會員登錄
MEMBER LOGIN
技術論壇
TECHNOLOGY FORUM
壓射速度對流變壓鑄AM60鎂合金缺陷形成的影響
發布時間:
2016-08-29 00:00
來源:
摘 要 采用自行研發的自孕育制漿技術制備AM60半固態漿料,利用冷室壓鑄機對漿料進行流變壓鑄成形試驗,研究壓射速度對鑄件缺陷形成的影響。結果表明,當壓射速度小于0.5m/s時,鑄件充型不足;增大至2.0m/s后,鑄件充型完整, 但充型末端易出現冷隔缺陷;壓射速度大于7.0m/s導致鑄件出現嚴重飛邊。顯微組織分析表明,壓射速度增大,鑄件內微氣孔增多且尺寸增大,鑄件邊緣液相偏析程度減小,同時內部夾雜增多,夾雜物尺寸較大;當壓射速度小于1.0m/s時, 初生相形貌發生粗化,液相中二次枝晶增多。因此,高壓射速度能在一定程度上提高流變壓鑄件顯微組織的均勻性,但同時使鑄件氣孔、夾雜缺陷增多,不利于提高半固態壓鑄件的力學性能
半固態成形(Semi—Solid Forming)是20世紀70年 代提出的一種新型金屬成形技術,其采用含有一半左右球狀固相的金屬漿料進行成形加工。由于半固態金 屬具有一定粘度,壓鑄時呈層流充型,有利于排出型腔氣體,能夠減小甚至消除氣孔缺陷,為熱處理強化創造條件。相比之下,液態壓鑄時金屬在壓力下呈高速紊流狀充填型腔,容易卷氣,造成氣孔缺陷,力學性能低且不 能進行熱處理強化。因此,半固態壓鑄是解決傳統壓鑄技術應用瓶頸的重要途徑之一。
近年來,由于工業生產對半固態成形性價比要求提高,學者將研究重點轉向短流程、高效率的半固態流變成形,先后開發了一些具有代表性的制漿技術,如 SSR、CRP、近液相線法、波浪形冷卻斜坡法、 傾斜式滾筒剪切法、蛇形管澆注法等。這為半固態流變成形工業化應用奠定了基礎。然而,除制漿之外, 半固態鑄件微觀組織和內部缺陷是決定其力學性能的主要因素。目前,針對半固態壓鑄工藝參數對鑄件顯微 組織的影響已有了一些研究,但仍然缺乏針對半固態壓鑄件缺陷形成規律方面的研究,這對于深入理解半固態成形、可控性精確成形的本質,以及提高半固態成形工藝可控性帶來了一定困難。因此,本課題 采用自行研發的自孕育制漿工藝制備 AM60半固態漿 料,利用冷室壓鑄機對漿料進行了流變壓鑄成形試驗, 研究了壓射速度對鑄件缺陷形成的影響,旨在優化半固 態壓鑄參數,為提高成形件質量提供參考.
1 試驗過程
試驗采用商用 AM60鎂合金,該合金理論液相線 和固相線溫度分別為615 ℃和580 ℃,其化學成分見表1。
取一定質量合金錠在坩堝電阻爐中熔化,升溫至720℃后用1.5%(質量分數)的C1C6精煉,扒渣后靜置。當熔體溫度降至690℃時,采用自孕育制漿工藝澆 注,具體過程見文獻。澆注時在導流器出口用溫度為595℃的保溫坩堝收集漿料并靜置3min,之后將漿料傾倒入壓鑄機壓室進行壓鑄。為了避免漿料在轉移和澆注過程中溫度波動導致固相率變化,制漿和漿料轉移澆注均使用同一坩堝。此外,對冷室壓鑄機壓室做特殊改造,在其側壁內沿軸向鉆孔,插入數根陶瓷加熱棒對壓室加熱,預熱溫度可達590℃,滿足 AM60鎂合金半固態成形的要求。試驗采用的壓射參數:增壓壓力為160MPa,模溫為250℃,保壓時間為30s,壓射時沖頭 速度選取0.2-0.9m/s。 壓鑄后,在壓鑄試樣1/2長度處切取寬度為5cm 的試樣,經過預磨、細磨、拋光后制成金相試樣,之后用 體積分數為10%的 HCl溶液腐蝕,利用 MEF-3光學顯微鏡對試樣中心和邊緣進行顯微組織觀察,重點觀察不同壓射速度下鑄件顯微組織中出現的缺陷種類及數量。
2 試驗結果與分析
2.1 壓射速度對鑄件成形性的影響
