會員登錄
MEMBER LOGIN
技術論壇
TECHNOLOGY FORUM
一種新型發動機汽缸體鑄造缺陷的解決方案
發布時間:
2013-10-31 00:00
來源:
公司新開發的一款高性能發動機,排量為7.14L,主要滿足中、重型卡車和大、中型客車以及其他動力機械,采用濕式缸套、直列、水冷、四沖程式結構,其中缸徑為108mm,最高爆發壓力可達17.5MPa,滿足國Ⅳ以上排放標準,目前已具備年產20萬臺的生產能力。其核心關鍵零部件氣缸體鑄件采用大批量、自動化、流水線生產方式,鑄件結構復雜,表面有大量的凸臺與加強筋,主要壁厚僅為6 mm,鑄件重224 kg。造型采用KW靜壓造型線臥澆工藝生產,砂芯全部采用冷芯盒制芯工藝,主體芯實現機器人整體浸涂:工藝。經過一年多的工藝優化和質量改進,鑄件內廢廢品率由15%降低到3%左右。
本文詳細介紹了該氣缸體工藝開發和驗證過程中出現的各種鑄造缺陷,初步探討了其形成機理,并提出相應的解決措施。
1 主要鑄件缺陷特征和分布
此新型發動機氣缸體最初生產時內廢廢品率高達15%,并且制芯生產效率低,每班次僅為100模,鑄件清理返工率高達50%;主要原因為鑄造過程中產生了大量鑄造缺陷,其中主要的鑄造缺陷有因鑄件表面結構復雜導致的粗清損傷與胃口帶肉缺陷、澆注系統設計不合理導致的沖砂缺陷、挺桿芯制芯工藝不合理導致的粘砂缺陷、上箱氣眼針多造成的散落砂缺陷和砂芯質量不合格造成的砂眼缺陷等。具體缺陷類別和缺陷比例如圖1所示,從圖1可以看出,機械手損傷、散落砂、粘砂、沖砂等缺陷為主要廢品特征,為此針對各個環節分別進行了分析和解決。
圖一 氣缸體主要缺陷及比例
Fig.Main defects and their proprotion in the
cylinder block
2 鑄造缺陷形成原因及解決措施
2.1 損傷缺陷
損傷缺陷對于在大批量、自動化、流水線鑄造生產條件下的氣缸體鑄件是最常見的缺陷之一。我公司氣缸體鑄件損傷缺陷主要包括兩種類型,一種為氣缸體鑄件表面的凸臺與加強筋在粗清時形成的損傷(規定此類損傷類型為粗清損傷),另一種為清理鑄件氣眼針時形成帶肉損傷(規定此類損傷類型為帶肉損傷);
2.1.1 粗清損傷缺陷
對于鑄件表面結構復雜,兄有大量的小凸臺和較高加強筋的鑄件,在用杉L械手進行鑄件粗清和轉運時,存在機械手損傷鑄件的隱患,極易造成粗清損傷缺陷。在前期生產一種新型氣缸體時,囚機械手造成的損傷缺陷比例高達3%以上:針對此缺陷經過多次工藝改進和工藝流程優化,損傷缺陷比例現已經降到0.5%左右。采取的措施如下。
(1) 針對易損傷的小凸臺,根據鑄件后續加丁裝配要求合理設置凸臺加強筋,增大凸臺的強度(圖2)。
圖二 易損傷凸臺及其加強筋
Fig.2 The damage-prone convex platrorm and corresponding reinforcing ribs
(2) 規范機械手操作規范,制定機械手粗清操作目視化看板,明確具體的粗清操作步驟及其機械手夾取鑄件位置。通過制定此規定,大大降低了人為損傷缺陷,因此,制定機械手粗清操作流程及鑄件夾取位置是采用機械手的鑄造車間必須要做的丁作,可以有效避免損傷缺陷的產生。
2.1.2 帶肉損傷缺陷
帶肉損傷缺陷是在清理鑄件澆冒口時帶走鑄件上的部分金屬造成的。設計的氣缸體右側面上共設計了16個小凸臺,以滿足發動機裝配很多外圍復雜部件的要求,鑄造工藝設計時,通常選擇此面為上平面,而在這些小凸臺上再設計出氣針,便于氣體/頃利排出,防止凸臺部位產生氣孔缺陷。但是出氣針的設置為后續的清理帶來了很多困難,既降低了清理效率又增加了帶肉損傷缺陷。在生產初期,由帶肉損傷造成的鑄件焊補占總數的80%。通過更改氣眼針形狀,很好地解決了此類問題。氣眼針底座由僅僅倒一圓角改為設計㈩一臺階結構,并適當減小氣眼針直徑尺寸,使氣眼針截面所占的凸臺面積降低到80%。氣眼針底座設計成臺階結構會使氣眼針與鑄件本體不直接相連,斷裂時從臺階處斷裂,該措施使出氣針帶肉損傷得到了有效解決。
