會員登錄
MEMBER LOGIN
技術論壇
TECHNOLOGY FORUM
【成功案例】重型卡車平衡軸支座結構優化
發布時間:
2022-03-29 20:06
來源:
前 言
本案例針對平衡軸支座在道路試驗過程中發生斷裂的問題,通過理化分析和鑄件解剖,查找出斷裂原因為鑄造缺陷引起,并對平衡軸支座結構和鑄造工藝進行優化設計。采用有限元方法和AnyCasting數值模擬方法分析了該零件在整車不同工況下的應力大小及應力分布情況及鑄造工藝的可行性。結果表明,平衡軸支座結構優化后可滿足整車強度需求,鑄造工藝改進后消除了鑄造缺陷。經實車試驗,驗證了平衡軸支座的可靠性,并對鑄件設計流程進行了總結和規范。
1 平衡軸支座結構優化
1.1 平衡軸支座斷裂原因分析
某重卡自卸車完成整車及零部件設計后,為了驗證整車滿載情況下各零部件的使用性能,對此輛樣車安排10000 km道路試驗。但是,道路試驗進行到1000 km時,即出現平衡軸支座斷裂現象。斷裂發生在平衡軸支座圓軸根部,斷裂處局部及斷口形貌見圖1。斷裂處附近錐度表面環向約1/2區域有磨損,漆膜被完全磨掉,露出零件金屬色,其余部位漆膜基本完整。斷口較不平整,被泥漿覆蓋,簡單清洗后可見斷口上有明顯的鑄造缺陷,缺陷面積約占整個斷面的50%。
在失效零件斷裂處附件進行微觀檢查,該區域石墨球化及大小均無異常,基體組織呈明顯的枝晶分布,基體為中等片狀珠光體+鐵素體+少量碳化物,珠光體有偏聚現象,檢查面上可見微觀疏松。石墨形態、微觀疏松及基體組織見圖2。經檢測平衡軸支座斷裂處附近基體硬度平均為HBW 211(公司內標準要求160~230),符合標準要求。為了進一步確認平衡軸支座內部確實存在鑄造缺陷,對該鑄件按照原鑄造工藝重新進行生產,鑄件毛坯經簡單清理后,將平衡軸支座從軸的中間部位鋸成兩半,解剖后的結果看到平衡軸支座軸根部確實存在縮孔鑄造缺陷,且縮孔位置與斷裂件缺陷位置基本一致(圖3)。平衡軸支座斷裂失效的主要原因為:失效零件斷裂處存在嚴重的鑄造缺陷,使其局部承載能力顯著下降,導致整車試驗過程中引發斷裂事故。
1.2 平衡軸支座結構優化
結合鑄造工藝及存在的缺陷問題,對平衡軸支座原結構進行詳細分析,發現在軸根部位置壁厚較厚,導致軸根部形成較大的熱節,且中間位置布置的圓環形加強筋也在軸根部,不利于此處砂芯的排氣,因此造成鑄造過程中易產生縮孔缺陷。結構優化主要以減輕壁厚、調整腔體結構為平板布置加強筋、優化圓軸根部圓環形加強筋的布置為主,以此來縮小圓軸根部的鑄造熱節,從而避免鑄造縮孔傾向。
1.3 改進后平衡軸支座結構靜力學分析
在Hypermesh中建立平衡軸支座與車架的有限元模型,設定平衡軸支座原材料為球墨鑄鐵QT500-7,彈性模量2.1×105 MPa,密度為7.8 g/mm3,泊松比為0.28。重型卡車在實際使用過程中板簧和車架對平衡軸支座施加的外載荷較大且種類很多,在設計過程中主要考慮四種工況,分別是垂直加速度、轉彎、車架扭轉和制動,分析平衡軸支座在各種工作環境中整體的剛度、強度和安全系數性能,為設計提供理論指導。
1.4 平衡軸支座改進方案鑄造工藝分析
利用AnyCasting軟件對平衡軸支座鑄造時金屬液充型和凝固過程進行數值模擬分析,以此分析結果初步確認平衡軸支座改進方案是否可避免鑄造缺陷,并為鑄造工藝設計提供參考。平衡軸支座采用的是濕型砂鑄造工藝,前期試制階段制作木模1套(包括芯盒3套),改進后的平衡軸支座鑄造工藝與原方案基本一致。考慮原方案鑄造存在缺陷風險,此次在鑄造工藝中增加設置2處外冷鐵及補縮冒口,鑄造工藝簡圖如圖7所示。
根據上述鑄造工藝設計,在AnyCasting軟件重建立平衡軸支座分析模型,設定分析條件并進行數值模擬分析,結果顯示,鑄件最終凝固位置位于冒口中,從數值模擬分析角度確認圓軸根部的鑄造缺陷已得到解決。
其次,對該鑄件重新制作模具,進行鑄件試生產后,對鑄件進行實物解剖,解剖后可以看到,鑄件內部組織致密,沒有發現鑄造缺陷,此結果與AnyCasting鑄造工藝數值模擬分析結果一致(圖8)。
平衡軸支座改進前后方案,各工況下安全因子結果見表4。平衡軸支座改進方案結構靜力學分析最小安全因子均>1,工況計算合格;各工況下最大應力比原方案均有降低,安全性能得到了極大提高。結構優化和工藝改進,鑄造工藝性優于原方案,重量比原方案減輕10%,鑄件制造成本降低10%。
1.5 鑄件類產品設計規范
為了規范鑄件類產品設計統一,加快鑄造和機加工單位的生產節奏,節省生產成本,根據設計人員的設計經驗,總結本次平衡軸支座改進優化過程,并在公司內部發布《鑄件類產品設計規范》,為公司內鑄件類產品設計過程提供參考。鑄件設計流程見圖9。
2 結束語
通過對平衡軸支座斷裂失效原因進行深入研究和分析,準確地查找到導致平衡軸支座斷裂的原因為鑄造缺陷引起。根據鑄件缺陷原因確定結構改進優化方案,改進后的方案經鑄件靜力學分析、鑄造工藝數值模擬分析及實物驗證,消除了鑄造缺陷,并在后續的30000 km試驗中未出現失效現象,保證了整車的使用性能和可靠性。平衡軸支座改進方案安全性能得到了極大提高。結合平衡軸支座設計改進過程,在公司內部發布《鑄件類產品設計規范》,在鑄件設計流程中引入鑄件靜力學分析和鑄造工藝數值模擬分析過程,統一規范鑄件設計過程,提高新產品鑄件設計開發質量和正確性,從而縮短新產品研發周期。
作者簡介:
李運成(1979-),男,工程師,主要從事汽車鑄件結構設計、優化、分析及鑄造工藝的研究,陜西重型汽車有限公司
本文節選自《鑄造》Vol.68 No.11 2019《重型卡車平衡軸支座結構優化》
附件下載:

-
地址:濟南市解放路134號 電話:0531-86401781 / 86952422 傳真:0531-86465075
郵箱:foundry-shandong@163.com 郵編:250013
版權所有 © 山東省鑄造協會 魯ICP備2021002429號
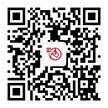
官方公眾號