會員登錄
MEMBER LOGIN
技術論壇
TECHNOLOGY FORUM
用鐵模覆砂工藝生產HT250制動鼓
發布時間:
2014-07-28 00:00
來源:
鐵模型覆砂鑄造,就是在金屬模型與粗成型金屬鑄型(常稱作:砂箱)內壁之間,覆上一層4~8㎜厚的覆膜砂,通常金屬模型的加熱溫度為240~250℃,外面的金屬砂箱的加熱溫度約為200℃,覆膜砂在這樣一個溫度場下固化,覆蓋在金屬砂箱內表面的覆膜砂成為硬殼的鑄型,鐵液注入覆有覆膜砂的金屬砂箱之中,凝固后成為鑄件的鑄造工藝方法。此工藝是基于金屬型鑄造和砂型鑄造相結合基礎上發展起來的,兼有二者的優點:鐵砂箱加快了鐵液的凝固冷卻,使鑄件石墨細小、結晶組織致密、基體中珠光體體積分數增加;鑄件尺寸精度高、加工余量小;鑄件表面光潔度好;造型材料需要量少;廢品率相對較低以及鑄件清理工作量小。由于鑄型強度高,幾乎不存在鑄型壁(向外)移動現象,所以石墨膨脹作用于鑄型的推力,幾乎不產生效應。因此使鑄件得到良好的自補縮,有利于減少或消除鑄件產生縮孔、縮松等缺陷。與砂型鑄造相比,采用鐵模(型)覆砂鑄造工藝生產出的鑄件,組織更致密、綜合物理性能得到改善,實現鑄件小冒口或無冒口鑄造。該工藝的缺點是:前期資金投入較多;適用于少品種、大批量鑄件的生產。
作者簡介:
楊群收( 1950—),長期從事灰鐵、球鐵等多種汽車配件;油田鉆井用高鉻雙金屬缸套及高鉻錘頭等耐磨材料的技術工作。現為中國鑄造學會質量控制及檢測技術委員會委員、河南鑄鍛協會專家組成員(住:河南、駐馬店13087096998、yqs6998@163.com)
制動鼓鐵模覆砂造型工藝示意圖:
1射砂孔 2下砂箱 3下砂箱覆砂層 4鑄件 5上砂箱覆砂層 6上砂箱
7澆注系統 8射砂孔 9澆冒口 10冒口覆砂層 11冒口坐套
一.鐵模覆砂工藝設計中及操作中的注意事項
(1)覆砂的厚度:覆砂的厚度對鑄件質量和生產成本都很重要。覆砂的厚度過厚,不但影響其激冷效果,也加大了生產成本,另外由于發氣量大,鑄件易出現氣孔缺陷,且不易均勻熱固化。覆砂的厚度過薄,激烈過重,鑄件的硬度高,不便精加工。一般情況下,精加工面覆砂較厚,非加工面覆砂較薄;珠光體基體材質的鑄件覆砂較薄,鐵素體基體的鑄件覆砂較厚;熱節點覆砂較薄(可少至3~4㎜),非熱節點覆砂較厚;距射砂口近處覆砂要厚,遠離射砂孔處覆砂適當薄;鑄件大而且形狀復雜時,覆砂要厚,否則影響砂的流速,途中固化,致使鑄型下部充砂不實。覆砂厚度一般控制在5~8㎜。
(2)如果鑄件的高(深)度大,在下部要設“氣塞”,防止起模時下部產生真空區不能進氣,吸傷鑄型。
(3)在加熱鐵模及砂型時,要控制其加熱溫度及整體溫度的均勻性。
(4)在設計分型面時,盡可能的使上下型(砂箱)高度均勻,減少充砂路程,便于使覆膜砂充實鑄型。
(5)射砂和排氣:即在往砂箱和鐵模型之間,形成的型腔中射充砂的同時,要使型腔中的氣體順利排出,否則將會產生覆砂不實或覆砂層不完整的現象。如:砂箱與鐵模底版的接觸面,砂箱上要開設排氣道,排氣道開設的大小,以只能充分排氣而不能跑砂為準則(一般是用手鋸開槽即可)。
(6)砂箱設計:砂箱壁厚激冷效果好,但鑄件易硬度高,砂箱壁薄急冷效果差。鐵模型及砂箱的壁厚一般在12~25㎜。鐵/砂=1:6~7(即鑄件重量與其所消耗覆膜砂重量之比)。
二.制動鼓化學成分及物理性能的要求:
制動鼓屬于HT250孕育鑄鐵,是汽車上的制動部件,質量要求嚴格。有的企業對其物理性能要求嚴格,對其化學成分含量要求不嚴;有的用戶不但對其物理性能要求嚴格,而且對其化學成分的含量要求也很嚴格。下表為兩個廠對HT250制動鼓化學成分、物理性能等的要求(表一、表二、表三為Z廠;表四、表五、表六為G廠):
化學成分要求:
表一
牌號 | 化學成分% | ||||
HT250 | C | Si | Mn | P | S |
3.0-3.6 | 1.3-2.0 | 0.5-1.1 | ≤0.06 | ≤0.12 | |