圖1為不同壓射速度下生產出的 AM60鎂合金壓鑄件。可以看出,當壓射速度為0.2m/s時,半固態漿料只能充填至型腔末端,所得試樣形狀不完整。試驗表明,在速度低于0.5m/s均會導致鑄件充型不足;當速度增大至2.0m/s時,壓鑄件料柄、橫澆道、試片及排氣槽部分輪廓清晰、形狀完整,表明增大壓射速度有利于提高漿料充型能力。但同時發現,速度在0.5-2.0m/ s時,鑄件末端表面處出現冷隔缺陷,見圖1b。當壓射速度增大至7.0m/s時,鑄件形狀完整,輪廓清晰,但此時沿分型面飛邊、毛刺嚴重(見圖1c)。由此可見,壓射速度越大,能在一定程度上提高漿料的充型能力,但同 時增大了產生鑄件飛邊缺陷的可能性。
試驗中在較低壓射速度下鑄件會產生澆不足、冷隔。這是因為壓射速度過低,漿料在壓室和澆注系統中 停留時間延長,固相率增大,導致粘度增大、流動性減小,使充型不連續或者充型后期中斷。此外,漿料充型時間越長,流動前端凝料現象加劇,先到模具型腔內部的金屬液不能及時與后面流入的金屬液完全熔合,就會出現明顯的冷隔。因此,對于半固態壓鑄而言,即使理論上凝固后期球狀漿料具有更好的流動性和補縮性,但如果壓射速度過低,同樣會導致無法完整充型。因此,為了提高漿料流動充型性,需要適當提高壓射速度。但速度過大,又會使漿料對分型面產生過大壓力,導致飛邊。這不但增加了后續飛邊切除工序,也增加成本,同時也容易導致鑄件表面應力集中,誘發裂紋。
2.2 壓射速度對氣孔的影響
圖2為不同壓射速度下流變壓鑄 AM60鎂合金顯微組織中的氣孔形貌。從圖2可見,壓射速度為0.5 m/s時,鑄件中未見明顯氣孔缺陷,隨著速度增大至2.0 m/s,可見光滑的微小氣孔分散在顯微組織中;當速度 增大至4.0m/s,氣孔清晰可見,數量增多,尺寸增大; 當速度增大至7.0m/s時,氣孔缺陷嚴重,數量增加、尺寸增大。由此可見,盡管半固態漿料具有一定粘度,有利于以層流方式充型以排出氣體,但如果壓射速度過大,同樣會造成大量氣孔影響鑄件性能。
半固態壓鑄時,壓室、澆注系統、型腔內部均存在氣體,壓射速度過高導致漿料受力增大,很容易導致紊流或射流,甚至飛濺現象。此時充型,氣體無法完全平穩排出型腔,被漿料裹入,而且由于漿料外部先行凝固,無法排出,最終留于鑄件表面之下。試驗發現,在鑄件末端和排氣槽附近觀察到的氣孔尤為嚴重。因此,利用半固態壓鑄減少氣孔缺陷需建立在優化壓射參數之上,如果氣孔嚴重,可通過降低壓射速度、增大漿料固相率來改善,同時也可以采取改進澆注系統設計以降低充型速度,增加溢流槽、排氣槽等措施。
2.3 壓射速度對液相偏析的影響
圖3為 AM60鎂合金流變壓鑄件在不同壓射速度 下試樣的邊緣組織形貌。可以看出,當壓射速度為0.5 m/s時,越靠近邊緣,固相顆粒越少,距邊緣約1000 μm范圍內幾乎均為液相,固相顆粒占比很少。隨著壓射速度增大至2.0m/s,邊緣液相偏析區明顯減小,固相顆粒增多,但邊緣液相率仍略高于中心。隨著速度增 大至4m/s,邊緣液相偏析仍存在,但固相率進一步增 大,從邊緣至中心固相分布趨于均勻。當壓射速度為7.0m/s時,邊緣液相偏析不明顯,整個視場內固相分布均勻。由此可見,增大壓射速度有利于減小鑄件邊緣液相偏析,從而提高組織均勻性。
半固態壓鑄時,由于存在一定含量的固相率,且液相將相鄰固相均勻隔離,固相之間相互作用較小,對流動充型影響較小。因此,在外力作用下,漿料中固相和 液相一般是分開流動,而且由于液相粘度低,流動速度較固相快。漿料充型時,邊緣部位金屬受型腔內部激冷,產生凝固收縮,體積收縮對液相產生近似于毛細吸引作用,使得漿料內部液相不斷流動至鑄件邊緣,造成液相偏析。隨著壓射速度增大,固、液兩相分離現象減小,液相高速帶動固相一起流動,因而使液相偏析減小。表面液相偏析區由于含有更多的硬質共晶相, 硬度會略大于心部位置,但從鑄件整體性能而言,液相 偏析造成的微觀不均勻很有可能誘導裂紋產生。因此, 在一定程度上增大壓射速度,對減小鑄件組織偏析、提高力學性能是有利的。
2.4 壓射速度對夾雜的影響
