會員登錄
MEMBER LOGIN
技術論壇
TECHNOLOGY FORUM
樹脂砂球鐵件表層球化不良的防止
發布時間:
2017-11-14 00:00
來源:
鑄造設備與工藝
吳祚勝 孟兆亞 代春福
(合肥鑄鍛廠 安徽 合肥 230001)
1、生產現象
通過金相,發現鑄件表面球化不良,異常組織為片狀石墨層,厚度在3~5mm,而且在片狀石墨與球形石墨之間存在一極薄蠕蟲狀石墨過渡區,如圖1所示。通過資料,發現許多文獻對采用樹脂自硬砂工藝生產的球鐵件表面出現的片狀石墨缺陷進行了報道,說明這種缺陷是一種普遍現象。
2、原因分析
一般情況下,球鐵中出現片狀石墨的主要原因是鐵液凝固時球化元素不足(Mg),或存在干擾元素,如S等。 我廠采用的樹脂為XY86-A呋喃樹脂,其技術指標如表1所示,加入量為1.0%(占砂) ;固化劑為SQ-A和SQ-B,加入量為30~50%(占樹脂)。SQ-A和SQ-B均為磺酸固化劑,都含有S元素,其技術指標如表2所示。通過實驗發現再生砂中的S元素含量較高,一般為0.1%左右,而球化后的鐵液中S元素含量則較低,小于0.02%。高溫下,砂型和鐵液組成的固/液界面之間,存在S元素的濃度梯度,S元素由砂型向鐵液中傳遞,差值越大,擴散能力越強。
在高溫狀態下,S元素以SO2氣體形式或者S2-、SO32-離子形式通過涂料層,進入鐵液中,增加了表層鐵液中干擾元素的含量。S元素與鐵液中的Mg元素反應,生成MgO、MgSO3以及 MgS等Mg的氧化物和硫化物,降低鑄件表層的殘余Mg含量,使鑄件表層球化不良,出現片狀石墨組織。
3、 防止措施
由以上分析,可知鑄件表層球化不良的主要原因是,高溫下型砂中的S元素進入鐵液,降低了鑄件表層的殘余Mg含量。要防止球鐵鑄件表層出現異常組織,必須阻止型砂中的S在高溫下進入金屬液。可以從三個方面解決這個問題:一是降低型砂中S元素的含量,減少傳遞源;二是采取措施,阻止S元素由型砂向鐵液的傳遞,從傳遞過程上解決;第三則是增加鐵水中殘余Mg含量,抵消S 的影響。具體有以下幾種方法:
3.1減少傳遞源
(1)降低再生砂的灼燒減量
再生砂中的硫元素與再生砂的灼燒減量有一定的比例關系。當灼燒減量高時,再生砂中S元素含量也高,在磺酸固化劑加入量以及型號不變的情況下,型砂中的S元素含量也會升高。高溫下,S元素在砂型與鐵液界面處濃度梯度隨之增大,型砂中的S元素向鐵液中擴散的動力也會增大,進入鐵液中的S增多,滲入深度加深,表面球化不良加重。降低再生砂的灼燒減量不僅能降低型砂中的硫含量,還能降低型砂的發氣量,降低鑄件產生氣孔的幾率。
(2)采用低硫磺酸固化劑
型砂中的硫元素,主要來自于磺酸固化劑。有研究表明,型砂中的S元素很難通過一般機械再生的方法降下來,控制源頭是最好的方法。在再生能力一定的條件下,采用低S固化劑,能有效降低鑄型和再生砂中的硫含量,從而從根本上解決表面層球化不良現象。
(3)降低固化劑的加入量
固化劑的加入量直接影響著型砂的硬化速度。在滿足初始強度要求的條件下,應盡可能的降低固化劑的加入量,不僅能降低鑄型和再生砂中的硫含量,還能降低成本。降低固化劑的加入量,型砂硬化速度變慢,鑄型的終強度能得到一定程度的提高。但是固化劑加入量不能太低,否則較短的時間內很難將其混勻,使得型砂強度分布不均勻,表面穩定性也差。
(4)降低砂鐵比以及吃砂量
