會員登錄
MEMBER LOGIN
技術論壇
TECHNOLOGY FORUM
進一步發揮感應爐熔煉優勢提升鐵液質量
發布時間:
2013-09-04 00:00
來源:
錢 立
(河北工業大學,天津300021)
多年來,采用感應爐已經成為鑄造企業技術改造、產品升級的主要措施之一。不僅眾多中小企業(尤其是多牌號生產)青睞感應爐,就是生產風電鑄件的大型工廠亦改為多臺中頻爐協同作業的方法。最近,玉柴集團打造世界最大的柴油機鑄件生產基地,其鑄造中心采用了單一感應爐熔煉,在保證質量的基礎上,降低了爐料成本,減少了生產工藝和生產人員。
1 感應爐熔煉采用無芯中頻爐
感應爐有有芯和無芯之分。感應爐熔煉應采用無芯爐。無芯爐變更鐵液品種方便,可以冷爐料起動,提溫迅速,生產率高,電磁攪拌作用好,筑爐修爐方便。頻率采用中頻范圍。與工頻爐相比,無需開爐塊;功率密度大,起動和熔化快,節約電耗;功率可無級調節,且可在不同爐體間任意分配;可自動變頻以適應爐料參數的變化;攪拌力度和“駝峰”可控;對爐料塊度并無苛求,從塊料到切屑均可。一般頻率隨爐子容量的增大而減小,例如0.1~60 t 爐子,頻率在2500~150 Hz。近年來,IGBT 半橋串聯逆變中頻電源因其負載適應范圍寬,熔煉過程中可保持恒功率運行,電源功率可以共享等高性能特點,在中型和小型爐子上得到了廣泛應用。
熔煉灰鑄鐵和球墨鑄鐵時,采用酸性爐襯,爐襯材料來源廣、價格較為便宜。天然石英砂最高工作溫度為1 650℃,熔融石英砂則為1 660℃。
工頻有芯爐適宜作保溫爐或澆注爐使用。某廠沖天爐鐵液連續流入立式有芯爐,有芯爐根據造型澆注線的需要隨時出鐵。因此對于頻繁出鐵和平衡鐵液供求關系十分有利。國外某廠是一個大沖天爐分別供應了3 個有芯保溫(儲存)爐,再由鏟車轉運鐵液至氣壓澆注爐進行澆注。有芯保溫爐爐膛密封性好、元素燒失極少。作澆注爐使用時能準確控制澆注溫度和澆注量。
本文以下提到的感應爐均指無芯中頻感應爐。
2 感應爐熔煉的優勢
感應爐熔煉具有以下優勢[1]:
(1)感應爐熱量產生于爐料內部,無需外界傳導,因而熱效率高,加熱速度快。
(2)鐵液過熱度容易調節,出鐵溫度高。
(3)元素燒損少,鐵液中氣體含量和非金屬夾雜物少。沒有沖天爐鐵液的焦炭硫污染問題。
(4)由于電磁攪拌作用,鐵液的化學成分和溫度均勻。
(5)熔煉工藝穩定、易控,鐵液化學成分準確。
(6)可以多用或全部使用廢鋼,用增碳的方法生產合成鑄鐵。
(7)切屑和邊角碎料等細小的難以在沖天爐內直接利用的廉價廢料,在感應爐內借助電磁攪拌作用,很容易卷入鐵液而迅速熔化,而氧化損耗卻較少。若裝料期加入,因切屑粒度小,感應電流分布于整個切屑的斷面,熔解較快,但燒失較多。
(8)感應爐的煙氣和粉塵較少,噪音小,作業強度低,環保治理比較方便。
(9)生產安排靈活,開爐、停爐方便。
(10)容易實現自動化管理。
然而,感應爐熔煉亦存在一些不足和問題。如不能了解其冶金特點,采取相應的操作對策去揚長避短是難以獲得優質鐵液的。此時,非但不能得到所需的金相組織,還會惡化切削加工性能,產生某些收縮缺陷等。
3 感應爐熔煉的冶金特點
感應爐的冶金特點與沖天爐不同。
(1)沒有氧化性的燃燒爐氣,又是采取批料間歇熔煉,因而元素損失少,化學成分準確、穩定。
(2)電磁攪拌作用在一定程度上有利于非金屬夾雜物的合并、上浮,并增加了與熔渣接觸機率而為熔渣所收容。同時亦有利于鐵液中溶解的H、N、O 的排除。
