會員登錄
MEMBER LOGIN
技術論壇
TECHNOLOGY FORUM
惠和杯論文│東風精鑄產品裂紋改善研究與實踐
發布時間:
2016-07-11 14:16
來源:
東風精密鑄造有限公司 十堰 442714
Research and Experiment on Improvement of Dongfeng investment casting Cracks
of Product
Liu jianguo Xu weidong He chunqiao Zheng wei Hu rentao
Dongfeng Investment Casting CO.,LTD Shiyan 442714
Abstract:This article starts with causes and types of cracks. Combined with casting improvement cases during the productive process, it discusses technical solutions and results of preventing and improving crack defects from such aspects as local structure adjustment,casting process optimization, post-procedure process improvement, etc., greatly reducing casting crack defects in the production process and also having some significance in improving the reliability and service life of precision castings.
Key words: Investment Casting,Crack Classification, Improvement Measures
1 前言
隨著汽車工業的進步,整車朝著安全、高速、低耗、低成本及良好的舒適性等方向發展,這將促進汽車零部件輕量化更深、更廣方向發展,近年來東風精鑄積極推進精鑄件輕量化的設計及推廣應用,從產品結構優化及多個零件集成后使鑄件變的更薄、更輕,同時也提高了零部件的功能集成。但隨之而來的是鑄件結構變的復雜,容易產生變形、裂紋等問題,這些成了生產過程中鑄造、校正等工序中遇到較多的難題。
2 裂紋的形成原因及分類
精鑄件裂紋的種類根據其產生的原因不同,大致可分為以下幾種:按裂紋產生的溫度范圍,裂紋可分為熱裂紋、冷裂紋;按照裂紋產生的位置,可分為內部裂紋和表面裂紋;按照裂紋尺寸大小,可分為宏觀裂紋和微觀裂紋;按照裂紋產生的次序,可分為初生裂紋、二次裂紋。根據實際生產過程中的分類統計,我們經常遇到的裂紋種類主要有以下幾種:熱裂紋、淬火裂紋和機械外力作用下產生的裂紋(如下圖1所示)。
鑄件由于表面及內部缺陷、尺寸及形狀偏差、鑄件化學成分以及溫度等原因,引起鑄造應力集中,當鑄造應力超過金屬的強度極限時,在鑄件表面或內部產生不規則的曲線狀的縫隙,從而形成裂紋,鑄件裂紋是一種不完全斷裂的金屬缺陷。裂紋的存在不僅破壞了鑄件的連續性,而且裂紋尖端大多尖銳,容易引起應力集中,促使鑄件在應力的作用下斷裂。
由于熔模鑄造生產周期長、生產過程各環節工藝相對較復雜,精鑄件裂紋形成的原因往往是多樣的,產品結構設計上的不合理、鑄造工藝設計不恰當、鑄件化學成分、精鑄型殼退讓性以及生產現場操作工藝不當等因素均有可能導致裂紋的產生。