2.2 沖砂缺陷
沖砂缺陷主要發生在鑄件的下表面兩個加強筋的結合部位,如圖3所示。沖砂缺陷對于缸體鑄件來說是非常嚴重的缺陷,因為沖走的砂子會隨鑄件凝固導致砂眼缺陷,嚴重影響鑄件的本體強度,若沖到水腔壁上便造成漏水缺陷(圖3c)。此類缺陷經過多次了藝改進,已得到明顯改善。主要改進措施如下。
(1) 從造型角度考慮,采用KW公司生產的氣流預緊實高壓多觸頭造型機,各造型參數相對來說比較穩定,針對沖砂缺陷,適當提高造型壓力與加砂量,最后通過硬度檢查來推算出砂型抵抗沖刷的硬度:
(2) 從砂處理角度考慮,生產該氣缸體時適當降低型砂含水量,提高型砂流動性 增加膨潤土的加入量,提高濕壓強度-經過大量的生廣:試驗,——般含水量要求控制在2.8%一3.0%,濕壓強度在170—180KPa、
(3) 從鑄件結構角度考慮,由于沖砂位置多為兩加強筋交匯處,增大加強筋與鑄件本體的過渡圓角, 防止尖角存在造成砂型強度低。事實證明,增大過渡圓角很好地減輕了沖砂缺陷。
(a)沖砂缺陷部位 (b)圖3a中I部沖砂局部放大區域 圖3a中I部背部沖砂區域
圖3沖砂缺陷部位及其局部放大圖
Fig. 3 Defect areas caused by sand-washing
(4) 從澆注系統角度考慮,原來澆注系統如圖4所示,只在第1、2、4、6、7瓦口上各開兩個內澆道。鑄件結構復雜且壁厚不均勻,因此澆注系統造成鐵液充型時出現紊流現象,并且內澆道開口位置正好對應下平面兩加強筋交匯處,而此交匯處也為砂型緊實度最低的部位,這就難免造成沖砂缺陷。另一方面,從圖4箭頭所指鐵液流向可以看出,第四瓦口處兩個直澆道都為其提供鐵液,澆注速度過快,沖刷下型最嚴重。從圖4中標注到的第四瓦口對應的下型位置,可以很明顯的看到嚴重的沖刷程度。
圖4改前澆注系統設置及其第四瓦口對應的下型位置
Fig.4Casting system before reform and drag corresponding to the fouth tile edging
因此更改澆注系統,在下型增加2個內澆道,在兩個直澆道上也就是對應的第三與第五瓦口處各增加一道內澆道。這樣很好地平衡了鐵液流動,減小紊流,最終減小鐵液的沖刷:經生產驗證,改進后的澆注系統改善效果明顯。新澆注系統如圖5所示。
圖5 改后澆注系統
Fig.5 Gating system afaer reform
2.3 散落砂與局部表面“粗糙”缺陷(橘皮現象)
關于鑄件表面散落砂的形成,前面已經介紹過,該氣缸體表面有大量小凸臺,為防止氣孔缺陷產生都 設計了出氣眼加強排氣,小氣眼設計為敞開式,分兩部分形成,模板本身氣眼針形成一部分,然后再利用造型線上的鉆了L機鉆透剩余部分,下一道廠序由人I:吹凈出氣眼內的殘留型砂:但鉆孔機有時存在隱患,即鉆頭坐標設定值與實際鉆孔位置不符,造成模板形 成的氣眼與鉆頭形成的氣眼連接不暢,搭接處易積聚大量散砂:實踐證明,此種情況即使經過人I:吹氣眼—I:序,仍殘留部分散砂,合箱后落入型腔,最終形成砂眼缺陷:經過長期跟蹤發現,當造型線斷電后,鉆頭坐標就會出現偏差,此時需根據實際進行調整鉆頭 坐標,保證尺寸的精確:通常直觀的判斷力·法就是查看澆注后鑄件形成的“氣眼針” [:下兩部分是否對齊連接,再隨時調整坐標:
關于鑄件局部表面“粗糙”缺陷,如圖6所示,在凸臺立面上出現粗糙的表面,粗糙情況與橘皮相類似,定義此類粗糙缺陷為橘皮現象,要注意的是人:廠吹氣眼時用的吹嘴長度、模板上氣眼針高度與鉆頭行程這二個尺寸的選擇,防止吹嘴中的高壓氣體破壞砂型表面,最后造成鑄件局部“粗糙”缺陷—該氣缸體前期生產時卜平面凸臺總/11現表面“機糙”現象,開始認為是—卜砂型硬度低, 且此處為凸臺的立面易造成局部“粗糙”現象。經過多次跟蹤,發現此問題的產生是由于吹嘴長度太長,并且與型腔距離太近,使得操作者在氣眼中稍微傾斜吹氣就會使高壓氣體破壞砂型形成“粗糙”缺陷。針對此現象,減小了鉆頭行程,使與型板形成的氣眼搭接長度盡可能小,并相應地減小吹嘴管長度,最終避免了局部“粗糙”缺陷。如圖7所示,當鉆頭行程與臍子氣眼針高度之間的搭接距離/4小于30mm,吹管深入砂型中的長度與臍子高度之間的距離B大于40mm時,對于防止高壓氣體破壞砂型有明顯效果。
