會員登錄
MEMBER LOGIN
技術論壇
TECHNOLOGY FORUM
重力鑄造鋁合金車輪常見表面缺陷分析及其改進
發布時間:
2017-11-14 00:00
來源:
《壓鑄》
(曾禮 趙建華 林建黨 重慶大學)
前言:目前,國外鋁合金車輪的鑄造方法主要有金屬型重力鑄造和真空高壓鑄造。而國內,由于金屬型重力鑄造投資少、工藝成熟、生產準備周期短,因而在鋁合金車輪生產中普遍采用此工藝。金屬型重力鑄造是利用金屬液自身重量充型和補縮的一種鑄造工藝,在合金液澆注及充型過程中容易產生紊流,使合金液易卷氣和氧化,因此在鋁合金車輪鑄件中容易產生針孔、氣孔及夾雜等缺陷。重力鑄造通過冒口內金屬液自身壓力來對鑄件進行補縮,補縮效果較差,鑄件容易產生收縮缺陷。因此重力鑄造鋁合金車輪生產中,在合理設計補縮冒口的基礎上,結合使用模具冷卻通道、激冷塊以及激冷或保溫涂料,對消除或減輕車輪的收縮缺陷具有重要作用。
1 重力鑄造鋁合金車輪常見表面缺陷
在金屬型重力鑄造鋁合金車輪生產過程中,常見如下一些表面缺陷:
1)氣孔缺陷氣孔的孔壁表面比較光滑,單個或成群分布于鑄件皮下,有的也會顯露于鑄件表面。產生氣孔的原因主要有:鋁液含氣量高;合金液澆注時卷入氣體;鋁液與涂料反應生成的氣體;合金液中夾雜上附著的氣體等。
2)表面縮陷縮陷的特征是鑄件平滑表面上出現凹陷部分。其產生原因有:鑄件局部熱節大;內澆口位置不當,截面積太小;模具溫度太高或太低;補縮壓力太低等。
3)欠鑄欠鑄缺陷表現為鑄件充填不完整,輪廓不清,邊角殘缺。其主要原因有:合金液渣、氣含量高,流動性差;合金液澆注溫度和模具溫度過低;澆注速度過低;鑄件壁太薄;澆注系統設置不當;型腔排氣不良等。
4)冷隔冷隔缺陷特點為在液流對接處有接痕,其交接邊緣光滑,在外力下有繼續發展趨勢。冷隔形成原因如下:合金液流動性差;澆口設置不合理,流程太長;充型速度太低或排氣不良;合金液壓力頭太低等。
2 摩托車輪表面缺陷實際產生原因分析
在重力鑄造摩托車輪生產過程中,產生這些表面缺陷的原因有很多,影響因素也錯綜復雜,往往一個缺陷并不是由于某一個原因造成的,而是多個因素的綜合作用的結果。而且不同缺陷之間還可能相互作用和影響,如鋁合金中的氣孔、夾雜和縮松缺陷就是相互促進,互為因果的。因此在解決這些缺陷的過程中,必須要在眾多因素中找出其真正產生的原因,然后才能采取對應的合理工藝措施來消除或減輕缺陷。
圖1 為我公司一款鋁合金重力鑄造摩托車輪生產中常出現的表面缺陷,在車輪中轂上常產生氣孔和表面收縮缺陷,在輻條部位則常產生欠鑄缺陷。在生產過程中這些表面缺陷具有不確定性,有時因為這些缺陷造成的產品報廢率高達10%以上,造成鑄件質量很不穩定。為此公司組織人員對該產品鑄造工藝進行了仔細的研究,以求消除或減少這些表面缺陷。
(a)中轂氣孔(b)中轂收縮(c)輻條欠鑄
圖1 摩托車輪表面缺陷
通過大量的試驗和探索,根據影響缺陷產生的諸多因素,結合實際生產過程中的工藝參數,如澆注時間、模具溫度等,初步確定了現有鑄造工藝條件下產生這些缺陷的原因。
1)中轂氣孔產生原因分析
鋁合金液采用旋轉除氣機精煉除氣,要求鋁液含氣量≤0.20 ml/100gAl,通過檢測,鋁合金液含氣量為0.16ml/100gAl,到達了技術要求,并沒有超標,而且氣孔基本上都分布在中轂的最高處,有的在表面,有的在很淺的表皮下,經過拋丸或機械加工后就會顯露出來,而且分布也不均勻,因此判斷氣孔并不是由于鋁液中的氣體析出而產生的析出性氣孔,而是外界的氣體浸入鋁合金液中產生的浸入性氣孔。經過分析認為產生這種浸入性氣孔的主要原因是澆注速度過快和型腔排氣不良。在鋁液澆注速度過快產生紊流而且型腔排氣不暢時,型腔中的氣體很容易被卷入鋁液中,然后在充型過程中氣體容易被液流推移至鑄件上部最后充滿的地方。由于金屬型鑄造凝固速度快,卷入的氣體將難以浮出金屬液和排出型腔,從而在鑄件上部的表面或淺層皮下形成氣孔缺陷。
2)中轂表面收縮產生原因分析
