會員登錄
MEMBER LOGIN
技術論壇
TECHNOLOGY FORUM
汽車鑄件輕量化的技術路線分析
發布時間:
2022-03-30 15:14
來源:
汽車鑄件輕量化的技術路線分析
摘要:根據國內、外汽車鑄件研發及應用情況,從鑄造材料研發與替代、鑄件結構輕量化設計、鑄造工藝進步3個方面分析汽車鑄件輕量化的技術路線。首先介紹了高性能鑄造材料及輕質鑄造合金在汽車零件輕量化上的最新發展趨勢與應用成果;以實際零件為例,列舉了鑄件輕量化設計過程中常見的薄壁化、空心化、集成化3種結構優化方案及輕量化效果;針對輕量化鑄件的生產問題,簡述了熔模鑄造和(真空)高壓鑄造成型工藝在汽車輕量化鑄件上的應用。
關鍵詞:輕量化鑄造技術路線
汽車自身質量大小是影響燃油消耗,降低污染物排放的重要因素之一。當前,鑄件占國產汽車質量的10%~20%,其中商用車鑄件約占整車質量的20%,乘用車鑄件約占整車質量的10%,為汽車零部件重要構成之一。因此,汽車鑄件輕量化對降低整車質量,減少污染物排放具有重要意義。從目前汽車鑄件輕量化的發展趨勢來看,其技術路線可從鑄件材料替代、鑄造技術進步及產品結構優化3個方面實現。
一 鑄造材料替代
1.1高性能鑄造材料在汽車零件上的應用
對于傳統鑄鐵、鑄鋼而言,可通過微、低合金化,鑄造工藝控制及鑄后熱處理等手段提高材料強韌性,從而提升性能。例如,通過微、低合金化及熔煉過程控制研發的QT800-5、ZGD1240-1450,通過施加等溫淬火處理獲得的等溫淬火球墨鑄鐵(Austempered DuctileIron,ADI)等。
1.1.1 高強韌鑄態球墨鑄鐵的研發與應用
大部分汽車鑄件為砂型鑄造的低強度球墨鑄鐵件。該材質具備制造成本低,工藝成熟度高的優點,但存在材料綜合性能低、外觀質量差等不足,制約了汽車零件的輕量化設計。而國外先進車企通過不斷研發,逐步提升球墨鑄鐵性能,拓展了球墨鑄鐵的應用范圍。如瑞士Georg Fischer(GF)Automotive AG公司研發的Sibo Dur系列球墨鑄鐵(表1、圖1),以Sibo Dur700-10和Sibo Dur800-5為代表的高強韌球墨鑄鐵材料在平衡懸架支架、差速器殼體、轉向節、車橋(軸)、控制臂、輪轂、曲軸和懸架系統等零件上的應用(圖2),實現了以鑄代鍛,以鑄代裝配,較好地滿足汽車輕量化要求。
對于獲取高強韌鑄鐵材質而言,各個生產企業采取的制備工藝路徑有所不同。有些企業通過微合金化和鑄造工藝優化,生產出的鑄態球墨鑄鐵性能即可達到技術要求。但該種方法對鑄造原材料及鑄造工藝控制要求嚴格。有些企業通過鑄后熱處理提高材料性能,一般采用正火或正火+回火處理。采用該方法的優點是對鑄造工藝及合金配比要求較松,缺點是由于增加了熱處理工序,并且鑄件變形,加工量增加,導致生產成本上升。
中國一汽高強韌鑄態球墨鑄鐵產品主要通過微合金化和鑄造工藝優化實現高性能。目前已成功開發出QT800-5、QT600-5等高強韌鑄態球墨鑄鐵牌號,并將上述材質代替QT450-10用于生產底盤支架類、殼體類汽車零件(圖3)。其中新開發的大支架(表2)通過采用高性能球墨鑄鐵QT800-5,并結合結構優化及制備工藝改進等措施,使之具備性能優良、降重效果明顯、成本低等優勢。