鎂合金半固態制漿時,如果熔煉不潔凈,熔體內易混入雜質。此外,鎂合金在高溫產生氧化燃燒,形成表面氧化皮、氧化渣等現象。當半固態漿料高速下注射到模具型腔時,很容易引起紊流將表面氧化夾雜裹入熔體,留于鑄件內部。圖4為不同壓射速度下 AM60合 金顯微組織中氧化夾雜形貌,其主要為形狀不規則,大小、顏色均不相同的夾雜物。從圖4可見,隨著壓射速度增大,顯微組織中夾雜物的數量和尺寸明顯增大,鑄件負載受力時,這些夾雜物會成為裂紋源,嚴重降低鑄件性能。試驗表明,如果壓射速度適當降低,有利于保證層流充填特性,漿料在通過內澆口等部位時,由于流動截面減小,流速增大,有利于表面氧化物滯留在澆口等部位,從而保證鑄件力學性能不會降低。
2.5 壓射速度對顯微組織的影響
圖5為不同壓射速度下 AM60鎂合金微觀組織形貌。從圖5a可見,當漿料在較低壓射速度下充型并凝固時,微觀結構組成為白色球狀 α -Mg晶粒和分布在黑色共晶組織中呈白色點狀的激冷 α -Mg顆粒。但在初 生 α -Mg晶粒之間,能夠觀察到尺寸較大的二次樹枝晶 組織。隨著壓射速度增大至1.0m/s,固相顆粒之間粘接現象減少,液相中樹枝晶分布均勻,尺寸相對減小(見 圖5b)。當速度增大至4.0m/s和7.0m/s時,半固態組織中白色 α -Mg晶粒形貌圓整,分布均勻,液相中二 次枝晶組織明顯減少(見圖5c、圖5d)。
半固態漿料壓鑄時,其凝固過程主要為漿料中剩余液相的凝固。因此,半固態壓鑄件微觀組織應為制漿時形成的較大尺寸固相顆粒與型腔內液相快速凝固形成的微小激冷組織。但是,壓射速度較低,漿料在壓室和澆注系統中與其接觸時間增加,液相提前部分凝固, 由于此時凝固速率不均勻,導致生成樹枝晶組織。 隨著壓射速度增大,剩余液相在充型過程中所受激冷作 用減小,且凝固速度增大,因此生成的二次枝晶組織減 小且數量較少。隨著壓射速度增大,漿料在很短的時間里迅速充填型腔,此時剩余液相幾乎全部在型腔內快速凝固,轉化為二次凝固 α -Mg(見圖5中白色細小顆粒)和共晶混合物(見圖5中黑色組織)。從凝固補縮角度來看,如果充型時產生過多的二次枝晶,凝固后期枝晶 間形成封閉空間,造成補縮困難,容易形成縮松、縮孔缺陷。試驗結果表明,增大壓射速度,半固態鑄件顯微組織相對均勻、細小。
綜上所述,半固態成形由于采用含有部分細小、球 狀固相顆粒的混合漿料進行成形加工,對細化鑄件微觀 組織、減少鑄件氣孔等缺陷具有積極意義。但是,從半 固態壓鑄來看,如果不能采用合適的壓射速度,不但會 使鑄件成形困難,而且會造成鑄件內部產生嚴重氣孔、 夾雜等缺陷,使半固態成形失去其應有的精確控形、控 性優勢。試驗表明,壓射速度越大,盡管能使鑄件微觀 組織更為均勻、細小,但同時會誘發嚴重的飛邊、氣孔、 夾雜等缺陷。這必將大大削弱其對鑄件組織改善的效 果,從而使半固態成形無法獲得其潛在的成形優勢。對 于含有一定固相率的半固態漿料,在熔體潔凈熔煉的基礎上,在確保鑄件良好成形性能的前提下,半固態壓鑄應采用盡可能小的壓射速度,這對于減小鑄件氣孔缺陷,保證其熱處理強化特性,進而獲得質量優良的半固態鑄件具有決定性作用。
3 結論
(1)半固態壓射速度對漿料成形性具有重要影響。 壓射速度過小,鑄件易出現充型不足、冷隔缺陷,壓射速度增大,鑄件成形性提高,但過大的壓射速度導致鑄件飛邊嚴重。
(2)半固態壓射速度減小,鑄件內微觀氣孔數量減少、尺寸減小,但顯微組織中邊緣液相偏析程度增大,初生相形貌粗化且二次枝晶增多;隨著壓射速度增加,鑄件微觀組織細小、均勻,但夾雜物數量增多、尺寸增大。
附件下載:

-
地址:濟南市解放路134號 電話:0531-86401781 / 86952422 傳真:0531-86465075
郵箱:foundry-shandong@163.com 郵編:250013
版權所有 © 山東省鑄造協會 魯ICP備2021002429號
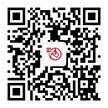
官方公眾號