會員登錄
MEMBER LOGIN
技術論壇
TECHNOLOGY FORUM
熔模鑄件常見缺陷及防止方法
發布時間:
2016-07-18 00:00
來源:
名稱 | 缺陷特征 | 產 生 原 因 | 防 止 方 法 |
氣孔 | 鑄件中出現明顯孔穴,孔內光滑 | 1型殼焙燒溫度低和保溫時間不足 | 1提高型殼焙燒溫度和延長保溫時間 |
2澆注系統設計不和理,型腔排氣不暢 | 2增設排氣孔或采用底注式澆道 | ||
3金屬液脫氧出氣不充分 | 3熔煉過程充分脫氧 | ||
皮下氣孔 | 鑄件經加工后出現的光滑孔洞 | 1爐料不干凈或使用過多的回爐料 | 1清潔爐料并減少回爐料用量 |
2熔煉過程中金屬液氧化吸氣,脫氧不充分 | 2嚴格控制熔煉工藝,加強脫氧 | ||
3型殼表面與金屬液發生反應 | 3選用合適的耐火材料 | ||
渣氣孔 | 夾雜物與氣孔并存 | 1爐料不干凈或回爐料過多 | 1清潔爐料并減少回爐料用量 |
2熔煉過程脫氧不充分 | 2嚴格控制熔煉工藝,加強脫氧 | ||
3鋼液含氣量多 | 3鎮靜鋼液 | ||
4型殼焙燒不足 | 4充分焙燒型殼 | ||
縮孔和縮陷 | 鑄件上由于補縮不良造成的孔洞,形狀不規則,孔壁粗糙 | 1鑄件結構不和理,有難以補縮的熱節 | 1改進鑄件結構,減少熱節 |
2澆冒口補縮作用欠佳 | 2合理設計澆冒口,使鑄件定向凝固,增大補縮壓頭 | ||
3澆注溫度過高 | 3降低澆注溫度 | ||
縮松 | 鑄件冷卻較慢處產生成片細小分散孔洞 | 1鑄件結構不和理,難以充分補縮 | 1改進鑄件結構,減少熱節 |
2澆冒口設計不和理,補縮作用欠佳 | 2合理設計澆冒口,使鑄件定向凝固,增大補縮壓頭 | ||
3澆注溫度過低 | 3適當提高澆注溫度和鑄型溫度 | ||
4鑄型的溫度低,鑄件冷卻速度過快 | |||
熱裂 | 裂紋沿晶界生長,表面有氧化顏色 | 1鑄型溫度低,冷卻速度過快 | 1提高鑄型溫度,減緩鑄件冷卻速度 |
2型殼退讓性差,阻礙收縮 | 2改善型殼退讓性和潰散性 | ||
3鑄件結構不和理,壁厚相差懸殊,過渡突變,應力過大 | 3改進鑄件結構減小壁厚差,平緩圓滑過渡 | ||
4澆注補縮系統設計不合理,造成鑄件局部 過熱或收縮受阻 | 4改進澆注系統設計 | ||
5選擇熱裂傾向小的合金和鋼種 | |||
冷裂 | 裂紋大多穿過晶粒,表面光亮 | 1鑄件結構不和理 | 1改進鑄件結構和澆注系統設計,減小收縮應力 |
2澆注系統設計不和理 | 2避免撞擊和拋甩鑄件 | ||
3鑄件在搬運和清砂過程中受撞擊 | 3矯正前退火,并改進矯正操作 | ||
4鑄件在矯正時操作不當或未退火 | 4減少型殼層數,并改善退讓性 | ||
5降低鑄件的冷卻速度,例如單殼可改用填砂澆注 | |||
金屬刺 | 鑄件表面出現密集或分散的小刺 | 1面層涂料粉液比低或粘度低 | 1提高面層涂料粉液比和粘度 |
2涂料與蠟模表面潤濕性差 | 2增加面層涂料潤濕劑加入量 | ||
3蠟模表面蠟屑未洗凈 | 3認真清洗蠟模和蝕刻 | ||
4面層撒砂料太粗 | 4減小面層撒砂料粒度 | ||