圖6 鑄件“粗糙”缺陷
Fig.6 The “rough” defects castings
圖7 鉆氣眼針示意圖
Fig.7 Schematic illustration showing the blow hole needle
2.4挺桿粘砂缺陷
粘砂缺陷對于采用砂型鑄造:廠藝的鑄件是必然出 ;現的鑄造缺陷之一,粘砂缺陷直接影響清理效率,進而直接影響鑄件的交貨期。對于大批量、流水線和自動化的鑄造生產條件下,清理效率直接反應生產水平與技術水平。我公司新開發的一種發動機鑄件要求年 ;產20萬臺,因此清理效率必須高效,這樣就對影響清理效率的內腔提出很高的要求,而該氣缸體內腔挺桿芯挺桿孔部位直徑尺寸僅為20mm,開始生產時用石英砂制芯,由于澆注時該部位全部被鐵液包圍,易燒結粘砂,嚴重影響清理效率:針對此缺陷,更改了制芯丁:藝與浸涂廠藝:
(1)制芯由石英砂改為鉻礦砂和熟料砂雙組份-1二藝:鉻礦砂和熟料砂都具有較高的耐火度和良好的導熱性,發氣量低,尺寸穩定性好;
(2)浸涂廠藝由挺桿芯與主體芯一次整體浸涂改為挺桿;芯亢浸涂一次并烘干再進行組芯整體浸涂。第一次浸涂采用耐火度更好的專用涂料,然后再用一般涂料整體浸涂。挺桿芯采用兩遍涂料后粘砂缺陷得到了徹底解決:
雖然制芯千藝與浸涂下藝更改后成本有所提高,但是大大提高了清理效率,并降低了廢品率。因此在大批量生產條件下,通過提高內腔質量來提高清理效率是必然的選擇:實踐證明,特殊砂芯采取高性能芯砂與二次浸涂是一種簡單、有效的工藝:
2.5 內腔砂眼缺陷
經過實踐表明,砂芯質量直接影響鑄件質量,特別是采用整體組芯工藝,砂芯分模面處的砂芯披縫,清理不凈易形成鑄件內腔砂眼缺陷(圖8):若制芯過程形成過多的砂芯披縫,在大批量生產下難免出現披縫清理不到位的情況:閩此,砂芯披縫的清理,必須
引起足夠的重視,并采取有效的丁藝措施。通常現代化丁廠設計時,制芯中心一般采用機器人自動取芯,這就給制作專用的裝置自動去除毛刺提供了有利條件,可以根據砂芯形狀制作一隨形框架,并裝上膠皮,這樣就可以利用機器人轉移砂芯,達到自動去除毛刺的目的—也可以在取芯機械手上設計安裝去毛刺裝置,去除砂芯夾取位置處的披縫;比如氣缸體缸筒芯,為四開模結構,側模與下模處形成缸筒芯頭,此芯頭因側模與下模配合間隙易形成砂芯披縫。最早的思路是減小下模與側模配合間隙達到小于0.3mm來防止披縫的產生,為此制芯過程中必須要求及時清理干凈兩側模配合處的砂子,但是這一方法經過實踐證明很難實現。后來我們改變思路,在機器人取芯夾具與缸筒芯頭接觸位置處設計安裝一環形圈,在取芯時環形圈自動切除芯頭的披縫(1~19)。總之,整體組芯工藝在組芯前去除砂芯披縫,對減少砂芯披縫形成的內腔砂眼缺陷非常重要,而且,借助去毛刺裝置自動去除,效果更好。
圖8 鋼筒披縫圖 圖9機器人去毛刺技術
Fig.8 Casting fin of cylinder barrel Fig.2 The structure for deburring of robot
3 結束語
在全自動、大批量、流水化生產千藝條件下,對氣缸體出現的各種鑄造缺陷采取了有效的解決措施,尤其是損傷、沖砂和局部表面“粗糙”等缺陷改進效果明顯,為其他類似新產品鑄造千藝的開發提供了參考。
(濰柴集團供稿)
附件下載:

-
地址:濟南市解放路134號 電話:0531-86401781 / 86952422 傳真:0531-86465075
郵箱:foundry-shandong@163.com 郵編:250013
版權所有 © 山東省鑄造協會 魯ICP備2021002429號
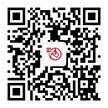
官方公眾號