高強韌鑄態球墨鑄鐵的成功研發為汽車鑄件輕量化設計提供了更多產品優化、改進的空間,已成為未來汽車底盤類零件輕量化的首選材料。今后高強韌鑄態球墨鑄鐵材料可在轉向節、車橋(軸)、控制臂、輪轂、制動盤、發動機支架,曲軸和懸架系統等零部件上推廣應用,用于替代傳統鑄鐵、鑄鋼材質,實現材料升級及零件輕量化設計。高強韌鑄態球墨鑄鐵的性能已與部分鍛鋼材質相近,可通過替代部分鍛造零件,實現以鑄代鍛、以鑄代裝配,進而降低零件質量及數量,減少裝配流程,實現成本降低及輕量化的目標。
1.1.2 ADI材料的研發與應用
ADI是一種強韌性兼備的球墨鑄鐵材料(圖4),具有很高的彎曲疲勞強度和良好的耐磨性,可用于替代部分鍛造零件,實現節能降重。
東風汽車公司對某商用車車型進行了等溫淬火球墨鑄鐵替代鑄鋼件的輕量化驗證工作,并針對等溫淬火球墨鑄鐵件強韌性高的特點,對14個懸架類零件進行了重新設計。表3所示為采用等溫淬火球墨鑄鐵材料替代后的輕量化效果,總質量減輕近40%,降重效果顯著。
中國一汽從70年代開展了ADI材料在曲軸、主從動錐齒輪上的研發,但受材料質量控制、鑄造及熱處理技術不成熟、不完善,以及成本等因素困擾,材料性能無法達到GB/T24733《等溫淬火球墨鑄鐵件》要求,限制了ADI材料的應用發展。面對技術難題,通過大量試驗,對等溫淬火球墨鑄鐵進行材料開發與成分優化,找出合金配比與材料淬透性、力學性能的關系,并對組織中的石墨球化率、石墨球數進行控制,成功開發出高性能等溫淬火球墨鑄鐵材料。該材料性能明顯高于國家標準GB/T24733的性能要求(表4)。
在ADI應用推廣方面,中國一汽已成功開發出QTD900-8材質的一系列典型汽車零部件,并通過了臺架道路試驗驗證,代替了40Cr、42Cr Mo材料鍛造生產,在國內、外均屬首次應用,達到國際先進水平。其中某零件實現單車降重27.4Kg,降材料成本174.8元,實現質量成本雙下降。
據報道,上世紀70年代后期,美國通用汽車公司在完成大量實驗室和車隊實際跑車測試后,正式生產ADI后橋螺旋傘齒輪用于替代AISI滲碳淬火鋼齒輪,節省成本超過20%。相比鍛鋼齒輪而言,ADI齒輪具有密度更低,吸震性好等優點,應用前景廣闊。目前我廠也在拓展ADI材料在汽車齒輪、曲軸、發動機支架、懸架支架、差速器殼、拖鉤、橫向穩定桿、輪轂、懸掛彈簧座等零部件上的應用。
1.1.3 蠕墨鑄鐵材料的研發與應用
蠕墨鑄鐵力學性能、物理性能介于灰鑄鐵和球墨鑄鐵之間(表5),話于制造強度要求較高和需承受熱循環負荷的零件。對商用車而言,隨著功率和扭矩的不斷提高以及節能減排指標的日趨嚴格,大功率柴油發動機氣缸體、氣缸蓋材料已發展到HT250甚至是HT300水平,由于更高牌號的合金灰鑄鐵鑄造性能目前還有瓶頸需要突破,限制了發動機節能減排的進一步發展。面對這一困境,國內、外車企轉向開發具有更高力學性能的蠕墨鑄鐵制備缸體、缸蓋,并取得成功應用。據資料介紹,相對于HT250、HT300傳統缸體、缸蓋而言,采用蠕墨鑄鐵制造(圖5),結構剛度可提高12%~25% ,實現降重16%(圖6)。并且蠕墨鑄鐵缸體還具有改善摩擦磨損性能、降低振動和噪音等優勢。
