會員登錄
MEMBER LOGIN
技術論壇
TECHNOLOGY FORUM
鎂合金鑄件在汽車工業中的應用與研究狀況
發布時間:
2016-08-17 00:00
來源:
鎂合金鑄件在汽車工業中的應用與研究狀況
第一壓鑄網
1 前言
研究表明,約75%的油耗與汽車整車質量有關, 減輕汽車整車質量可以有效降低油耗及排放。減 輕整車質量,還可以明顯減小動力傳動負荷,可在 較低的牽引負荷下達到更好的操控性能。在保 證汽年零部件強度和剛度要求下盡可能選用質量較輕的材料,是汽車輕量化的重要途徑之一。鎂合 金是當前常用金屬結構材料中最輕的,而且儲量豐 富,因而成為汽車減重以提高其燃油經濟性和可操 控性的首選材料。
2 鎂合金用于汽車工業的優勢
幾種常用材料的性能參數如表1所列 :
鎂合金部件應用于汽車工業中主要有如下優 勢:
a.質量輕,其密度只有鋁合金的2/3;
b.比強度高于鋁合金和鑄鐵,略低于比強度最 高的纖維增強塑料,有一定的承載能力;
c.比剛度與其他幾種材料基本相同,可以取代 鋁合金和鋼部件;
d.具有良好的鑄造性能和尺寸穩定性,易于加 工,廢品率低;
e.具有良好的阻尼系數,減振量大于鋁合金和 鑄鐵,用于制造殼體可以降低噪聲,用于制造座 椅、輪圈可以減小振動,從而提高汽車的安全性和 舒適性;
f.抗電磁干擾及屏蔽性好,減少噪聲;
g.對環境污染小,可重復利用。
3 國內外鎂合金汽車零部件的應用概況
3.1 國外應用概況
德國大眾汽車公司是最早在汽車上大規模應 用鎂合金的汽車公司,早在20世紀30年代,大眾 汽車就開始使用鎂合金,特別是90年代以來,德 國在鎂合金領域一直處于世界領先地位;奔馳汽 車公司最早將鎂合金壓力鑄造件應用于汽車座支 架,奧迪汽車公司第一個推出鎂合金壓力鑄造儀 表板。近年來,帕薩特、奧迪A4和奧迪A6等汽車 的齒輪箱殼體使用AZ91D鎂合金,與鋁合金部件 相比減重25%。
美國在1948~1962年間,采用壓力鑄造生產了 數百萬件鎂合金鑄件供汽車使用。美國的福 特、通用和克萊斯勒等汽車公司在過去的十幾年 里一直致力于鎂合金汽車鑄件如轉向柱架、離合 器殼體、進氣管、離合器片、汽缸蓋、座架、濾油器 殼體等的開發和應用,替代效果明顯,大大促進了 鎂合金的發展。
日本開發出鎂合金低壓力鑄造造裝置,由此, 經過研究相繼開發了一系列鎂合金壓力鑄造產 品,如豐田汽車公司首先制造出鎂合金汽車輪 轂、轉向軸系統、凸輪罩等零部件,目前,日本的各 家汽車公司都生產和應用了大量鎂合金殼體類壓 力鑄造件。
3.2 國內應用概況
在我國采用鑄造鎂合金已有30多年的歷史, 但最初主要用于航空航天工業的殼體、機輪和機 座等 [5,8] ,在汽車行業起步較晚,目前僅近百家企業 從事鎂合金壓力鑄造件的生產和研究。上汽、一 汽、東風汽車公司及長安汽車在研究和開發鎂合 金在汽車領域應用方面發揮了重要作用。
20世紀90年代初,上汽在國內最早將鎂合金 應用在汽車上,首次在桑塔納轎車上采用鎂合金變 速器殼蓋、殼體和離合器外殼。目前,其鎂合金 汽車變速器外殼生產和應用技術已經十分成熟,鎂 合金電機殼體鑄件正在電動汽車上進行裝車試驗。
一汽開發了高性能鎂合金 [5] ,可用于制造高溫 負載條件下的汽車動力系統部件,還成功開發出 腳踏板、氣缸罩蓋、增壓器殼體、轉向盤、傳動箱罩 蓋等鎂合金壓力鑄造件,并已應用于生產。
東風汽車公司結合我國汽車零部件壓力鑄造 生產企業設備現狀,開發了鎂合金冷室壓力鑄造 工藝生產汽車零部件的全套技術。
長安汽車在國家科技支撐計劃的支持下,完 成了以鎂合金變速器殼體、油底殼和氣缸蓋罩為 代表的大型復雜鎂合金壓力鑄造件的設計、分析、 模具開發制造和樣件生產,成功開發出國內第一 個鎂合金座椅并裝車通過法規試驗驗證,并聯合 重慶大學開發了擠壓力鑄造造鎂合金汽車輪轂。
3.3 典型零件
