會員登錄
MEMBER LOGIN
技術論壇
TECHNOLOGY FORUM
不同爐型熔煉灰鑄鐵 氫氮含量如何控制
發布時間:
2016-07-28 00:00
來源:
鑄造裝備
摘要:不管是氫還是氮的含量都要受熔煉工藝的影響,發現鐵液在澆包及保溫爐內的停留時間是影響氫含量的重要參量。氮的總含量(指化合氫和熔解的氮兩者之和)受溫度影響不太顯著。論文還指出;鐵液中的氫含量、保溫時間、和溫度高低三者之間的關系,說明氫含量的關系不是直接的關系。
序言
在生產高端鑄件,例如;灰鐵發動機缸體及缸蓋等高端產品生產時,經常會出現一定比例的產品缺陷,以及突發性引起的產品價格上漲事故。所以保證氣孔及氣縮孔缺陷發生率最低,盡快減少缺陷,并得到解決。
只要熔爐在正常參數下進行,熔池空間中的氣體,熔化了的液體及它周圍環境三者之間的關系與發生的,應是很容易理解的事情。液體金屬非常活躍,在它的表面生成化合物。不管生成氣體或是縮氣孔,其基本原理是三者平衡關系受到破壞,它們和周圍液體之間是處在一個平衡狀態下的。含量與熔液表面之間所產生的影響,在熔液和型腔內的氣氛,或者說,型砂與鐵液之間界面間形成的各種反應。借而得出,氣孔的形成核心與鐵液及凝固有著密切的關系。
鐵液中氫氣和氮氣的含量過高,就會在鑄件內形成針孔,當凝固的鑄件針孔析出的原因是由于凝固時氣體的溶解度下降所導致。熔液中的氣體含量是依熔液溫度及處理方法變化而改變的。這種變化也反應在鐵液充型過程,型腔界面產生的反應形成的氫氣和氮氣就從造型材料中釋放出來,也可以熔入鐵液中,這是很有趣味的。從爐料熔化到澆注,再到型腔充滿。在這個生產鏈條的各個階段中,平衡參數的變化就反應出氣體含量(包括氫和氮)的含量變化。
試驗的進行
本文介紹的內容分別來自兩個很不相同的工廠。他們制造灰鑄鐵的工藝路線差異很大。
鑄造1廠:用兩臺中頻感應電爐(每臺容量為11噸/爐)。熔化好的鐵液裝在1.8噸的鐵液包內。運到澆注區域,按計劃每包鐵液澆注4—5箱鑄型。
鑄造2廠:使用兩臺容量為3噸澆包和一臺生產率是每小時40噸的沖天爐。鐵液從爐內流出,進入保溫爐混合,自那以后鐵液不再是只可從單一熔煉方法(感應電爐或沖天爐)得到。但是要即使決定各自用量多少,預算過程有些困難和麻煩,只能在一天生產過程中予以變化調整。用1.6噸澆包將5噸鐵液分別倒入5個澆注保溫爐中去調整化學成分,然后,從這些澆注保溫爐經人工操作或自動澆注完成。
測試調整
首先我們必須明確這兩個鑄造廠在生產路線中,一些特定位置的氫氮含量。由于各種爐型的熔化工藝、爐型結構、熱工原理、使用的燃料等是不同的。通過對各種熔爐鐵液含氣量的對比測試,鑄造1廠直接在熔爐中測試,鑄造2廠基于安全原因,先從感應爐倒入澆包,添加新鐵液后再在包中測試。
為了準確的定出鐵液在翻包過程溫度損失造成的影響,鑄造2廠在爐前附近對新鐵液分別進行了氣體量的測定。
兩個鑄造廠都研究了溫度的影響,將澆包中的鐵液溫度從1500℃冷卻到1300℃時觀察其氣體含量的變化。以幾分鐘為一個時間段,進行自動記錄,兩個鑄造廠都做了相同的調查。
同時,兩個鑄造廠還在鑄型中測試了氫和氮的含量,鑄造1廠是在澆包內測的,而鑄造2廠由于澆包(鐵液處理包)太小,改為鐵液澆入鑄型后,在充滿型腔上升到冒口后進行,鑄型鐵液重390公斤,冒口直徑約30公分。
氫含量的測定
商業上有專門的測氫儀器測得含量。但是這種測氫系統不能測出全溶入鋼鐵熔液內的氫含量。只可在一個鐵模、耐住高溫的盆、或澆注包等熔器中進行測定。由信息處理機、分析儀以及氧槍,還有可更換的咀子組裝在一起。測量時,氮氣通過噴咀進行鐵液,與此同時,只要這些氣體吸收了氧氣,直到這氣體與鐵液之間調到了平衡。吸收氧氣的載體持借助于多孔陶瓷粒子再次抓獲,并進行分析研究。這些氣體作循環運動,直至得出測出結論,載體中的被測氣體氫的分壓不再變得為止。在分析儀中,通過測出的這種氣體的導熱能力去確定氫的濃度。
為了準確地測量氫含量,噴氮氣的咀必須向下傾斜15℃,插入鐵液的625px,插入鐵液約625px,測量時,熔液只許少量攪動。
氮含量的測定