如Audi汽車公司從1999年開始在3.3L的V8TDI發動機生產中使用蠕墨鑄鐵,并開發出2.7L和3LV6柴油發動機,用于A4、A6和A8型汽車。福特公司開發的V62.7Llion蠕墨鑄鐵柴油機具有155kW功率和440N·m轉矩。配有雙渦輪增壓的蠕墨鑄鐵發動機用于捷豹s型轎車以及路虎運動型多用途汽車。此外,大富、歐曼、戴姆勒-克萊斯勒、依維柯以及斯堪尼亞卡車公司全部通過采用蠕墨鑄鐵(表6)鑄造技術改進發動機性能。
蠕墨鑄鐵缸體、缸蓋雖比灰鑄鐵更具競爭力,但蠕墨鑄鐵缸體、缸蓋生產存在2方面技術難題:
a.蠕化處理過程中的工藝穩定性問題;
b.蠕墨鑄鐵的加工性能不如灰鑄鐵。國外蠕墨鑄鐵的成熟生產工藝有Sintercast工藝、Oxycast工藝、Novacast工藝、Backerud工藝。其中Sintercast工藝應用較廣,可有效保證蠕化處理的穩定性,獲得高蠕化率,但該工藝存在每包鐵液都要進行檢測,導致制造成本增加。
中國一汽在柴油機研發方面走在國內同行前列,目前研發的蠕墨鑄鐵發動機氣缸蓋即采用Sin?tercast工藝生產,材料為RuT450,蠕化率達到80%以上,正進行臺架試驗驗證工作。伴隨著蠕墨鑄鐵材料研發、制造及加工工藝的不斷改進,今后將繼續推動蠕墨鑄鐵缸體、缸蓋在更多機型上的應用,為汽車輕量化及節能減排提供改進空間。
1.1.4 鑄鋼材料的研發與應用
東風汽車精密鑄造公司采取微合金化并應用精密鑄造技術、熱處理技術提高材料性能,開發出系列高性能鑄鋼材料(表7)用于汽車鑄件薄壁化(最低4mm)及集成化設計(圖7、圖8)。經材質改進及結構優化,零件強度可提升30%以上,降重10%~30%。
受中國一汽制造資源及鑄鋼材質研發方面投入不足的影響,以往自主乘用車、商用車上鑄鋼件應用較為有限。近些年,通過對鑄鋼合金成分設計、材料強韌化機理的運用和熱處理工藝摸索,開發出系列高性能低合金鑄鋼材料,并在汽車零件上進行推廣應用。
1.2 輕質鑄造合金在汽車零件上的應用
汽車鋁合金零件中,鑄造鋁合金件(重力鑄造、低壓鑄造和其他特種鑄造零件)占74%~80%。對于鑄造鋁合金而言,除通過合金化提高性能的同時,目前還可通過控制成型工藝及后續熱處理提高材料力學性能。鑄造鎂合金和其它有色鑄造合金受成本及成型工藝等方面的限制,實際用量較小,但隨著工業水平提升、制造技術的發展及生產成本的降低,應用前景廣闊。
1.2.1 鑄造鋁合金的應用
鋁合金是汽車上應用最廣的有色合金,并且鋁合金材料的單車使用量在逐年提升(圖9)。目前汽車上應用的鑄鋁件正逐步替代灰鑄鐵、低牌號球墨鑄鐵件。
發動機為汽車心臟,其輕量化效果對提高汽車的動力性、經濟性和環保性具有重要意義。以往發動機缸體、缸蓋多采用鑄鐵生產,采用鑄造鋁合金(圖10)后可使質量大幅降低。如美國通用汽車公司的V8發動機氣缸體采用鑄鐵時的質量為94.4kg,采用鑄造鋁合金后僅為24.5kg,降重74%。氣缸蓋作為發動機第二大部件,長期處于高溫狀態下工作,承受較大的熱沖擊和應力集中。
采用鑄造鋁合金生產氣缸蓋除具有降重效果外,鑄造鋁合金還因具有良好的導熱性,可使熱量快速導出,提高發動機熱效率,避免缸蓋燃燒室產生過熱現象的優點。中國一汽在發動機研發方面一直走在國內最前沿,目前正在與清華大學合作開發過共晶硅鋁合金缸體。過共晶硅具有很好的耐磨性,可直接作為缸套與活塞摩擦,并將缸體一體壓鑄成型,達到進一步輕量化的要求。