(3)熔渣不能感應發熱,渣溫低。加之坩堝的高徑比大,又沒有沖天爐內鐵滴與渣滴交互接觸的機會。因此,熔渣內物理化學過程不活躍,熔渣的冶金功能極為有限。熔渣主要起覆蓋保護和一定程度的收容夾雜物的作用。
(4)感應爐熔煉后期,隨著鐵液溫度的升高,當達到所謂平衡溫度以上時,發生以下反應:
SiO2(爐襯)+2[C]→[Si]+ 2CO↑
( SiO2)(液中)+2[C]→[Si]+2CO↑
此時,對FeO、MnO 有類似的反應。感應爐內C 的還原作用是沖天爐無法比擬的。發生上列反應的條件一是高溫,二是缺氧和沒有氧化性氣氛。沖天爐爐缸里只有在濕底(爐缸不過空氣)時,才能滿足Si、Mn、Fe 從氧化物中被C 還原的條件。沖天爐的爐缸較淺,鐵液流經爐缸的時間比較短暫,反應沒有感應爐內從容、充分。C 作為還原劑,產生的CO 造成熔池“自沸騰”,對鐵液起到了脫氣除雜的凈化作用。
(5)鐵液的過冷傾向大。圖1[2]表明,在相同CE 下,感應爐鐵液的共晶過冷度比沖天爐鐵液大。這是由于:①高溫下,鐵液中由生鐵和回爐料帶來的石墨的減少和消溶;②熔煉后期,鐵液中SiO2 因與C 反應,而使可作為外來晶核的SiO2 減少,乃至喪失;③感應爐鐵液的[S]、[O]明顯低于沖天爐,一般[S]<0.05%,[O]<0.001 5%。如此低的O、S 含量,對于灰鑄鐵來說,是難以指望硫氧化物的外來晶核作用了。
鐵液過冷傾向大,將導致以下情況出現:灰鑄鐵中出現過冷石墨,甚至產生自由滲碳體;將使球墨鑄鐵出現麻口組織、并減少石墨球數量;產生自由滲碳體的結果,使鑄鐵縮松縮孔傾向增大;使薄壁灰鑄鐵件出現滲漏;使切削加工性能惡化,降低機加工工效,增加刀具損耗,提高加工費用,這是用數控機床或加工中心大批量生產企業所十分忌諱的。
4 感應爐優質熔煉的控制要點
4.1 把化學成分控制工作做細
雖然與沖天爐相比,感應爐有元素燒失少,化學成分準確、穩定的先天優勢,但如果后天失調,這個先天優勢是會打折扣的。準確控制化學成分還需有四個前提。
(1)用凈料 爐料雜亂、不干凈、銹蝕多,則元素燒失增大,也無法使燒失穩定。此外,感應爐爐渣的冶金功能差,也要求爐料純凈,嚴防P、S、O 和微量元素含量不明。
(2)準確配料 根據元素的燒失規律,正確進行配料。特別不要忘記把熔煉后期的脫C 量考慮在配C 量之內。配料不準確,會延長熔煉時間,增加能耗。
(3)配備多功能熱分析儀和直讀光譜儀 及時掌握化學成分和凝固等信息,進行爐內或爐前調劑。當感應爐與沖天爐或高爐雙聯時,適時而準確的測報更為重要。
(4)把握火候,控制好終點 關于終點溫度和時間的控制,后敘。
4.2 合理加料
七手八腳、胡亂加料、野蠻加料的現象,在一些工廠常有發生。有些“規程”只側重于操作性的表述,如①爐底墊輕薄料;②料塊要合理,切忌厚大(電頻率在100~500 Hz 時,最佳平均料徑為230~100 mm);③裝料要緊密,但不能在熔化期發生棚料,等等。這些規定,對于保護爐底免受撞擊和過熱,爐料順行和熱利用,無疑是必要的。然而,從冶金學視角考慮,強調以下幾點更為重要。
(1)爐料裝入順序,應保證爐底盡早形成高碳熔池。令熔點低的回爐料先裝,再裝生鐵,熔點高的廢鋼裝在其上。這樣,供電后爐底很快便形成熔池,廢鋼浸入其中,表面因增C 而降低熔點,起到了助熔作用。還必須指出,廢鋼比生鐵易于氧化,當溫度高于700℃以后,廢鋼表面氧化加速。若廢鋼能盡快熔于鐵液,無疑對于減少氧化也是有益的。