通過摸索和試驗,在鋁合金車輪重力鑄造中,涂料厚度、合金液澆注溫度和模具溫度對表面收縮缺陷有較大影響,其中模具溫度的影響尤為突出。在模芯溫度過高或過低的情況下,都可能在車輪中轂表面產生收縮缺陷,造成表面凹凸不平。該車輪的中轂緩沖腔隔板比較薄,而中轂四周壁厚較厚,鋁合金液凝固過程中,緩沖腔隔板起著補縮通道的作用,中心冒口對中轂和部分輻條的補縮都要通過隔板進行。在模芯溫度過低時,鋁合金液澆注后中轂隔板凝固速度比較快,補縮通道過早封閉,使中心冒口的補縮作用大大減弱,從而容易在中轂表面,特別是中轂與輻條連接之處產生收縮缺陷。如果模芯溫度過高,雖然降低了隔板的凝固速度,但也會使中轂和輻條相接的熱節處凝固非常慢,當其落后于隔板的凝固時間時,中心冒口也會失去補縮作用,同樣會在中轂表面產生縮陷。實際生產表明,該類車輪的模芯溫度在450~480℃比較合適,能使中心冒口起到比較好的補縮作用。經過測量,生產中涂料厚度、鋁合金液澆注溫度都符合要求,但模芯溫度偏高,常在480℃以上,因此要在現有生產節拍條件下減輕表面收縮面,需要加強對模芯的冷卻,降低模芯溫度,加快中轂四周的凝固速度。
3)輻條欠鑄產生原因分析
金屬型重力鑄造中,由于模具傳熱快、透氣性能差,因此鑄件壁太薄、模具和鋁液澆注溫度低、澆注速度快、型腔排氣性能差等因素都容易引起鑄件欠鑄。從輻條上該缺陷表面上看其具有冷隔特征,但是該處零件壁并不薄,而且合金液澆注溫度和模具溫度都比較高(澆注溫度720℃左右,模具溫度450℃左右),因此引發輻條欠鑄最可能的原因是澆注速度快和型腔排氣不良。這兩個因素會使鑄件充型時合金液前沿型腔內壓力大大增加,合金液流容易將來不及排出的氣體封閉在零件局部,如零件的轉角或最高處,如果該處排氣不暢或不能排氣,就會在該處產生大的背壓,合金液不能充滿,造成零件欠鑄。該車輪輻條處是采用排氣線進行排氣,當頻繁出現輻條欠鑄缺陷后對排氣線進行檢查,發現排氣線被很多鋁屑堵塞,造成排氣系統的排氣性能大大降低。因此要解決該車輪的輻條欠鑄缺陷,除了適當降低澆注速度,更重要的是經常檢查和清理排氣線,保證排氣系統暢通。
3 鋁合金車輪表面缺陷的改進措施
根據上述的探索及原因分析,對該車輪出現的表面缺陷采取了合理的改進措施,以避免或減少這些缺陷的產生。
1)中轂氣孔的改進措施
車輪澆注時采用漏斗澆注,一般合金液在漏斗中的高度基本保持一致,因此合金液澆注速度主要取決于漏斗出口大小。為了降低充型速度,對漏斗進行了改進,減小了漏斗出口直徑,使漏斗出口直徑由原來的φ36改為φ28,如圖2 所示。同時為了加強渣、氣過濾和減輕液流紊流程度,漏斗下的錐形過濾網由原來的單層改為雙層。
圖2 澆注漏斗的改進
此外為了加強車輪中轂的排氣,對模芯的排氣系統進行了改進,增加模芯排氣槽數量,縮短排氣槽間距,從而增強了排氣效果,模芯排氣槽改進如圖3 所示。
圖3 模芯排氣系統的改進
2)中轂表面收縮的改進措施
為了加強中轂模芯的冷卻,在下模芯設有水冷通道。同時在下模芯上也設置了排氣塞,原水冷通道孔與排氣孔距離很近,壁厚僅3~5mm,使得這薄壁很快產生裂紋,為了不影響排氣,在水冷孔內又鑲嵌了鐵管,鐵管與模具之間的間隙影響了模具向冷卻介質的傳熱性能,降低了水冷管道的冷卻能力,導致模芯溫度偏高,模具溫度場不利于形成順序凝固,在中轂表面容易產生收縮缺陷。因此對下模芯的排氣孔和冷卻孔重新進行了布置,保證兩孔間的壁厚不低于10mm,取消了冷卻孔內的鋼管,增強了冷卻能力,使模芯溫度達到了合理的溫度。模芯的冷卻孔的改進前后如圖4。
a)改進前(b)改進后
圖4 上模芯的改進
3)輻條欠鑄的改進措施
車輪輻條處模具粘鋁產生的鋁屑堵塞了排氣線,嚴重影響了模具的排氣效果,如圖5。為了加強輻條部位型腔內的排氣,對輻條處模具排氣線重新進行線切割,清除堵塞排氣線的鋁屑,并對排氣系統定期進行檢查和清理,保證輻條處排氣暢通。
圖5 輻條排氣系統
通過實際生產驗證,以上的探索和改進是正確而有效的。改進后該車輪的氣孔、轂面收縮和輻條欠鑄缺陷大大減少,產品廢品率降到4%左右,并且質量比較穩定。
4 結語
通過對鋁合金重力鑄造車輪的中轂氣孔、中轂收縮和輻條欠鑄缺陷產生原因的探索和分析,找出了引發缺陷的原因:澆注速度過快和模芯排氣不暢造成中轂氣孔;模芯溫度過高引發中轂表面收縮;輻條排氣線堵塞,排氣不暢導致輻條欠鑄。根據這些原因對工藝、模具采取了相應的改進措施,減少了此類表面缺陷的產生,提高了鑄件合格率。
(來源《壓鑄》)
附件下載:

-
地址:濟南市解放路134號 電話:0531-86401781 / 86952422 傳真:0531-86465075
郵箱:foundry-shandong@163.com 郵編:250013
版權所有 © 山東省鑄造協會 魯ICP備2021002429號
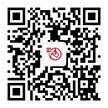
官方公眾號