鑄造鋁合金除在發動機缸體缸蓋應用外,還用于替代鑄鐵材質的發動機配件達到降重效果,如殼體、罩蓋、底座、支架等。經計算,QT450-10材質的發動機懸置支架更改為鑄鋁材質后,經結構優化,在材料成本不提高的情況下,可實現單件降重60%。
鑄鋁件還在傳動系統、行駛系統、轉向系統等方面具有廣泛應用。如中國一汽采用鑄造鋁合金替代鑄鐵實現輕量化方面,已將部分HT250材質的變速器殼體采用鑄造鋁合金生產(圖11),降重效果顯著,并已通過臺架試驗驗證,實現批量生產。
在某乘用車研發過程中,其前副車架、轉向節(圖12)零件通過選用A356材質,采用低壓鑄造成型替代以往鋼制零件實現輕量化。在控制臂輕量化方面,通過將控制臂設計成空心梯形結構,采用鑄造鋁合金生產達到降重目標。
1.2.2 鑄造鎂合金的應用
鎂合金壓鑄件在汽車上使用最早的實例是車輪輪輞。在汽車上試用或應用鎂合金的實例(圖13)還有油門剎車支架、儀表板支架、離合器殼體、制動踏板固定支架、座椅、轉向柱部件、轉向盤輪芯、變速器殼體、發動機懸置、氣缸蓋和氣缸蓋罩蓋等。在降重方面,與傳統鋼制轉向輪芯相比,鎂制件降重45%;與全鋁氣缸蓋相比,鎂制件降重30%;與傳統的鋼制沖壓焊接結構制動踏板支架相比,整體的鎂鑄件降重40%,同時剛性也得以改善。圖14所示為別克君悅(LaCrosse)6.9kg的壓鑄鎂儀表板梁,與傳統的鋼板設計比,減重40%,并且有效減少了零件數量。
雖然鎂合金壓鑄件具備比強度高的優點,但受成本、成型工藝技術及知識儲備限制,我廠鎂合金壓鑄件的應用較為有限,僅在方向盤骨架、儀表板等零件上有所應用。今后在深入開展鑄造鎂合金材料、成型技術研發的基礎上,逐步拓展鎂合金鑄件在座椅骨架、發動機鏈條室罩蓋、氣門罩蓋、變速器殼體、離合器踏板、制動踏板支架、車輪、輪轂、電子設備殼體等汽車零部件上的應用。
二 鑄件產品輕量化設計
2.1 薄壁化
在鑄件輕量化設計思想中,薄壁化是實現鑄件輕量化設計最有效、最直接的手段。鑄件薄壁化設計可預先通過CAE模擬、拓撲優化,在滿足零件使用性能前提下,對零件承受載荷不大或安全系數過高的部位進行壁厚減薄處理,實現降重降成本目標。經薄壁設計優化后的鑄鐵件壁厚一般可達到3~6mm,鑄鋁件壁厚可達到1mm。但受表面張力和粘滯力對合金液充型的影響,薄壁鑄件若采用普通砂型重力鑄造將難以成型或廢品率較高,一般采取熔模鑄造、真空吸鑄、差壓鑄造等特種鑄造工藝實現。
薄壁鑄件的鑄造工藝復雜主要體現以下幾點:
a.尺寸精度問題。由于壁厚較薄,鑄型材料及金屬材料的收縮和鑄件變形規律難以掌握,鑄件容易發生變形翹曲。
b.補縮問題。薄壁鑄件平均壁厚小,當局部壁厚突然增大時將難以補縮,在壁厚增大部位易形成縮孔縮松缺陷。
c.表面質量問題。薄壁鑄件對表面質量要求很高,若薄壁部位存在微小缺陷,將比傳統厚壁鑄件更易形成應力集中,對零件受力造成不利影響。針對上述問題,除要求選取適合的鑄造工藝并對零件鑄造工藝進行CAE模擬優化的基礎上,還要求在鑄件結構設計時重點關注零件壁厚的一致性,避免零件壁厚突然增大及薄壁大平面結構。中國一汽已開發出壁厚6mm的支架(圖15)。