用光譜儀測定鐵液中的氮含量。用一個盤狀鑄型澆注出試樣,鑄型用合脂砂造型。盤砂試樣壁厚4mm,直徑35mm,光譜儀測出總氮量,包括了溶解氮以及化合氮。
因為試樣要存放在盤中,于是試樣和樹脂砂粘接劑做的砂型發生接觸,其中它含的氮量要比鐵液的高。但是與砂子的接觸面積很小,在圓錐型腔上部和底部面積不一樣,接受氮的差別很小。
結果與討論
熔煉方法的影響
圖1 鑄造1廠的兩臺不相同的感應爐F1、F2及一臺沖天爐F2。鑄造2廠的F2,鐵液澆注溫度1400-1450℃,用氣球指示兩個廠的標準偏差
氫、在測定熔液中的氫含量時,所用的鐵液是從鑄造1廠和鑄造2廠提供,在圖1中看出明顯的差別,在感應爐生產的鐵液含氫量比在沖天爐鐵液的含氫量高。當溫度在1450℃沖天爐的鐵液氫含量約為1.5ppm,此時兩臺感應爐化的鐵液含氫總量是2—2.5ppm。這一結果與早些時后得到的數據十分一致。那時測得的為2ppm[123]左右。其原因是,兩者的爐型不同,爐料成分以及熔煉過程中的操作各方面也存在差別。沖天爐的豎爐從上往下,高溫區段的溫度梯度差別大。有利于加強對爐料的預熱,這種預熱可以使爐料的濕氣蒸發,減少鐵液中的氫氣含量。這兩種類型的爐子,鐵水的含氫量是不一樣的,大約差別20%。這兩種爐子重要差別是使用了含氫量低的爐料。爐料的化學成分盡管有些不完全一樣,但預熱效率指標好,優勢大。結論是沖天爐在祛濕方面是一個更為優秀的工藝設備。但是如果沖天爐這個優點不被充分利用,爐料中的濕氣得不到排除,則轉變為水蒸氣及濕氣。將以氫的形勢熔入鐵液,引起氫含量高。
氮
圖1是氮的總含量,也就是說(包括溶解氮和化合氮),研究指出,沖天爐熔化的鐵液比起感應電爐含氮量要高,這歸屬于不同的爐料成分,和爐料配料工藝。
例如;當空氣送風量過大,鐵液的含氮量增高。沖天爐熔化的鐵液氮含量高的另外原因是焦炭質量差。此外,爐料使用的廢鋼量高,含氮量也高。在爐料中廢鋼比例大約占50%。關于沖天爐鐵液含氮量高于感應電爐這件事,在過去文件中已經討論過。在沖天爐鐵液含氮量大約是 105ppm,而感應電爐是25ppm—95ppm之間。
在試驗中,兩種感應爐所化出的鐵液,氮含量出現的成分差別,可用爐料品種說明。在鑄造1廠用的是高氮含量,可看到爐料中廢鋼量是高的,用的廢鋼量達到40%。在鑄造2廠僅用了3%,鑄造1廠爐料中還附加了含氮的鐵合金,所以,鑄造1廠所得到的鐵液含氮量要比鑄造2廠高。
另外一個因素可能來自增碳劑,鑄造1廠所用的增碳劑,含氫、氮都比較低(含氫 0.005%、氮0.15%)。鑄造2廠附加碳灰做增碳劑另附加硅粉。用這些物質含有大量的氫和氮,但是測量表示氮含量在鑄造1廠是高的,這顯示出鑄造2廠用的碳灰對氮含量的影響是不明顯的。
另有報道,氮含量超過110PPM到150PPM就可能出現缺陷,這兩種鐵液含氮量在邊界線以下。但是爐料在沖天爐內的熔化速度比電爐快,例如;5噸熔量的電爐只有當爐料化清,而且還要一定的過熱后才能從爐內取出鐵液,澆注試樣。而沖天爐只需化部分爐料熔化即可取出試樣,就可有代表性。必須想到對于產生缺陷的危險與溶解氮和化合氮之間的比例數是很關鍵的;如果溶解氮的含量,靠 近了熔解度,這時熔液就成為飽和甚至過飽和狀態,多余的氫氮大量移出,造成在鑄件表皮容易形成氣體針孔的危險。
溫度的影響
圖2 鑄造2廠(a)和鑄造1廠(b)的熔液溫度與含量的關系,氫含量測量是從澆注溫度開始,冷卻到凝固溫度,對此溫度區間分成若干小溫度段,然后分段測量得出數據
一個很有趣味的觀察,當對氫含量進行測量時,發現熔液從澆注溫度冷卻到凝固時開始,向圖2(a)表示的那樣,在感應爐中氫的含量隨著溫度的降低,氫含量減少,而在沖天爐熔化的鐵液中,隨溫度降低而氫含量反而提高。這是鑄造2廠的實情。這兩種鐵液間用肉眼可以看到的差別,是原始含氫量,在測量開始的時候,因為溫度高,感應爐的鐵液含氫量要比沖天爐的鐵液含氫量高。
圖2(b)是鑄造1廠得到的各種測量數值,圖中也反應出含氫量的升高或降低。這種特性,是由于鐵液從爐內流出后,時間是一分一秒的增加,要早于溫度變化。