化學成分對于熔點的影響是基于Fe-C 相圖中液相線的變化:隨著C 含量的提高,鋼的熔點降低。同樣的道理,一些高熔點鐵合金,可以利用表面增Fe,降低液相線溫度,來達到助熔的目的。筆者在熔煉有Mo、W、B、V 等的鑄鐵時,較早地將FeMo、FeW、FeB、FeV投入熔池,起到了助熔作用。借助電磁攪拌作用,鐵液成分很快就均勻了。
(2)熔煉初期切忌底部熔池過熱,以免爐底因發生SiO2(爐襯)+2C=Si+2CO 反應而致的化學侵蝕。鐵液的過熱還會加劇元素的燒損和含氣量的增加。
(3)隨著爐料的逐步熔解,應適時適度續料,前一批料尚未化盡前,投入后續料。投向熔池的爐料要干燥、無銹蝕,以防鐵液氧化和氣體含量增加。在冬季,往熔池加冷廢鋼,會“炸濺”,產生安全事故。切屑宜加入熔池。裝料期加,會加大元素燒損。
(4)裝料初期應隨著加金屬料,加入適當的造渣劑(清渣劑),使爐底的熔池早早處于熔渣的保護之下。以后,在熔化期視需要,再補充渣料;爐料熔清后,可扒渣,再造渣。總之,熔煉過程中,提前造渣,造好渣,補渣換渣,是不可忽視的環節。
4.3 精益凈化
研究表明,僅僅關注鑄鐵的基本化學成分和組織是不夠的。鑄鐵性能的發揮和鑄件的失效,往往與鑄件中的鑄造缺陷、組織缺陷、某些同溶元素和晶界脆性相的存在密不可分。而所有這些,多數與鑄鐵中的非金屬夾雜物及氣體有關。因此,必須發揮感應爐內的精益凈化作用。
電磁攪拌有助于金屬料和增碳劑的加速熔解吸收,使化學成分和溫度均勻化,也有利于脫氣和去除非金屬夾雜物。但脫氣和去雜的作用是有限的。感應爐多采用單相供電,產生如圖2 所示的兩段四區電磁攪拌。由圖可知,下部兩區對于夾雜物的上浮有一定的抵消作用,也削弱了電磁攪拌的脫氣作用。
平衡溫度是決定反應SiO2+2C=Si+2CO 方向的溫度。當溫度大于平衡溫度時,反應向右進行,反之則反應向左進行。單質狀態下,平衡溫度為1 645.8℃。鐵液中的C 含量和Si 含量影響平衡溫度:隨著C 含量的增加或Si 含量的減少,平衡溫度降低。在通常灰鑄鐵或球墨鑄鐵鐵液成分下,平衡溫度約在1 425~1 400℃,對于低溫用鐵素體球墨鑄鐵則約在1380℃左右。當熔池溫度高于平衡溫度時,反應產物CO 造成熔池沸騰。生產中為了保證足夠的沸騰力度,一般取平衡溫度以上50℃,稱作沸騰溫度。CO 造成的沸騰是發生于整個熔池的,CO 是往上逃逸的。因此,其凈化作用是電磁攪拌無法比擬的。利用熔煉后期熔池的“自沸騰”凈化是感應爐熔煉的一大特色。通過“自沸騰”能很好地降低鐵液中H、N、O 的溶解量,并在氣泡上浮過程中,攜帶非金屬夾雜物進入熔渣。
吹Ar 凈化是一種有效的輔助手段。通常可采用爐內或包內插管吹Ar 或爐底透氣磚吹Ar,亦有在爐底安置氣體擴散器,再在其上搗搐特定的耐火材料層,令Ar 通過這一可透氣的燒結層達到凈化目的。
研究表明,除N 是除氣的重點。降低鐵液中的N,不僅可以免除N 氣孔,更主要的是提高球墨鑄鐵,乃至提高抗磨白口鑄鐵的韌性。
除了以上的方法可以除N 外,還有吹O2 或吹CO2 除N 和脫N 劑脫N 等的試驗與實踐。
4.4 防止后期H、N、O 回升即便進行了凈化處理,如果此后操作不當,H、N、O 仍有回升的可能。為此,須特別注意幾點。
(1)后期不能投潮濕的物料。
(2)選用O、N 低的增C 劑。
(3)電磁攪拌力與輸入功率成正比,與頻率的平方根成反比。加入增C 劑后,一般可用調低頻率的方法,促使增C 劑的溶吸。但攪拌力度(尤其是在無熔渣覆蓋的情況下)不能過度。否則,“駝峰“高,氧化吸氣風險大。