目前,鎂合金在汽車上應用的零部件有100多 種,可分為兩類:
a.殼體類,如離合器殼體、閥蓋、閥板、變速器 殼體、儀表板、曲軸箱、發動機前蓋、氣缸箱、儀表 板、過濾器殼體等,這類件不僅可以減輕整車質 量,而且由于鎂合金的阻尼衰減能力強,可以降低 汽車運行時的噪聲;
b.支架類,如轉向支架、轉向盤、燈托架、制動 器、離合器踏板托架、制動支架、座椅框架、車鏡支 架、分配支架和輪轂等,這類件有很好的抗沖擊韌 性,大大提高了汽車行駛過程中的平穩性和安全性。
隨著鎂合金汽車零部件的開發,鎂合金在汽 車上的應用有如下特點,由體積小的零件過渡到 體積大的零件;由結構簡單件過渡到復雜件;由簡 單受力件過渡到適應特殊性能要求的件;由分件 組合向過渡到集成化設計。
4 鑄造工藝方式
目前,在汽車中鎂型材、變形鎂合金的應用較 少(平均用鎂量不到 3 kg),主要應用的都是鑄件 (單車達到30~40 kg),壓力鑄造生產的鎂合金約 占車用鎂合金總量的80%。
4.1 壓力鑄造
從國內、外的研究應用情況看,鎂合金的鑄造成型方法較多,當前汽車零部件大多采用壓力鑄 造工藝進行生產。采用壓力鑄造工藝生產的鑄件 具有輪廓清晰、表面質量高、尺寸精確穩定、加工 余量小,組織細密、強度和硬度較高等特點。另 外,利用壓力鑄造工藝可以生產形狀復雜的薄壁 鑄件,生產效率高。
在鎂合金壓力鑄造中,鎂合金的比熱容小、填 充鑄模型腔速度快,彌散狀態的金屬流與模型腔 內的空氣高度混合,氣體來不及排出,最終在壓力 鑄造件內形成氣孔、澆不足、冷隔等缺陷。鎂合 金壓力鑄造件一般不能進行熱處理強化,為了消 除這些缺陷,提高壓力鑄造件的質量,近年來美 國、日本等相繼開發出了真空壓力鑄造、充氧壓力 鑄造、擠壓力鑄造造、半固態觸變注射成形和鑄鍛 雙控成形等新工藝。
4.2 真空壓力鑄造
鎂合金真空壓力鑄造是利用真空技術把模型 腔中的空氣抽空,同時輔助降低模型腔中的氣壓, 使得充填成型和合金熔液中的氣體排出,使合金熔 液在壓力作用下充填模型腔,并在壓力下凝固而獲 得致密件。真空壓力鑄造件不僅可消除表面氣 孔、疏松,提高表面質量,還能改善鑄件致密度、解 決涂料脫皮、電鍍起泡及盲孔缺料等工藝難題。近 年來,隨著鎂合金真空壓力鑄造工藝日益精良,鑄 件壁厚最低可達1.5mm,真空度≦80kPa,充填時間 大大減小,鑄件強度和韌性都得到相應提高。
4.3 充氧壓力鑄造
鎂合金的充氧壓力鑄造是充分利用熔化狀態 的鎂合金易與氧氣或其他活性氣體發生反應的特 點,在金屬液充填壓力鑄造模型腔前充入活性氣 體置換模穴內的空氣,當鎂熔液壓入模型腔時,活 性氣體與其反應生成金屬氧化物顆粒彌散分布在 鑄件中,從而消除鑄件內的氣體。充氧壓力鑄造 能夠減少甚至消除壓力鑄造件的氣孔,細化鑄件 組織,從而提高鑄件致密度和力學性能,并使其可 進行熱處理強化。日本輕金屬株式會社用充氧壓 力鑄造法成批生產了AM60鎂合金汽車輪轂,比鋁 輪轂質量減輕15%。
4.4 擠壓力鑄造
利用高壓使鎂熔液低速擠入模型腔內,凝固和 微小的塑性變形之后得到鑄件的方法就是擠壓力 鑄造。利用該工藝所得到的鑄件具有很高的致密 度、優良的力學性能及較高的尺寸精度等,對鑄件 的疏松、氣孔等缺陷有很好的改善作用。此外, 得到的鑄件還可以直接進行熱處理工藝,以獲取更 細小的組織晶粒。重慶大學蔣德平、龍思遠對鎂合 金輪轂做了一系列研究,采用擠壓力鑄造的鎂合金 輪轂具有良好的力學性能,工藝流程更短,生產效 率也更高。由于擠壓力鑄造的壓力可以改變鎂 合金的固溶度和熔點,科研人員開發了一些適合于 擠壓力鑄造的鎂合金體系,如英國的HTMI鎂合金, 在180 ℃下具有優異的強度和抗蠕變性能。
4.5 半固態觸變注射成形