粘 | 鑄件表面有粘砂層,經噴砂后顯示有凸起的毛刺或凹坑 | 1面層用的耐火粉料和撒砂料雜質含量過高 | 1降低涂料中粉料和撒砂料中的雜質含量 |
砂 | 2制殼耐火材料或粘結劑選用不當 | 2選用適當的耐火材料和粘結劑 | |
3澆注溫度過高 | 3降低澆注溫度 | ||
4澆注系統設計不和理,造成型殼局部過熱 | 4改進澆注系統設計,減少局部過熱 | ||
表面麻坑 | 鑄件清理或拋丸后,局部出現密集的點狀凹坑 | 1澆注時金屬液和鑄型的溫度偏高,鑄件冷卻速度慢 | 1降低鑄型和金屬液的溫度,加快鑄件冷卻速度 |
2鑄件冷卻環境氣氛氧化性太強 | 2在鑄型的周圍人為的造成還原性氣氛 | ||
3水玻璃型殼中殘留的鈉鹽太多 | 3合理選用耐火材料和粘結劑 | ||
4充分焙燒型殼 | |||
5嚴格制殼工藝,保證硬化,風干充分 | |||
夾雜物 | 鑄件上存在與基體成分不同的物質,包括涂料層,砂粒,硅酸鹽,皂化物 | 1型殼面層涂料干燥,硬化不良 | 1面層涂料充分干燥.硬化 |
2涂料層結合不牢,在制殼和焙燒過程中面層涂料剝落 | 2降低第二層涂料的粘度 | ||
3型殼強度低,承受不了鋼液的沖擊而損壞 | 3提高型殼強度 | ||
4型殼脫蠟后放置時間短,水分多或焙燒時升溫快而損壞 | 4延長脫脂后型殼放置時間 | ||
5操作不慎,由澆口杯掉入砂粒或其他雜物 | 5脫蠟前仔細清理澆口杯邊緣;澆注前用吸塵器將型殼中的雜物吸出;采用二次焙燒法,即一次焙燒后,用熱水仔細清洗型殼內腔再進行二次焙燒 | ||
6模組焊接質量不良,涂料滲入接縫處形成飛翅 | 6改進操作,消除蠟模焊接處的縫隙,或采用浸封模料浸封 | ||
7模料中混入涂料粉,砂粒,皂化物等雜物 | 7認真過濾和處理回收模料 | ||
氧化夾雜 | 多見于大氣熔煉和澆注的耐熱合金,不銹鋼鑄件,其形狀呈細小片狀或網絡狀 | 1爐料不干凈,在熔煉過程中脫氧不充分 | 1清潔爐料,加強脫氧 |
2澆注系統擋渣作用差 | 2采用底注式澆道 | ||
3澆注溫度低,不利于氧化物浮出 | 3提高鑄型溫度和澆注溫度 | ||
4出鋼前用聚渣劑除渣 | |||
5采用真空熔鑄或過濾凈化 | |||
渣孔 | 鑄件的內部或表面夾有渣料,拋丸后鑄件表面形成孔洞 | 1渣料太稀,出鋼前未扒凈 | 1適當調整渣料增大粘度便于扒渣,并使用聚渣劑 |
2爐嘴上的雜物未清理干凈 | 2認真清理爐嘴上的浮砂或雜物 | ||
3澆注時擋渣不好 | 3澆注前適當鎮靜鋼液以利浮渣 | ||
4澆注系統擋渣作用差 | 4澆注時擋好渣 | ||
5改進澆道設計或采用過濾器 | |||
鼓脹 | 在鑄件較大平面上局部凸起 | 1制殼用耐火材料的雜質高,粘結劑的高溫性能差,使型殼在高溫金屬液的作用下產生變形 | 1使用雜質含量低的耐火材料,選用合適的粘結劑,提高型殼高溫強度。 |
2澆注溫度過高 | 2降低澆注溫度或采用填砂法澆注 | ||
3硅酸乙酯型殼面層硬化不透 | 3延長面層涂料氨干時間,增加氨氣濃度 | ||
4增設工藝孔 | |||
表面凹陷 | 鑄件表面局部凹陷 | 1蠟模表面縮陷 | 1用表面無縮陷的蠟模 |