經材料優化(將材料由QT450-10升級為QTD1050-6)及零件結構優化,鑄件質量由之前的4.1kg降為1.8kg,實現材料降重55%,降成本20%左右。目前項目組正推進壁厚2mm的支撐支架(圖16)及壁厚4~6mm的ADI殼體等鑄造零件的研發工作,為自主汽車鑄件輕量化提供技術支撐。
2.2 空心化
鑄件除通過薄壁設計實現輕量化外,還可通過空心化設計達到降重效果。在鑄件空心化設計方面,國外已有空心鑄鋁支架、鑄鐵空心曲軸及凸輪軸等應用實例。
圖17所示為空心鑄件、擠壓件焊接制成的支架,這個支架是工業界第一個由一個大的空心鑄件和若干擠壓件焊接組成的支架,達到減重10kg(約35%),比當前生產的鋼支架縮減了40個組件。其中空心鑄鋁件合并了32個沖壓鋼件,并減重9.5kg(約40%),降重效果明顯。
中國一汽正推進空心軸的研發及試驗驗證工作。經空心化設計(表8),可實現降重45%,材料成本降低28%,降重降成本效果顯著。
2.3 集成化
集成化設計是目前汽車零部件設計的一種趨勢,也是汽車鑄件輕量化發展的必經之路。該設計的主導思想為通過結構優化及可靠性計算,采用鑄造手段將多種成型工藝的零件集成一種零件,實現降低制造成本和輕量化的目標。集成化設計可使零件質量大大減輕,但對鑄造工藝提出了更高要求。
在集成化設計方面,國外車企通過對鋁合金薄壁鑄造工藝的研究,實現了鑄造鋁合金結構件的集成化設計并投入應用(表9),有效降低了車身質量,減少工藝過程,達到輕量化與集成化的目標。
東風汽車公司采用熔模鑄造方法對商用車底盤、懸架類零件(圖18)進行集成化設計,已取得較好的降重及經濟效果。據資料介紹,根據零件數量及集合難易程度的不同,經集成化設計,在成本不增加的前提下,零件安全系數可提升20%左右,降重20%~30%(表10)。
中國一汽也在鑄造零件的集成化方面進行深入研究,如某發動機上曾將鋁合金氣缸蓋罩蓋與凸輪軸罩蓋集成一個零件;某發動機143D支架將油泵體與支架集成一個零件(圖19),經過試驗驗證滿足使用要求。除此之外,還對懸架系統中的系列零件進行集成化設計,已實現裝車量產。目前正深入推進鑄鋁車架、車門、電池箱,鑄鐵橋殼等零部件的集成化設計與開發工作。
集成化設計不僅對鑄造工藝要求較嚴,也對設計水平及材料性能提出了更高要求,需要不斷創新,拓展集成化設計水平及應用效果。
三 鑄造技術進步
鑄造材料的不斷升級及輕量化設計對鑄件薄壁、空心、集成化的要求越來越高,也進一步推動了鑄造工藝的不斷改進及新型鑄造工藝在汽車零部件上的應用。從鑄件輕量化發展趨勢分析,熔模鑄造和(真空)高壓鑄造成型工藝具有顯著優勢。
3.1 熔模鑄造技術
汽車鑄件經拓撲優化后局部壁厚可降至1~6mm,采用普通砂型鑄造一方面難以成型,另一方面零件外觀質量也難以控制。采用熔模鑄造成型不僅具有尺寸精度高、表面質量好的優點,還可制備外形復雜的鑄件,是今后鑄造技術重點發展方向之一。目前,中國一汽將原方案普通砂型鑄造的壁厚4mm的進氣管采用熔膜鑄造工藝生產,壁厚僅為1mm(圖20),質量由1.4kg降低為0.4kg,成本降低15元。