在相同的澆注溫度下,鑄型采用較低的砂鐵比以及吃砂量,型砂中的樹脂固化劑能得到較多的燒損,再生砂的灼燒減量以及S含量都會變低。采用較低的砂鐵比以及吃砂量,不僅能降低S元素在鑄型與金屬液界面的傳遞動力,還能降低型砂、樹脂和固化劑的使用量以及再生系統的工作量。
(5)使用不含硫元素的固化劑
磷酸等為無機固化劑,不含S元素,能從根本上解決鑄件表層球化不良問題。磷酸高溫下潰散性差,再生砂中的磷酸鹽易沉積,反復使用時,鑄件表面會出現磷共晶組織,樹脂砂強度也會下降,一般只用于一次性使用的自硬砂中。
(6)加入新砂
新砂中不含S元素,在再生砂中加入新砂,能降低型砂中S元素的含量,應避免使用100%的再生砂。但是新砂加入量不能太高,否則會增加樹脂固化劑的加入量,反而增加型砂中S元素的含量。
3.2 截斷傳遞途徑
(1)阻硫涂料
這里的阻硫是指在涂料中添加其他物質,如MgO。當硫元素以SO2、SO2-和SO32-的形式通過含有MgO的涂料層進入鐵液時,能被涂料層中的MgO所吸收。
SO2+MgO→ MgSO3
SO23- +Mg2+ → MgSO3
S2- +Mg2+ → MgS
(2)提高鑄件的冷卻速度
冷卻速度越慢, 鐵液保持液態的時間也就越長,對砂型熱作用時間長,使固化劑受熱分解量增加,同時增加了硫元素的擴散時間,球化衰退加劇。提高鑄件的冷卻速度,能有效的減少硫元素的擴散時間,降低球化衰退效果。在使用冷鐵提高冷卻速度的情況下,鐵液不與樹脂砂接觸, 而與冷鐵接觸, 凝固加速, 形成硬殼, 也在一定程度上避免了硫元素的滲入。
(3)降低澆注溫度
在保證不出現其他缺陷的情況下,盡可能降低澆注溫度。降低澆注溫度, 能減少硫元素與液態金屬的接觸時間,減少硫元素的擴散,消弱球化衰退效果。
3.3 抵消S 的影響
(1)增加鐵液殘余Mg含量
提高稀土鎂球化劑的加入量,增加鐵液殘余Mg含量,消耗擴散到鐵液表層的干擾元素S。這樣做并不能完全消除擴散到表層的S元素,所以增加鐵液殘余Mg含量。只能使表層片狀石墨區減薄,并不能完全消除。殘余Mg含量不能過高,否則鑄件會出現渣眼、 縮松、 氣孔等缺陷,嚴重時鑄件出現滲碳體組織,惡化鑄件機械性能。
3.4 采取的措施
通過以上分析,結合我廠的實際情況,我們采取了以下措施:
(1)增加灼燒減量和再生系統的檢測、檢修力度,將灼燒減量降至2%以下。此時再生砂中的S含量約在0.05%左右,在很大程度上降低了型砂與鐵液界面S元素的擴散動力。
(2)降低澆注溫度,將澆注溫度降至1350℃以下,減少S元素與液態金屬的接觸時間, 減少硫元素的擴散。
(3)提高殘余Mg含量,將殘余Mg由0.03~0.04%增加到0.04~0.06%。
采取這些措施以后,我們將片狀石墨層厚度控制在了1mm以下如圖2所示,滿足了客戶的使用要求。
4、結論
有機磺酸固化劑的使用,使樹脂砂再生砂中含有較高的S元素。采用樹脂砂工藝生產球 墨鑄鐵時,鑄件表層易因球化衰退而出現片狀石墨,通過降低灼燒減量、降低澆注溫度、提高殘余Mg含量等措施使這種缺陷得到很好的控制
(來源:鑄造設備與工藝)
附件下載:

-
地址:濟南市解放路134號 電話:0531-86401781 / 86952422 傳真:0531-86465075
郵箱:foundry-shandong@163.com 郵編:250013
版權所有 © 山東省鑄造協會 魯ICP備2021002429號
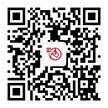
官方公眾號