3 改善裂紋的措施應用【1】
針對生產中探傷統計裂紋比例較高的鑄件,結合裂紋產生原因的不同,通過對鑄件結構優化、鑄造工藝、化學成分以及生產現場操作工藝等方面的調整與改善,來預防裂紋缺陷的產生,達到減少或消除裂紋缺陷的目的。
3.1鑄件結構局部優化,消除應力集中
在鑄件設計階段,除了根據產品自身的特殊特性和使用性能要求來設計鑄件結構外,還應充分考慮熔模鑄造工藝對鑄件結構的要求,對鑄件結構進行局部優化,使鑄件壁厚盡量保持均勻一致,對于鑄件結構限制必須存在的壁厚差異較大的,要盡可能保持厚薄結構平穩過渡,減小鑄件熱節和鑄造應力。必要的時候對鑄件結構進行局部特殊處理,如在鑄件的孔邊緣增加工藝翻邊或工藝補貼,拐角部位增加工藝筋等措施,避免產生較大的應力集中。
3.1.1厚薄壁相交處,結構平穩過渡
鑄件結構上的不均勻,導致各部位壁厚相差較大,薄壁處冷卻較快,強度增加較快,阻礙厚壁處收縮,結果在強度較低的厚處或厚薄相交處出現熱裂紋。
如下圖2所示為商用車板簧支架,鑄件鎖緊孔周邊加強連接筋交接部位裂紋改進案例。改進前老結構產品孔周邊壁厚較厚,與連接筋壁厚差異較大,如下圖2所示。經磁粉探傷統計,鑄件此交接部位裂紋比例高達20%以上。后期通過對產品加強筋結構微調優化,將筋設計成到孔周邊由遠及近截面逐漸變大的錐形結構,并將筋根部與大孔壁連接部位平穩過渡,消除臺階,如下圖2所示,改進后鑄件此部位裂紋消除。
3.1.2采用殼體結構,消除鑄件熱節
模組澆注后在自然冷卻條件下,型殼內各點的熔融狀態的鋼水凝固時間是不相等的,結構交叉連接較厚的局部區域冷卻速度較慢,最后凝固形成鑄件的熱節。這就會使鑄件凝固后在該區域產生熱應力集中,導致鑄件此部位裂紋的產生。因此對于鑄件結構設計,應盡量減小或避免產生鑄造熱節,以減少或消除鑄件局部熱量集中產生的鑄造應力。
如下圖3所示為實際生產過程中遇到的因裂紋報廢率較高的兩種鑄件的改進案例,就是典型的通過鑄件結構調整,由原來的筋板連接結構調整為殼體結構,消除原有熱節,減小鑄造應力,從而達到消除裂紋的目的。
3.1.3拐角優化設計,消除加強筋根部縮裂
對于存在加強筋結構的一類零件,加強筋根部與連接面處形成的拐角部位,通常是容易產生鑄造應力集中的位置,也是實際生產中遇到的產生裂紋最多的部位。因此,拐角部位的優化設計對于減少應力集中,消除裂紋有著非常重要的作用。
如下圖4所示,商用車橫梁支架類鑄件加強筋根部與平面相接的拐角部位為直角連接,拐角部位的裂紋缺陷廢品率在15%以上。通過將拐角優化為大圓角平滑過渡,鑄造應力大大減小,裂紋缺陷消除。
3.1.4增加工藝翻邊補貼、工藝筋避免應力集中
生產實踐證實,在不影響零件使用性能的情況下,通過對容易產生裂紋的孔周邊、筋板拐角部位增加工藝翻邊補貼、工藝筋等方法(如下圖5所示),同樣能夠有效地消除鑄造裂紋缺陷。
3.2鑄造工藝設計優化
除了產品結構影響外,精鑄件生產過程中鑄造工藝合理與否也是導致鑄造缺陷產生的重要原因之一。所以,為了有效地減少或消除鑄造缺陷及其不利的影響,解決鑄造工藝的問題同樣至關重要。在鑄件凝固階段后期,當鑄件線收縮受阻時就會產生鑄造應力,如果應力超過了鑄件凝固時的高溫強度,就會在此部位產生熱烈紋。因此,為防止鑄件產生裂紋缺陷,鑄造工藝設計時遵循順序凝固理論,從而盡量避免鑄件凝固收縮受阻。
3.2.1澆注系統優化設計
澆注系統對裂紋的影響不可忽視。一般澆冒口附近溫度較高,冷卻緩慢,容易產生裂紋。因此,設計合理的澆注系統,確定正確的澆注工藝,減少澆冒口對鑄件收縮的阻礙能夠防止鑄件產生熱裂缺陷。鑄件內澆道根部易出現過熱現象,在靠近內澆道邊緣處容易產生裂紋,因此內澆口設計時要考慮鑄件各部分溫度分布均勻和阻力最小的原則,實現鋼液充型平穩,有效地降低鋼液流速,轉移鑄件的過熱區,避免鑄件在內澆道附近產生裂紋缺陷。