機械性能要求: |
|
單鑄試棒機械性能要求按表二
表二
牌號 | 抗拉強度(Mpa) | 硬度(HB) |
HT250 | ≥250 | 190-240 |
鑄件本體取樣,機械性能要求按表三
|
表三 | ||
牌號 | 抗拉強度(Mpa) | 硬度(HB) |
HT250 | ≥230 | 180-230 |
注:本體試樣在制動鼓柱面中部提取 |
金相組織按GB7216
基體:片狀珠光體,鐵素體或碳化物(若有)≤5%
石墨:A型細片狀石墨均勻分布占80%以上,B型、D型、E型等分布≤20%,石墨片狀長度不低于5級
化學成分要求按表四
表四
牌號 | 化學成分 | |||||
HT250 | C | Si | Mn | P | S | Cr |
3.4-3.6 | 1.3-1.8 | 0.6-0.9 | ≤0.08 | ≤0.12 | 0.2- |
機械性能:
單鑄試棒機械性能要求按表五
表五
牌號 | 抗拉強度(Mpa) | 硬度(HB) |
HT250 | ≥250 | 187/255 |
鑄件本體取樣,機械性能要求按表六
表六
牌號 | 抗拉強度(Mpa) | 硬度(HB) |
HT250 | ≥230 | 185/255 |
注:本體試樣在制動鼓柱面中部提取
金相組織按GB/T7216
基體:片狀珠光體,鐵素體或碳化物≤5%
石墨:A型石墨,石墨長度3-5級
三.化學成分的控制
1.碳(C)碳是鑄鐵的基本元素,碳在鑄鐵中的存在形式主要有兩種:一種是以游離狀結晶碳石墨的形式存在,另一種是以化合狀滲碳體的形式存在,也正是碳在鑄鐵中的這種存在形式,把鑄鐵分成許多類型。在灰鑄鐵中碳主要以片狀石墨形式存在。含碳量高,有利于促進石墨化,分析出的石墨量大,其金相組織往往為鐵素體基體和粗大的片狀石墨,材料強度和硬度較低;如果含碳量控制適當,又得到合理化孕育,其金相組織為珠光體和細小的片狀石墨,有較高的機械強度和硬度;如果含碳量低,又得不到合理化孕育,其金相組織為珠光體和細片狀石墨,甚至是白口組織,其強度高、硬度高、不便于機械加工。
對于生產HT250制動鼓來說,前者廠要求含碳(C)3.0~3.6%,比較好控制,通過孕育措施就可以到達其物理性能要求。后者廠要求含碳(C)3.4~3.6%,那就需要進行低合金化處理才能達到其物理性能要求。我們在實際生產中,前者廠碳控制在3.1~3.4%;后者廠碳控制在3.4~3.55%。
2.硅(Si)硅能減少碳在液態和固態鐵中的溶解度,促進石墨的析出,因此是促進石墨化的元素。如果以孕育的方法加入,其促進石墨化的效果更加強烈,其石墨化作用為碳的1/3 左右,故增加硅量會增加石墨的數量,但也會使石墨粗大;反之,減少硅量,會使石墨細小。一般碳、硅含量低可獲得較高的機械強度和硬度,但流動性稍差;反之,碳硅含量高,流動性好,機械強度和硬度較低。
灰鑄鐵中C、Si都是促進石墨化的元素。提高碳當量促使石墨片變粗、數量增多,強度和硬度下降。降低碳當量可以減少石墨數量、細化石墨、增加初析奧氏體枝晶數量,從而是提高灰鑄鐵力學性能常采取的措施。但是降低碳當量會導致鑄造性能降低、鑄件斷面敏感性增加,硬度上升加工困難等問題。控制含硅(Si)量如表七所示:
表七
前者(Z)廠 | 爐前含量 | 1.3—1.5 % |
終硅含量 | 1.6—1.8 % | |
后者(G)廠 | 爐前含量 | 0.8—1.0 % |
終硅含量 | 1.6—1.8 % |
3.錳(Mn) 錳是阻礙石墨化元素,故提高含錳量會增加基體組織中的珠光體數量。隨錳含量的增加,鑄鐵的強度、硬度增加,而塑性和韌性降低。控制在0.7-0.9 %。
4.硫(S) 硫在鑄鐵中通常被認為是有害元素。硫穩定滲碳體,阻止石墨化。硫化鐵的熔點低、且質軟而脆,能降低鑄鐵的強度,促進鑄鐵的收縮,并引起鑄鐵的過硬和裂紋形成。