(4)“自沸騰”或吹Ar 等處理不能過于激烈。
(5)鐵液化學成分和溫度合格后,停電扒完渣,要盡快傾爐出鐵。出鐵最好一次完成。分包出鐵或遇意外情況,要對剩余鐵液供電保溫,無渣保護的鐵液,氧化燒失和吸氣問題會突出起來。
4.5 正確控制終點
爐料熔清后,熔池升溫加快,經過平衡溫度、沸騰溫度、臨界溫度,而達到過熱溫度。所謂臨界溫度是指當超過這一溫度時鐵液中石墨核心數明顯減少,鐵液白口傾向增大,鑄件或試樣中石墨形態發生變異,產生過冷石墨甚至出現自由滲碳體。不同資料所提供的臨界溫度數據不甚一致,一般為1 455~1 510℃。臨界溫度與爐料狀況及鐵液化學成分有關,如生鐵牌號高則臨界溫度高;廢鋼配比多,生鐵用量少則臨界溫度低;鐵液C、Si 含量低則臨界溫度低等。此外,使用什么樣的增C 劑也影響到臨界溫度。熔煉最終的過熱溫度視鑄鐵材質、鑄件體量大小,以及爐料等情況的不同而定,一般為1490~1 550℃。
經過1 490~1 550℃過熱的鐵液,淡化了爐料的不良遺傳性影響,也加大了過冷傾向。但只要作好預處理和孕育處理,孕育效果會發揮得更好,有利于石墨和基體的細化。必須強調,過熱溫度切忌隨意提高。必須指出,在過熱溫度下停留時間不能長。否則會產生“死鐵液”(這種情況常在夜班保溫,第二天早班使用的鐵液中發生)和H、N、O 回升的現象。
4.6 預處理
感應爐鐵液的自發形核能力差,白口傾向大,必須認真做好孕育處理。與相同化學成分的沖天爐鐵液相比,感應爐鐵液的孕育量要多出0.1%~0.2%。對于高質量的鑄件,出鐵前還應該在爐內進行預處理。晶型石墨和SiC 的形核能力強,是應用最普遍的預處理劑,其次是孕育級的硅鐵。
此外,還可在包內進行預處理。爐外預處理技術可查有關報道。對灰鑄鐵而言,感應爐鐵液的S 含量低,不利于孕育形核。需將提高至0.07%~0.10%。因此,從廣義的預處理概念上講,鐵液增S 也是一種預處理。FeS 的熔點為1 193℃,它能全部溶于鐵液。S 的回收率視加入時機和加入狀況而定,熔煉后期鏡面加入時回收率可高于90%,裝料期加入則回收率降低。為了降低費用,有的工廠使用黃鐵礦增S。
4.7 節能快熔
“十二五”期間,單位 GDP 能耗要降低16%。節能減排已被列入地方政府官員的業績考核之中。熔煉工部節能是企業節能的重中之重。感應爐節能快熔可采取以下措施網。
(1)提高比功率,以實現高的電效率和高的熱效率并實現快速熔煉。目前0.5~60 t 爐子的比功率設計為1 000~600 kW/t。
(2)一拖二,即一套電源同時向兩個爐體供電,功率在兩個爐體間任意分配。整個熔煉過程以恒功率運行,功率利用系數幾乎可達100%。
(3)盡量安排在較大容量的爐子上熔煉。據測算,5t 爐比2t 爐的噸鐵電耗可減少3%~4%。
(4)作業制度上,采取連續熔煉。
(5)增設爐蓋,并減少開蓋率。帶蓋作業與敞口作業相比,液面熱損耗功率可降低50%~60%。
(6)使用凈料,禁止銹蝕料和含坭帶砂料入爐。
(7)掌握爐料成分,準確配料,免除成分超標而導致的不必要的調整工作。
(8)設法縮短裝料、熔化、取樣和檢測時間,提高功率利用率。
(9)避免終點鐵液溫度過高。否則不但多耗電,還增加了降溫時間。爐內靜止降溫很慢,3t 爐在無覆蓋的情況下,每分鐘降溫不超過3℃。
(10)采用優質爐襯材料,延長爐齡。