當盛有熔液的鐵水包吊起時,在熔液和周圍的空氣之間,氫原子不停的發生交換,這種平衡狀態與鐵液中氫的濃度有關。也與壓力和溫度有關,熔液在爐內的平衡狀態,與它在包內的平衡狀態是不一樣的,鐵液包在車間的跨度內吊起,它們的表面與空氣在室溫條件下是無有邊際的,根據這個原理出發,和氫氣發生強烈的擴散,不管是氫氣強烈的擴散進入到熔液,或者是從熔液進入到空氣,如果鐵液倒入澆包內時,產生兩種情況,氫的含量處在大約是2PPM,這就說明達到了平衡能度。這種平衡濃度不是立刻達到的,而是逐步的。因而氫在這種情況下,也是變化的,所以和溶解度的大小有關,與溶解的化學成分、溫度、壓力有關。因為平衡濃度和速度(進入原始晶格子的位置)同時與溫度有關。鐵液中的氫含量與溫度構成了一個關系。但是溫度不是必須的決定因素。
圖3 鑄造2廠(a)和鑄造1廠(b)中各種鐵液品種中的含氮量與溫度的關系,測量的溫度范圍為從澆注冷卻到凝固階段
總的氮量和溫度之間的關系,并不像圖3那么干凈明顯,在氮含量100ppm出現降低溫度,在80ppm時候,實際是保留一個常數位置,氧含量和溫度這種關系,Elmguist研究指出;氧量的變化與溫度沒有關系,被溶解氧強烈受溫度的影響,這意味著受溫度的變化而變化,溶解氧和化合氧之間的交換關系。
氧保持著故有的熔解,存在著溶解特性,氮也存在著象氧那樣溶解部分的氮量是有可能改變的。當保持一個常數時,這個可能就存在了因為測定溶解氮量沒有合適的好方法,只能在灰鑄鐵的溶液中測出總氮量,于是就不能定出和溫度是怎么樣的一個關系。
充型的影響
圖4 鐵液澆注鑄型之前的含氫量(a)和含氮量(b)。澆注開始前,鐵液內氫含量(a)和氮含量(b),鐵液在型內的氫含量和氮含量。澆注前氣體的測定,即可從中間澆包也可從敞包到出,而測定鑄型內的氣體含量則常在外冒口中進行
從圖4(a)得出,在進入鑄型后的鐵液中,氫含量要高于澆注前鐵液氫含量。這是因為鐵液在鑄型表面上流過,在使用潮模砂時,潮模砂含量高的氫的比例。而使用的泥芯是用人工合成樹脂砂制造的,當粘接劑燃燒時,也會放出一定的氫,大量的氫(含量)確來源于潮模砂的水分,附帶說;當沖型時速度快,接近紊流,以空氣的濕度進入鐵液。
在第一批得到的五組試樣鑄型中,情況很不相同,氫量大約從23%上升到117%,產生問題的原因,最可能是第一批鐵液首先流過鑄型表面,這部分鐵液,所吸收的氫含量自然會是最高的。在一個體積相對大的敞開的冒口中,測氫含量,如果外冒口是充滿的,那么氫在這種鐵液內變得稀釋。
氮
將鐵液的試樣拿到一個鑄型中,定氮系統的重量的確好。試樣盤不能完全充填,因為鐵的溫度太低,從圖4b可引導出氮含量出現微小變化。如果鐵液要澆入鑄型,含量要提升10%,允許用提高氫量的辦法,也可以加入潮砂,化學連接砂,以及紊流充型而引起,導致首先氮含量移到化學磨具過程在充型,因此這是nahe 氫含量比氮含量提升的快。
結論
從研究結果得知如下結論;熔化過程沒有出現來自氫的極端數值與控制混亂而造成的。重要的是氫、氮對于所發生的變動主要是熔化工藝。溫度、出鐵槽帶來的影響小。氫、氮含量還通過澆注這一工序而受影響的。鐵液中氣體含量在澆注進入鑄型之前,它們之間出現了差別,帶來了影響。
沖天爐熔化的鐵液比感應電爐含氮量高、含氫量低。爐料的預熱會降低,比感應電爐低(氫含量),但是它們的含量并不總是低于沖天爐鐵水的含量。不管是氫還是氮在充型過程中都提高,氫含量增加更強烈。
其它研究內容
建議研究其它的在充型過程中開展研究,但在這個過程是局限在金屬進入了鑄型之后才起作用。同樣的工作應該也包括象充型過程的紊流,縮氣孔在凝固過程氣體的形成和發生,部分工作也應當放在鑄型中吸收氣體的各種條件。為了獲得鑄鐵凝固過程的信息與組織。
附件下載:

-
地址:濟南市解放路134號 電話:0531-86401781 / 86952422 傳真:0531-86465075
郵箱:foundry-shandong@163.com 郵編:250013
版權所有 © 山東省鑄造協會 魯ICP備2021002429號
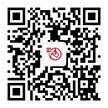
官方公眾號