會員登錄
MEMBER LOGIN
技術論壇
TECHNOLOGY FORUM
發動機曲軸感應淬火工藝
發布時間:
2014-11-19 00:00
來源:
感應淬火是發動機曲軸進行表面強化處理最有效的熱處理工藝,能提高其綜合的力學性能,同時它的經濟性、環保型、安全性等被機械行業所認知,是“十二五”規劃積極推廣的熱處理工藝。就國內而言,在主要的發動機主機廠、曲軸配件廠,感應淬火都已成為主要的曲軸強化手段,并在不斷擴大應用。曲軸采用感應淬火進行表面強化處理,技術和經濟指標非常理想。
曲軸感應淬火的優勢特點
(1)鋼曲軸經感應淬火+低溫回火(或自熱回火)后,與調質態相比可提高曲軸疲勞強度100%以上,同時大大提高軸頸表面的耐磨性(淬火+回火硬度可精確控制在50~55HRC),而其他強化手段則難以同時達到以上兩項指標。
(2)感應淬火生產效率高,而且感應淬火工序由于清潔及可按節拍生產,可以直接安排在曲軸生產流水線上,節省物流費用和時間。
(3)對曲軸而言,感應淬火是最節能的熱處理技術。曲軸僅對軸頸等需要淬火硬化的表面部位加熱,而且電效率高、時間短,較其他熱處理能耗降低80%以上。
(4)由于加熱范圍小、時間短,使處理的曲軸變形小、氧化脫碳少,可以減少精加工余量,降低機加工的工作量等。
感應淬火曲軸的材質
(1)曲軸材料
汽車曲軸常用材料有調質鋼42CrMo、35CrMo、40Cr、40MnB等,非調質鋼48MnV等,以及球墨鑄鐵等,這些材料都可以進行感應淬火。根據曲軸產品設計中有關數據,如曲軸載荷、發動機轉速、發動機服役條件等確定曲軸服役條件,選用材料時要根據服役條件與相應的材料淬火后能達到的技術指標等因素進行分析。材料中Cr、Mo等合金成分可以顯著提高材料的淬透性,從而提高曲軸的強度,但其價格較高,而且淬火開裂傾向大,需要使用合適的淬火劑以避免淬火裂紋,所以選材時應考慮滿足性能要求的前提下優先選擇球墨鑄鐵和非調質鋼,以降低生產成本。只要工裝合適、工藝合理、操作精確,無論是調質鋼還是球墨鑄鐵曲軸,都可實現感應淬火的技術要求。
(2)毛坯的預備熱處理
對鋼件講,調質鋼調質處理可以得到細致均勻的組織,零件內應力較小,對感應淬火極有好處:淬火組織均勻、淬火變形和開裂傾向小。非調質鋼利用V、Ti等元素的加入細化晶粒,在大幅度降低生產成本的同時提高各項力學性能,但其在組織準備上不同于調質鋼,所以在制定感應熱處理工藝時要根據其組織(珠光體—鐵素體型微合金非調質鋼為例)特點加以分析,才能充分的利用優點而避免其不足。
球墨鑄鐵曲軸的預處理組織主要有正火態和鑄態兩種。正火處理可以提高了珠光體的含量,消除鑄造應力,組織也較均勻,再經感應淬火容易得到組織、硬度均勻的淬硬層。鑄態球墨鑄鐵毛坯,鑄態組織中珠光體含量一般在75%~85%,鐵素體較多,要得到理想的淬火組織對感應淬火工藝要求較高。所以,制定工藝時要考慮不同的預處理對感應淬火的影響,才能將材料和熱處理工藝的性能發揮到最佳狀態。
感應淬火的熱處理規范
(1)感應淬火工藝要求的制定
感應淬火工藝,要取得理想的效果,與加熱功率、工件的材料、控制間隙、加熱時間、冷卻時間、工件余熱、淬火液的濃度、冷卻壓力等都有關系。對不同的材料應采用不同的參數,如合金鋼的韌性好,適合大功率加熱和快速冷卻,而球墨鑄鐵是脆性材料,不適合大功率、長時間加熱以及驟冷,加熱時間和冷卻時間應根據現場設備的實際狀況、工件淬硬層的要求而定。合金鋼和球墨鑄鐵曲軸中頻感應淬火的工藝參數見表1,僅供參考。
功率 | 加熱時 | 冷卻時 | 余熱 | PAG淬火 | 冷卻壓 | |
/kW | 間/s | 間/s | /℃ | 介質(%) | 力/MPa | |
42CrMo | 100±10 | 7~12 | 4~8 | 180~220 | 濃度5~10 | 0.45±0.05 |
QT800-3 | 80±10 | 7~9 | 3~5 | 180~220 | 濃度6~10 | 0.35±0.05 |
(2)感應淬火的技術要求
指標主要有:表面硬度、硬化區范圍、硬化層深度、金相組織、淬火變形量以及淬火裂紋等。
