量一般控制在4.30%~4.50%,考慮到6MW 主機架和輪轂的壁厚特別厚大,應當將碳當量控制在4.30%左右。
盡管通常認為石墨開花(或爆裂狀石墨)是伴隨著石墨漂浮產生的,但在實際的金相檢驗中會看到有石墨開花,卻并不伴隨石墨漂浮,我們更愿意將石墨開花歸入石墨畸變一類的缺陷之中。石墨畸變是厚大斷面球鐵中最常見、最難避免的一種缺陷。由于石墨球化理論的不完善,導致石墨畸變的機理也無定論。盡管如此,還是有一些行之有效的方法應用于球墨鑄鐵的生產之中,來解決石墨畸變的問題。抑制石墨畸變的措施主要有對原鐵水進行脫硫處理,以減少球化劑的用量。將稀土和鎂含量控制在相對較低的水平;在鑄件的厚壁處使用冷鐵等激冷物,增加鑄件的冷卻速度;控制鑄件的含硅量以及微量元素含量;加入少量Sn、Sb或Bi 等微量元素進行微合金化處理等。實踐證明,以上措施的綜合應用,可以有效防止厚大斷面球墨鑄鐵出現石墨畸變,并增加石墨球數。石墨大小和石墨球數都會影響到球墨鑄鐵的力學性能,在生產風電鑄件時要特別注意這兩項金相分析指標。要增加石墨球數,減小石墨大小,首先可以采用預處理工藝;另一方面要做好孕育處理,采用具有不同特點的孕育劑(比如含Ba、Ca 的孕育劑,含S、O 的孕育劑)進行復合孕育處理,要重視隨流孕育;再就是如前所述,用Sb、Bi 等微量元素進行微合金化處理。
3.2 鑄造工藝
風電鑄件一般采用底注式澆注系統。底注式澆注系統具有鐵液充型平穩,氧化小,型腔排氣順暢等優點,但不利于鐵液中的熔渣、砂粒等夾雜物上浮。充型后鑄件上部的溫度低于下部溫度,不利于補縮,澆注時間較長、澆注溫度過低的情況下容易在鑄件上部出現氧化皮夾雜物等缺點。6MW 主機架、輪轂鑄件的高度達4m 多,底注式澆注系統的缺點就更顯突出。根據6MW 主機架和輪轂重量看,都需要采用2 套以上的獨立澆注系統來進行澆注。這就可以將一套澆注系統采用底注式的,另一套澆注系統采用中注等其他方式。但存在一個問題,另一套澆注系統的注入位置不好確定。由于主機架和輪轂的特殊結構,除了底注之外,難于在鑄件上另外再找到一個合適的注入位置,能夠將鐵液平穩地、均勻地引入型腔。經過分析,最后決定全部采用底注式澆注系統。對底注式澆注系統的不足之處,則采用其他辦法來加以彌補。比如,適當的提高澆注溫度和澆注速度,采用發熱保溫冒口來提高補縮效率等。6MW 主機架和輪轂要進行超聲波無損檢測,必須對鑄件的縮孔、縮松缺陷進行嚴格的控制。首先,必須設計好鑄件的補縮系統。為了提高補縮效率,取得良好的補縮效果,采用冷鐵和冒口相結合的補縮系統。在鑄件的厚大部位和一些機加工面設置冷鐵,在鑄件的頂面設置冒口。在設計補縮系統時,用計算機進行凝固模擬,根據凝固模擬的結果和經驗來調整冒口、冷鐵的大小和位置。
6MW 主機架和輪轂鑄件的高度有4m 多,加上砂型和澆口盆的高度,整個鑄型高達7m多,鐵液的壓頭很高,容易發生脹砂、粘砂、跑火等鑄造缺陷。為了防止這些鑄造缺陷,需要適當增加型砂中樹脂的加入量,以提高樹脂砂的強度。在造型時使用振實臺來緊實型砂,提高砂型的緊實度,使用鋯英粉涂料,防止粘砂。由于主機架和輪轂的抬箱力都高達數百噸,除了采用常規的放置壓鐵、用螺栓緊固砂型的方法,還要用焊接圓鋼和鋼板,對砂箱的重要位置進行緊固和加固,以防止發生跑火。
3.3 其他方面的技術難點和解決方案