研發及應用的壁厚2mm的擋泥板支架(圖21),尺寸精度達到了CT4級,表面粗糙度達到了Ra0.4,替代了采用20#鋼的擋泥板支管與QT450-10支架的焊接結構,實現降重81%,降成本46%。在JL01輕型車鋼板彈簧支架開發過程中,選用高強韌鑄鐵QTD1050-6替代原QT450-10材質,經輕量化計算及拓撲優化,零件主體壁厚僅為4mm。對球墨鑄鐵材質而言,該零件若采用傳統砂型鑄造易出現冷隔、澆不足等鑄造缺陷,并且產品外觀質量難以保證,如果選用熔模鑄造生產則能滿足零件壁厚及外觀質量要求。
在熔模鑄造鋁合金車門內板(圖22)及車架的應用方面,緊跟國外輕量化研究進展,對整體鑄造鋁合金車門及車架的可行性進行分析。在整體鑄造鋁合金車門研發過程中,受車門尺寸較大,結構復雜,且車門上框部分壁薄中空及車門對尺寸精度要求高等不利因素的影響,鑄造工藝難度大。需對車門結構進行整體優化及工藝分析,降低鑄件壁厚不均勻性及鑄造缺陷的發生率,提高成品率,降低制造成本。
3.2 (真空)高壓鑄造技術
高壓鑄造是將液態或半液態金屬,在高壓作用下,高速填充壓鑄模型腔,并在壓力下快速凝固而獲得鑄件的一種方法。高壓和高速是高壓鑄造與其它鑄造工藝的根本區別,也是重要特征。高壓鑄造具有生產效率高、產品質量好、尺寸穩定性好,尺寸精度高的優點。并可通過結構優化減少零件數量,一個高壓鑄件可以整合數十個沖壓零部件,主要用于減振器支座(圖23)、門邊框架等零件制造。奔馳新SL大量應用鋁合金高圧鑄造技術,使零部件數量大大減少,其中A柱由兩個鑄件構成,替代原來的13個零件;前減振器支座整合了7個零件。
但高壓鑄造存在易產生氣孔,不能熱處理的不足,因此高壓鑄件的力學性能較金屬型重力鑄造件和低壓鑄造件低。而真空壓鑄工藝利用特殊設備將壓鑄型空腔內的空氣抽出,在真空條件下壓鑄成形。因此,能夠有效降低鑄件內部氣孔,并可進行熱處理強化,確保鑄件力學性能。同時,在真空條件下,可減少型腔內的反作用力,實現在很小的比壓下用小機器來壓鑄較大或者較薄的鑄件。
據介紹,奧迪A8(圖24)車身鑄鋁件占27%,并且該車的前縱梁后段、后縱梁前段、前減振器支座、后減振器支座等主要結構件也都采用真空壓鑄薄壁鑄鋁件,并通過集成化設計將車身零件由先前50個縮減至29個,實現車身框架完全閉合。該種結構不僅使車身的扭轉剛度提高了60%,還比同類車型的鋼制車身車重減輕50%,降重效果明顯。
四 結束語
鑄件材料替代、產品結構優化及鑄造技術進步既是汽車鑄件輕量化的3條主要技術路線又是一個協同創新的有機整體。在高性能及輕質鑄造合金合理應用的基礎上,對汽車鑄造產品結構實行優化設計,再輔以鑄造技術的進步作為實現輕量化設計思想的關鍵技術支撐。同時把汽車鑄件的輕量化設計統籌到汽車整體優化設計中,制造出成本效益更好、質量更輕、質量更佳的輕量化汽車鑄件。
附件下載:

-
地址:濟南市解放路134號 電話:0531-86401781 / 86952422 傳真:0531-86465075
郵箱:foundry-shandong@163.com 郵編:250013
版權所有 © 山東省鑄造協會 魯ICP備2021002429號
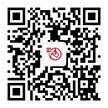
官方公眾號