淬火硬化層金相組織:鋼曲軸為針狀或細針狀回火馬氏體,不應出現游離鐵素體;球墨鑄鐵曲軸允許在球狀石墨的附近有少量未溶鐵素體,但不能成環狀。
硬化層深度及表面硬度是獲得高疲勞強度的重要指標,都有一個最佳范圍,過高和過低都使疲勞強度降低。硬化層深度和表面硬度過低造成零件強度不足、耐磨性降低;反之當硬化層深度過高時,壓應力峰值從表面向內推移,表面壓應力降低,從而使強度降低,硬度過高帶來的危害是明顯的,它使零件的脆性增加,在曲軸受到彎扭疲勞載荷及沖擊力的情況下強度嚴重降低。常用鋼曲軸的淬火硬化層深度及表面硬度與疲勞強度的關系如圖1所示。
圖1 硬化層深度及表面硬度與疲勞強度的關系
圖中所示硬化層深最佳范圍適用于Φ55~Φ90mm軸頸,其他軸頸應在此基礎上做出調整,在以提高耐磨性為主時,表面硬度可以取高至55HRC左右;而球墨鑄鐵具有良好的自潤性及儲油能力,曲軸表面硬度≥45HRC即具有足夠的耐磨性;疲勞強度要求高時,應以得到高而均勻的表面壓應力為主,對表面硬度則不過分追求。
(3)淬火后的回火
感應淬火后,表面的組織由珠光體轉變成馬氏體,致使工件存在殘余的熱應力、組織應力,必須及時對工件進行回火處理,一般規定在4~8h內,否則會引起曲軸表面開裂,同時,感應淬火后的回火也是提高材料塑性和韌性、穩定工件尺寸的有效手段。
感應淬火處理的操作要領
(1)待處理件表面應無裂紋、缺陷、毛刺、油污、脫碳層等,否則,淬火后容易產生淬火裂紋、燒傷工件、硬度不夠等缺陷。
(2)設計制造或選用感應器時,其結構形狀和尺寸應能滿足工藝要求。
(3)感應器與工件在處理過程中,應保持合適的相對位置,控制間隙一般在1.5~2.5mm。
(4)正確選擇電參數,使設備處于最佳工作狀態。鋼軸選擇功率在(100±5)kW,球鐵曲軸選擇(75±5)kW。鋼軸可以較高的功率處理,因其有好的延展性,適合淬火;球鐵是脆性材料,適合較低功率淬火,否則特別容易產生淬火裂紋。
(5)工件表面溫度的測量很重要,應采用光電高溫計或紅外輻射溫度計,連續跟蹤測量控制工件下料溫度,保持在150~220℃的余熱,及時調整設備工作參數,利用余熱實現工件的自回火,這也是防止淬火裂紋的關鍵措施。
(6)根據材料、工件形狀、尺寸以及加熱方法和所要求的硬化層深度,合理確定冷卻參數,包括冷卻方法、冷卻介質(類型、溫度、濃度、壓力、流量)以及冷卻時間等。
(7)球鐵曲軸的圓角不適宜淬火強化,那么硬化層應離開圓角一定的距離3~6mm,使硬化區與非硬化區交界處的殘余拉應力遠離圓角,以提高疲勞強度,防止圓角處應力過度集中而引起早期非疲勞斷裂。
應用
球鐵曲軸的感應淬火加圓角滾壓,被越來越多的曲軸生產廠家所應用,該復合強化工藝的合理使用會使曲軸的疲勞強度提高100%以上,并且極大改善表面的光潔度和耐磨性,可操作性強。下面是某型號的QT800-3四缸曲軸進行中頻感應淬火處理的實例,其效果優于其他的表面熱處理。
(1)加工流程
鐵模鑄造→正火處理→高溫去回火→粗加工→一次探傷→感應淬火→中溫回火→二次探傷(檢測淬火裂紋)→精加工。
(2)感應淬火的工藝規范
根據曲軸感應淬火的技術要求,如圖2所示,制定感應淬火的工藝參數,如表2所示。
圖2 球鐵曲軸主軸頸淬火區域
表2 淬火工藝參數
(3)設備和工裝
設備是曲軸專用的半自動淬火設備,可控硅中頻電源,馬鞍形感應器,濃度5%~8%PAG淬火液。
(4)處理后的檢驗結果
曲軸淬火處理后各軸頸的淬硬層為3.0~4.0mm,淬火+回火后表面硬度45~52HRC,淬硬區域與側面的間距在5~6.5mm,淬硬區金相組織馬氏體6~7級,無淬火裂紋;淬火+回火后徑向圓跳動量≤0.5mm(測量中間主軸頸),滿足技術要求。
附件下載:

-
地址:濟南市解放路134號 電話:0531-86401781 / 86952422 傳真:0531-86465075
郵箱:foundry-shandong@163.com 郵編:250013
版權所有 © 山東省鑄造協會 魯ICP備2021002429號
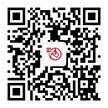
官方公眾號