會員登錄
MEMBER LOGIN
技術論壇
TECHNOLOGY FORUM
鋁合金消失模鑄造常見鑄造缺陷分析
發布時間:
2016-08-26 00:00
來源:
消失模鑄造屆
1 表面針渣孔(針孔)
鋁合金消失模鑄造采用干砂造型,泡沫模樣涂敷使用保溫涂料,由于氣化需要吸收大量熱量所以其出爐溫度和澆注溫度比普通砂型鑄造和壓力鑄造以及金屬型重力鑄造的溫度要高,加之鋁元素是活動金屬,所以造成鋁合金熔液氧化吸氣,鋁合金液在熔煉和澆注時與空氣中的水氣反應溶解氫氣和氧化。在其冷卻過程中鋁合金液容易析出氫氣形成分散性針孔和渣孔。另一方面主要原輔材料和熔煉設備及工具在生產過程中沒有充分嚴格按照生產工藝要求進行操作和技術控制;如熔煉設備和原輔材料以及熔煉工具在生產前沒有充分預熱;在選料熔化、精練、變質、出爐過程沒有嚴格控制鋁合金液吸氣和氧化以及在澆注過程中操作不當使空氣進入鑄型內產生嚴重的鑄造缺陷;所以在整個的生產過程中任何一個小的環節出現疏忽都會造成不良后果。如圖1~圖5常見的表面針孔、氣渣孔、針渣孔、渣孔、渣眼。
圖1 針孔 圖2 氣渣孔 圖3 針渣孔
圖4 渣孔 圖5 渣眼
這些缺陷的產生主要是在生產工藝制定上不科學和不合理;其防止辦法主要有以下幾點:①改變澆注系統;提高澆注速度;控制澆注時不能產生紊流。②提高涂料層和型砂的透氣性③控制泡沫模樣的密度、水份、發泡劑含量。④做到模樣干透;涂料涂層干透。⑤控制使用泡沫模樣粘結劑用量和質量,在保證粘接牢靠的前提下;用膠量越少越好同時必須選用低發氣量的膠料。
2 氣孔、夾渣孔、夾砂
氣孔在我們這里是指鑄件表面光滑的孔洞;它的形成主要是泡沫模樣發氣形成以及鋁合金液在凝固過程中。其氣體來不及排出鋁合金液造成。其主要原因是:泡沫模樣密度過大強度不均勻、涂料透氣性差、涂層沒有干透、出爐和澆注溫度偏低、澆冒口系統設計不合理。如圖6~圖9所示。
圖6 氣孔 圖7 渣氣孔
圖8 夾砂 圖9 夾渣孔
3 粘砂、結瘤
粘砂是金屬液滲入型砂中,形成金屬液與型砂的機械混和物,粘砂有兩種情況:一種是金屬液通過涂料層開裂處滲入型砂內,形成金屬液包住型砂;另外一種是金屬液透過涂料層滲入型砂內,形成的粘砂。鋁合金鑄件的粘砂一般都是填充砂不緊或沒有振實以及真空度過高所導致。鑄件粘砂情況如圖10~圖12所示。
圖10 粘砂 圖11 結瘤 圖12 表面粘砂
生產過程中控制表面粘砂的措施主要是控制好涂料的制備質量和涂敷質量;要求涂料涂層均勻、涂敷完整;特別是形狀復雜的內腔及拐角處的涂敷質量以及造型型砂粒度和造型時的緊實度。其次在操作過程中要有合理的澆注溫度、澆注速度以及負壓度。
4 縮孔縮松
鋁合金消失模鑄造其鑄件的澆冒口系統設計是相當關鍵的。其澆冒口開設與普通砂型鑄造不同;其冒口的補縮能力沒有普通砂型鑄造好;原因是消失模鑄造的冒口鋁合金液溫度偏低;冒口內壓力低。所以容易產生縮孔和縮松。如圖13~圖15所示。產生縮孔和縮松缺陷時要認真發現原因和產生的機理;一般采用改變澆冒口系統的設計,使系統合理科學以及提高補縮能力的方法來防止其缺陷發生。
圖16 潰型(塌砂)
圖13 縮孔 圖14 縮松 圖15 縮孔
5 潰型(塌砂)
消失模鑄造中型砂的移動、鑄型的破壞造成鋁合金液不能完全置換泡沫模樣使鑄件不能成型或鋁合金液充型速度過慢澆注溫度過低導致。如圖16所示,潰型(塌砂)缺陷防止辦法一般采用提高鑄型強度、合理的造型裝箱工藝、正確的澆注操作來保證。
6 冷隔與重皮
在消失模鑄造生產過程中鑄件表面產生冷隔其原因是鋁合金液澆注溫度偏低、澆注速度慢、澆注壓力頭低、澆注系統開設不合理造成。特別是鋁合金復雜薄壁件更容易產生冷隔;另在充型過程中負壓過大;鋁合金液沿型壁過快上升超過內部鋁合金液的上升速度;在鑄型表面形成一層殼;而后又被后面上升慢的鋁合金液填充;如果沒有被后面的鋁合金液熔化其殼就形成重皮缺陷。如圖17、圖18所示。我們解決這類缺陷的辦法是:①選擇符合鑄件結構和工藝要求的專用砂箱以及造型時泡沫模樣在專用砂箱中合理的擺放位置。②改進澆注系統,提高澆注溫度和澆注速度。③適當調整負壓,控制好氣化速度。
7 澆不足