6MW 主機架和輪轂是在我公司剛剛竣工的年產6 萬t 的新工廠生產的。當時,鑄造設備還沒有全部安裝完成,設備能力略顯不足,特別是熔煉設備能力嚴重不足。為了解決這個問題,決定采用多開箱造型的工藝方案,設計專用砂箱,避免行車起吊超重。在熔煉時,先將熔化好的鐵液存放在鐵水包中,并采用保溫措施,再結合回爐加溫鐵液的方法,待所需要的鐵液全部熔化和加溫完畢,再同時進行球化處理。在生產之前,設計了幾套熔化、保溫和加溫的方案,以及球化處理后到澆注完成的最短時間的方案,通過多次試驗、確定了最佳方案。6MW 主機架和輪轂鑄件的形線復雜,壁厚不均且尺寸要求嚴格。木模形狀尺寸必須準確,制作難度較大。必須應用三維CAD 技術,用數控木工機床制作木模。
4 鑄造工藝、生產情況和質量檢驗
4.1 主機架、輪轂的鑄造工藝
6MW 主機架的鑄造工藝簡圖,見圖3。采用了3 套獨立的底注式澆注系統,直澆道和內澆道采用陶瓷管。計算的澆注時間為154s,最小阻流截面積240cm2,澆注系統各組元的比例為Σ直:Σ阻:Σ橫:Σ內:=1.5:1:2:1.6。在鑄件的頂面設置4 個Φ230mm 的鴨嘴冒口和一個直徑Φ300mm 的發熱保溫冒口,在鑄件的機加工面和一些厚大斷面部位放置冷鐵,多開箱造型。6MW 輪轂的鑄造工藝簡圖,見圖4。采用了2 套獨立的底注式澆注系統,直澆道采用陶瓷管,內澆道采用披縫式澆口。計算的澆注時間為140s,最小阻流截面積200cm2,澆注系統各組元的比例為Σ直:Σ阻:Σ橫:Σ內:=1.13:1:2:1.5。在鑄件的頂面設置3 個Φ300mm的發熱保溫冒口,并在機加工面和厚大斷面處放置冷鐵,多開箱造型。
4.2 熔煉工藝
用中頻感應電爐進行熔煉。爐料采用國產高純生鐵、低碳鋼廢鋼以及風電鑄件的回爐料,用沖入法進行球化處理,孕育處理的方法采用包內孕育和隨流孕育,并進行了預處理和微合金化。球化劑和孕育劑的化學成分見表1。6MW 主機架的澆注重量為85t,同時處理3 包球墨鑄鐵進行澆注。輪轂的澆注重量為64t,同時處理2 包球墨鑄鐵進行澆注。
4.3 生產情況和質量檢驗
經過生產現場測量,主機架的實際澆注時間為144s,三包鐵液的澆注溫度分別是1319℃、1320℃、1337℃;輪轂的實際澆注時間為125s,兩包鐵液的澆注溫度分別是1318℃和1345℃。
主機架和輪轂鑄件均在澆注之后冷卻196h 以上開箱,開箱溫度不大于300℃。最后,對6MW 主機架和輪轂鑄件進行了形狀尺寸檢驗、表面質量檢驗、超聲波探傷、磁粉探傷、理化檢驗以及本體金相分析。力學性能試驗是用厚70mm 的附鑄試塊制樣進行試驗的。所有的檢驗結果均達到技術規范的要求。其中,力學性能檢測的結果見表2,附鑄試塊的金相分析照片和本體金相分析照片分別見圖5—圖8。金相照片的放大倍數均為100 倍。
5 結束語
厚大斷面球墨鑄件的生產一直存在許多難題。采用電爐熔煉,樹脂砂鑄造,底注式澆注系統,多開箱造型,將輕稀土和重稀土球化劑組合進行球化處理、復合孕育處理、預處理、微合金化等技術方法,成功生產出重達50 多噸的6MW 風力發電機組的主機架和輪轂球墨鑄鐵件。目前,主機廠已經完成了6MW 主機架和輪轂的組裝,風力發電機組成功下線。
(摘自《2012 中國鑄造活動周論文集》)
附件下載:

-
地址:濟南市解放路134號 電話:0531-86401781 / 86952422 傳真:0531-86465075
郵箱:foundry-shandong@163.com 郵編:250013
版權所有 © 山東省鑄造協會 魯ICP備2021002429號
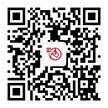
官方公眾號