2型殼分層,型殼面層向內鼓脹 | 2嚴格制殼工藝,避免涂料堆積,保證硬化,風干充分 | ||
3仔細清理浮砂 ,降低過渡層涂料粘度 | |||
鑄瘤 | 鑄件表面凸起的金屬小瘤 | 1涂料中的氣泡未被排除 | 1涂料鎮靜或真空除氣 |
2涂料時蠟模拐角或溝槽處有氣泡夾在涂料中 | 2涂料時用毛刷或氣嘴仔細排除夾在蠟模拐角處的氣泡 | ||
鼠尾 | 鑄件表面有不規則的淺溝條紋 | 1型殼面層熱膨脹系數大而背層小,在加熱過程中面層涂料開裂翹起 | 1合理選用型殼面層和背層的耐火材料 |
2涂料面層和背層結合不牢 | 2仔細清理浮砂,降低過渡層涂料的粘度 | ||
冷豆 | 在鑄件表面嵌有未完全熔合的金屬顆粒 | 1澆注系統設計不合理,澆注時金屬液產生飛濺 | 1合理設計澆注系統,使金屬液平穩進入型腔 |
2澆注時沖擊力過大,金屬液在型腔內產生飛濺 | 2澆注時,適當降低澆包與鑄型間的距離,避免產生飛濺 | ||
冷隔 | 鑄件上邊緣圓鈍的穿透或不穿透縫隙 | 1澆注溫度或鑄型溫度低 | 1提高澆注溫度和鑄型溫度 |
2內澆道截面積小 | 2合理設計內澆道 | ||
3澆注速度慢 | 3提高澆注速度 | ||
4澆注時斷流 | 4防止斷流 | ||
澆不到 | 鑄件殘缺或棱角不清晰 | 1澆注溫度或鑄型溫度低 | 1提高鑄型和澆注溫度 |
2澆注速度慢 | 2提高澆注速度 | ||
3鑄型排氣不暢 | 3增設排氣孔或改善型殼透氣性 | ||
4內澆道設計不當,金屬液流程過長 | 4改變內澆道的位置或增加數量 | ||
脫碳 | 鑄件表面層碳的含量低于基體 | 1澆注時金屬液和鑄型的溫度偏高,鑄件的冷卻速度慢 | 1適當降低鑄型和金屬液的溫度,加快鑄件的冷卻速度 |
2鑄件冷卻環境氣氛氧化性太強 | 2在鑄型的周圍,人為的造成還原性氣氛 | ||
變形 | 鑄件幾何形狀和尺寸不符合圖樣要求 | 1熔模變形 | 1采用優質模料,控制制模工作室溫度或采用矯正胎具 |
2型殼變形 | 2采用高溫變形小的制殼材料 | ||
3鑄件冷卻快,產生的內應力過大 | 3減慢鑄件的冷卻速度 | ||
4鑄件結構不和理,使其冷卻速度相差過于懸殊 | 4改進鑄件結構或增設防變形肋 | ||
5澆注補縮系統設計不當 | 5改進澆注補縮系統設計 | ||
6矯正鑄件 | |||
鑄件脆斷 | 鑄件脆性斷裂,斷口晶粒粗大,呈冰糖狀 | 1鋼液中脫氧劑鋁加入量過多 | 1嚴格控制脫氧劑鋁的加入量 |
2鋼中S , B等雜質含量過高 | 2采用潔凈爐料;提高爐襯質量 | ||
3鋼液嚴重過熱 | 3嚴格控制熔煉工藝,防止鋼液過熱和吸氫 | ||
4鋼液吸氫嚴重,造成氫脆 |
附件下載:

-
地址:濟南市解放路134號 電話:0531-86401781 / 86952422 傳真:0531-86465075
郵箱:foundry-shandong@163.com 郵編:250013
版權所有 © 山東省鑄造協會 魯ICP備2021002429號
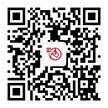
官方公眾號