在泡沫模樣的薄壁處或遠離澆口的位置由于鋁合金液與模樣置換過程中;鋁合金液前沿阻力大、鋁合金液流動距離遠,熱損耗大、降溫速度快;造成鋁合金液流動速度差,產生澆不足。如圖19和圖20所示。
圖17 冷隔 圖18 重皮
圖19 澆不足 圖20 澆不足
澆不足一般采用以下措施防止:①降低泡沫模樣的密度、改變原始珠粒種類、減少模樣的發氣量;②提高鋁合金液的澆注溫度和澆注速度③提高泡沫模樣涂料的透氣性和型砂的透氣性。
8 表面孔洞與凹坑缺陷
消失模鑄造在工藝操作不當和控制不嚴格的情況下,容易產生表面孔洞與凹坑的鑄件缺陷這些表面缺陷產生的原因比較復雜如渣孔、砂孔、縮孔等表面缺陷。此外如泡沫質量不良的情況下,鑄件表面還會產生龜紋等缺陷。如圖21~圖23所示。
消失模鑄造的這一類鑄造缺陷是比較復雜的產生過程,要認真仔細的具體分析,并且要根據自己單位的所有工藝操作過程和控制數據進行整體分析;一般采取以下幾方面措施同時進行:①嚴格控制組合模樣的工藝操作;提高澆冒口系統的擋渣能力和排渣能力;②提高鑄件的澆注溫度和澆冒口的補縮和擋渣和集渣能力以及澆冒口連接處的連接質量;③控制泡沫模樣質量和涂料的干燥質量。
圖21 孔洞 圖22 表面孔洞 圖23 凹坑
9 表面碳缺陷(皺皮)
表面碳缺陷(皺皮)是鑄件澆注時由于聚苯乙烯的分解產物形成所致。聚苯乙烯在700℃以下溫度形成粘稠的瀝青狀液體。粘稠的瀝青狀液體一部分被涂料層吸符;一部分在鋁合金液與涂料層之間形成簿膜;在還原氣氛下形成結晶碳。它在鑄件表面形成碳缺陷影響表面質量,見圖24~圖25。
圖24 龜紋 圖25 碳缺陷
碳缺陷的形成主要是泡模模樣的密度大或局部密度過大或涂料和型砂的透氣性以及澆冒口系統和澆注工藝控制不當等造成。要減少其缺陷產生必須嚴格控制預發泡和成型工藝;涂料質量的嚴格把關;設計合理的澆注系統和生產工藝;嚴格控制泡沫原材料的質量、提高鋁合金液熔煉質量以及澆注溫度和澆注速度。
10 珠粒狀表面和表面過燒
珠粒狀表面表現在鑄件表面呈泡沫珠粒狀,其根本原因是珠粒膨脹愈合不良。它會影響其鑄件機械性能以及密封性鑄件滲漏而導致鑄件報廢。另一方面影響其鑄件的外觀質量用戶不接受有此缺陷的產品。如圖26和圖27所示。其原因是①成型珠粒發泡劑含量不足;②成型時蒸汽壓力低;通蒸汽時間短;③成型模具質量有問題。表面過燒同珠粒狀表面性質基本相同不同的是一個不足一個是過火造成。表面過火現象是成型時模具的局部位置蒸汽量過大和珠粒充型不實。總體說主要是泡沫成型模具有問題,需要對模具進行必要的修理;才能解決其缺陷。
圖26 珠粒狀表面 圖27 表面泡沫過燒
11 表面凹凸現象
表面凹凸現象主要是因為泡沫成型模具上面的排氣塞凹凸和進料口料塞桿定位發生變化以及模具工作表面有破損或鑄造缺陷造成。防止這些小的缺陷產生平時要加強模具的定期檢查;成型操作工人要認真檢查觀察生產出來的泡沫模樣的外觀;即時發現即時處理。另外模具的制作要到專業的廠家去定作;才能保證模具質量;模具質量有保障泡沫模樣質量就有了質量保證。
結論
(1)國內鋁合金鑄件的消失模鑄造正是在起步初級階段,生產廠家少、產量低、設備性能要求高、工藝技術復雜、投資大。
(2)鋁合金吸氣、氧化是造成鑄件缺陷的最大原因。必須嚴格控制工藝過程從原輔材料的選擇、熔煉前的準備、熔煉操作技術的監督控制、除氣、精煉、變質、靜置、品質檢查、澆注等全部過程的綜合控制,才能有效防止。
(3)氣孔、渣孔、針孔、冷隔、澆不足、砂眼、表面氧化、皺皮、夾砂夾渣等等常見缺陷要認真分析綜合考慮并且結合生產單位的現有條件進行考慮解決。
(4)不同的鑄件結構特點有著不同的工藝要求;生產過程出現的缺陷也不相同,認真分析出現的問題;采取有效措施加以控制和預防。
(5)嚴格控制工藝過程;選擇合適合格的生產設備和檢測設備控制和保證其生產能正常進行。
附件下載:

-
地址:濟南市解放路134號 電話:0531-86401781 / 86952422 傳真:0531-86465075
郵箱:foundry-shandong@163.com 郵編:250013
版權所有 © 山東省鑄造協會 魯ICP備2021002429號
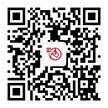
官方公眾號