鎂合金的觸變注射成形是一種充分利用注塑 成形原理讓金屬半固態觸變成形工藝。模具和成 形材料與壓力鑄造工藝相似,工藝過程則接近于 注塑成形工藝。該工藝不但可使鑄件組織致密、 凝固收縮小、成形溫度低和尺寸精度高,還具有操 作簡單、安全、效率高和環保等一系列優點,適 合形狀復雜、致密度高、薄壁和高性能零件的生 產。觸變注射成形技術是目前唯一用于鎂合金工 業生產的半固態成形技術,具有巨大的應用潛力。
4.6 鑄鍛雙控成形
鎂合金的鑄鍛雙控成形集合了液態壓力鑄造 和鍛造的優點,在成形過程中,可同時實現鑄件 形狀、尺寸和使用性能的精確控制。實質就是在壓 力鑄造基礎上,待模型腔中的液態金屬還未完全凝 固時,立即施加一個變形力,打碎已經凝固的枝晶 組織,進行細晶強化,使制件的力學性能得到顯著 提高,既解決了壓力鑄造件毛坯縮孔和疏松的缺 陷,又解決了鍛造不能生產復雜高精度零件的缺 點,主要用于生產形狀復雜和強度要求高的汽車零 部件。
5 存在問題與發展趨勢
雖然汽車工業用鎂量不斷增加,但是其在汽車上的應用還是相當有限。目前汽車工業中的主要 材料仍然是鋼鐵,其次是鋁。鎂合金在汽車工業中 并沒有獲得大規模應用有如下幾個方面的原因。
a.鎂合金的耐蝕性較差,存在高溫蠕變性,強 度不高等缺點,另外,鎂合金低溫工作能力及屈服 極限有限,高性能的鎂合金有待于研究開發。目 前鎂合金的基礎數據積累還不夠,沒有系統的力 學性能測試,在腐蝕、熱膨脹及模具設計等方面的 數據也不夠,使得汽車零部件的設計難度增大,成 本增加。
b.與鎂合金快速發展相適應的新型鑄造技術、 技術人員、設備配備不足。近年來,真空壓力鑄造 技術、充氧壓力鑄造技術、擠壓力鑄造等一系列新 型鑄造技術發展起來,使得鎂合金性能得到了很 大提高。如鎂合金的連續鑄軋技術具有很好的應 用前景,而目前國內的研究大多數還在實驗室內, 很少有工業化生產。另外,這些新型技術屬于汽 車生產商的機密技術,無法在汽車領域廣泛應用 推廣。鎂合金鑄造是一個系統工程,它集設計、制 造及研究為一身,需要鎂合金鑄造工作者具有更 全面的知識、經驗及研究開發能力。新的鑄造技 術要有新型的設備來與其匹配,以生產出性能更 好的鑄件,擴大鎂合金的應用范圍。但是新型設 備投資、運行的成本較高,可以對現有設備進行改 進,以降低其生產成本、減少生產周期,最終擴大 鎂合金在汽車行業的應用范圍。
北美鎂戰略聯盟計劃到2020年車用鎂平均質量 約達158 kg。我國按照目前車用鎂平均質量3 kg、年 增長20%計算,到2020年與北美仍有很大差距。 要想縮小這種差距,今后的主要發展方向為:
a.提高鎂合金的材料性能。鎂合金耐蝕性較 差,對于暴露在外特別是沿海地區的汽車底盤和 行走系統零部件,應能滿足使用環境對耐蝕性的 要求,高耐蝕鎂合金的研究成為鎂合金發展重要 方向;目前廣泛使用的商業鎂合金,如AZ91D,在 120 ℃以上溫度工作時因析出相的分解和軟化,使 其抗蠕變性能較差,對于工作溫度超過130 ℃的高 性能齒輪箱和曲軸箱,現有的鎂合金很難滿足使用要求。高耐熱鎂合金開發與應用是將來鎂合金 在汽車工業應用的重要領域;在汽車部件輕量化 的同時,其安全可靠性非常重要,重要的車內部件 如轉向盤、轉向盤立柱、座椅骨架和車門框等,除 了要滿足成型性要求,更重要的是材料要具有高 強韌性,能減振并使零件受重擊時不斷裂,應用較 多的如 AM60,AM50 其合金塑性較好,但強度偏 低,并且鑄造流動性和耐蝕性不理想,具有更高強 度和韌性,又具有優良鑄造流動性的鎂合金應該 大力發展。
b.新型鑄造技術、高技能人才及新型設備將成 為鎂合金鑄造發展三要素。
附件下載:

-
地址:濟南市解放路134號 電話:0531-86401781 / 86952422 傳真:0531-86465075
郵箱:foundry-shandong@163.com 郵編:250013
版權所有 © 山東省鑄造協會 魯ICP備2021002429號
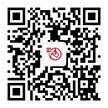
官方公眾號