用電爐熔煉鐵液的過程,與用沖天爐熔煉鐵液的過程是不相同的:沖天爐從開始融化到鐵液自爐中流出所經歷的時間很短,大約10min左右。即使沖天爐的出鐵水溫度不太高,但在爐內熔化過熱帶的溫度也在1700℃以上,而且鐵水的氧化并不嚴重,只會有利于粗大片狀石墨的分解,使其溶于鐵液,而且也不會減少自發晶核的量。這是因為細小的鐵液滴,滴落在妁熱的(白亮色)焦炭上,從焦炭上吸收了碳和硫,反而增加了自發晶核的量。另外,當爐中鐵液經過沖天爐的“過橋”流出后,要在前爐缸中停留一段時間,這段時間對鐵液的增核是有利的。用電爐熔化就不同了,從開始熔化到出鐵,需要約一個小時的時間,不存在著增碳、增硫的現象,而且鐵液過熱溫度高、過熱時間長、又有感應電流的攪拌摩擦作用,鐵液中微細的晶態石墨即自發晶核和外來結晶核心,都會逐漸溶于鐵液而消失;或浮經液面與集渣劑粘裹在一起被挑出爐外。這樣,使鐵液在共晶結晶時,可作為外來晶核的物質大幅度減少。例如,可作為外來晶核的SiO2,在溫度很高,又有攪拌作用的條件下,就易于與鑄鐵中的碳,發生如下反應而消失:
SiO2+C2→Si+2CO↑
這種缺少晶核的鐵液,在共晶結晶凝固過程中過冷傾向大,對孕育的回應能力很差,生產出的鑄件硬度高,不易精加工。
硫在灰鑄鐵中還具有低合金化的特殊作用。當含硫量小于0.06﹪時,硫的一些有益作用就無法得到發揮。在鑄鐵中存在有細小而分散的硫化夾雜物,能在石墨的生核和成長中起積極而有益的作用。用感應電爐熔煉廢鋼加增碳劑的合成鑄鐵,其最終含硫量一般不會超過0.03%的。我們為了提高鐵液的含硫量,爐前化驗后適量加入硫化亞鐵,含硫量控制在0.07-0.09%。
5.磷(P)磷在鑄鐵中通常也被認為是有害元素。P使鑄鐵的共晶點左移,其作用程度和硅相似,能溶于液態鑄鐵中,并降低碳在液態鑄鐵中的溶解度, 有略微促進石墨化作用,故計算碳當量時應計入磷的含量。當金屬材料中磷的含量達到一定量時,在鑄鐵中就易形成磷共晶,含磷量越高磷共晶數量越多。磷共晶的熔點低,在鑄鐵凝固過程中,較長時間的保持液態,不斷被共晶團排擠,最后被“驅逐”到共晶團邊界,在那里凝固,因此磷共晶呈多角狀(像做衣服剪下代尖的布頭)分布在共晶團邊界上,由于磷共晶尖銳角對金屬基體具有一定 的切割作用,所以降低了材質的強度,使鑄件易發生脆裂缺陷。
就制動鼓的生產來說,我們從使用的原材料源頭注意,就是不要進高磷生鐵、不要大量使用炮彈皮、柴油機缸套等高磷鑄鐵件作回爐料。含磷量應控制在≤0.07%。
6.鉻(Cr)鉻是反石墨化元素,共析轉變時穩定珠光體。在灰鑄鐵中含量有0.15%,即可明顯起到提高材質硬度和強度的作用。我們在對鉻的含量和控制方法上,作了大量的工作,在含碳量要求>3.4%的鑄鐵里,其含量稍低,鑄件的硬度和強度就低;其含量稍高出要求范圍,鑄件的硬度就高,精加工困難。我們在最后調料過程中采取措施,把鉻含量控制在0.3-0.45%范圍之內。
配料單(簡單)
元素名稱 | C | Si | Mn | S | P | Cr | |||||||
目標元素含量(%) | 3.4/3.5 | 1.65/1.8 | 0.7/0.85 | 0.07/0.1 | <0.06 | 0.3/0.45 | |||||||
配入元素含量(%) | 3.45 | 1.75 | 0.8 | 0.8 | 0.35 | ||||||||
材料名稱 | 新生鐵 | 廢鋼 | 回爐料 | 增碳劑 | 硅鐵 | 高碳錳鐵 | 高碳鉻鐵 | 硫化鐵 | |||||
配入了(%) | 20 | 60 | 20 | 2.25 | 1.4 | 0.4 | 0.5 | 0.16 | |||||
附件下載:

-
地址:濟南市解放路134號 電話:0531-86401781 / 86952422 傳真:0531-86465075
郵箱:foundry-shandong@163.com 郵編:250013
版權所有 © 山東省鑄造協會 魯ICP備2021002429號
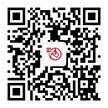
官方公眾號