(11)在保證爐齡的前提下,爐襯不宜過厚。因為壁厚增加會降低電效率和感應器的輸入功率,降低了生產效率,而且由于不易形成良好的初期燒結層,致使初期熔蝕加快。坩堝壁厚與爐子容量及坩堝直徑的關系見表1。
注:d 為坩堝的平均直徑。
(12)合理的坩堝絕熱層厚度。為了減少坩堝壁的散熱,需要一定厚度的絕熱層。但絕熱層增厚時,絕熱層內側溫度上升,會使燒結層或半燒結層擴展而縮小松散層。一般絕熱層厚度取5~7 mm。一旦要增加絕熱層時,搗打料中的膠結劑加入量應減少。
(13)調度上要避免感應爐被迫等待造型的情況。
(14)熔煉工部天車配置要合理,防止熔爐等天車而造成窩工。在采取以上種種措施后,先進的指標可達到:電耗580~540 kW/t;連續熔化,冷料至1500℃鐵液的熔煉時間為35~54 min/爐。
5 減少事故的措施
感應爐熔煉過程中出現的事故和問題,大多來自感應爐系統(中頻電源及爐子)和爐臺操作。好的感應爐系統可以免除許多煩惱,減少維修費用和停工損失。
5.1 正確配置感應爐系統
國內多家公司生產的感應爐已相當完善,達到無故障設備的水平。因此,有相當規模的鑄造企業應從這些公司中尋找供貨商,它們會提出詳細的項目書。該感應爐系統對電源、爐體、傾爐系統和水冷系統等進行顯示、報警、診斷和故障處理。根據爐內變化著的情況,變頻器會處于高效運行狀態。一個高度自動化的感應爐,人工操作僅限于接通電源、開啟變頻器和調定輸入功率,無需設專人看守變頻器或作其他操作調節。如果鑄造企業受生產量和經濟條件所限,在感應爐技術改造時,應聽取行業組織和專家的建議,并向供應商重點了解幾種情況:①所用可控硅、控制板、集成塊、元器件、絕緣材料以及液壓缸、水泵、冷卻設備等輔機的來源和配套情況;②配件庫的狀況;③服務能力和響應速度。
筆者發現,有鑄造廠喜歡就近就熟(熟人)購買“便宜貨”。這些供應商主要生產爐子,其余是“串起來”的。而且2t 爐還用鋁殼。試想,這樣的系統可靠性、耐用性會是怎樣?按照國家發改委鏟業結構調整指導目錄(2011 年本)》規定,無磁軛(≥0.25 t)鋁殼爐屬于淘汰類產品。用鋁殼爐也有違工信部《鑄造行業準入條件》中,關于企業生產裝備的要求的。
5.2 正確進行爐臺操作
爐臺操作不當,容易造成爐料搭棚,爐底熔池過熱,“大象腳”和漏底等事故。這些事故多與爐料尺寸過大、野蠻裝料、爐襯材料及燒結工藝不當、鐵液過熱溫度過高,以及爐襯修補不及時等有關。企業管理者,不能把爐臺操作看作體力活,一定要加強崗位培訓,提高員工素質。
耐火材料的生產公司很多,著名的公司都有很好的服務,如推薦適用的耐火材料及輔料,指導筑爐和爐襯燒結,并對最低爐襯使用壽命做出保證等。
5.3 及時的信息測報
對鐵液的化學成分和凝固信息要作爐前測報,以便及時指導生產,防止鑄件質量事故。直讀光譜儀的標準曲線,過一段時間應重新做,這是因為曲線會漂移,而且國產標樣,其深層成分與淺層成分也會有所不同。熱分析儀也應該定期校驗。化學分析法雖然慢,用作爐后分析,準確性高。C、S、P、Mg 等對光譜分析操作手法很敏感,應該用化學分析的結果進行比照。
(摘自:《鑄造》)
附件下載:

-
地址:濟南市解放路134號 電話:0531-86401781 / 86952422 傳真:0531-86465075
郵箱:foundry-shandong@163.com 郵編:250013
版權所有 © 山東省鑄造協會 魯ICP備2021002429號
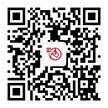
官方公眾號