對于薄壁鑄件采用扁寬形狀內澆口設計。澆口厚度一般為鑄件壁厚的一半,為了不降低澆注速度,避免局部過熱,同時保證模組的焊接強度,內澆口寬度一般比正常值大1~2倍。扁寬內澆口有利于分散金屬液的引入,避免因局部過熱而產生熱裂紋。圖6改進前的方案,該鑄件在內澆口附近出現熱裂紋。改進后將內澆口厚度減薄一半,寬度增寬一倍,熱裂基本消除。
澆注系統設計應盡量避免框形結構。對于存在兩個熱節的精鑄件一般情況下往往設計兩個內澆口,于是使得鑄件-內澆口-直澆道成為一個框形結構,這類結構最容易出現收縮受阻,很容易在內澆口附近產生熱裂,因此應盡量避免框形結構。圖7所示為板簧下托板鑄件澆注系統設計方案。圖7a為改進前方案,為了鑄件上下兩處熱節的補縮,分別設置了兩個內澆口。內澆口附近過熱而成為“弱點”,其收縮受鑄件本身以及中間部位型殼的阻礙,“弱點”部位存在熱裂。圖7b更改為一個加長腰圓形內澆口,鑄件翻轉180°焊接。滿足上下補縮的同時也緩解了原來的凝固收縮受阻,熱裂消除。
3.2.2鑄件材質改善
選擇熱裂敏感性小的合金,嚴格控制有害元素S含量。不同鑄造合金,對熱烈的敏感性也不同。凡是凝固過程中收縮系數較小,凝固時形成的固相的強度較高的合金,其熱裂敏感性較小。
硫是鋼中的有害元素。圖8所示為不同澆注溫度硫含量對鋼高溫強度的影響。鋼在凝固時,由于硫的存在,在晶界處出現FeS和Fe的低熔點共晶,而使鋼在高溫時的強度降低。因此含硫量高的鋼,其熱烈敏感性大。表1所示為含硫量與鑄件熱裂產生的關系,由表可知,含硫量高時鑄件中形成熱裂多。因此用稀土合金對鋼液進行純凈化處理,降低鋼中的含硫量是防止熔模鑄鋼件產生熱裂的有效措施之一。
烈的關系
另外,生產實際操作中,注意回爐料添加比例,一般鑄鋼件回爐料添加比例應小于30%,對于高裂紋、高機械性能產品需嚴格控制回爐料添加比例。
3.2.3低溫鋼水紅殼澆注
有些鋼種在結晶溫度附近的強度極限值很低,澆注溫度越高,凝固時結殼的強度越低。降低澆注溫度有利于防止熱裂紋的產生。但是降低澆注溫度,尤其是薄壁鑄件,很容易產生冷隔、澆不足等缺陷,因此在降低澆注溫度的同時必須相應的提高型殼溫度。型殼溫度提高到600℃以上還可以避開石英砂的相變膨脹,并有利于內層型殼的軟化,從而減緩型殼對鑄件的收縮阻礙。因此,低溫鋼水紅殼澆注是防止熱裂產生的有效措施。
3.3后工序操作工藝改善
由于鑄鋼件的鑄態組織較脆,遭受外力沖擊時容易造成脆斷。在鑄件清砂落件階段,不合適的操作過程都有可能使鑄件在機械外力作用下產生裂紋。因此,對于不同結構的鑄件采取合適的清理操作方式對預防鑄件產生裂紋也同樣至關重要。
對不同鑄件指定錘擊落件的部位,特殊鑄件在澆口棒上增加焊接錘擊方臺,薄壁件無法實現錘擊落件的采用氣割、切割落件,復雜薄壁件取消滾筒拋丸采用掛拋、改善機械校正等方式(如下圖9所示)均能有效地減少機械外力作用產生的裂紋。
在熔模鑄造生產取模、制殼、焙燒等過程中,盡量減少鑄件變形,同時并提高校正模等工裝輔具設計,開展熱校和多次整形校正研究,來降低因后續校正而產生裂紋。
4 結論
本文根據鑄件生產實際情況,結合裂紋產生原因的不同,通過對鑄件結構優化、鑄造工藝、化學成分以及生產現場操作工藝等方面的調整與改善(如表2所示),來預防裂紋缺陷的產生,達到減少或消除裂紋缺陷目的,不僅降低企業廢品損失,也提高了鑄件安全性、可靠性。可見,上述裂紋的改善措施在精鑄行業中具有一定的參考意義。
表2 產品結構、工藝優化設計及操作改善防裂紋對策及建議
參考文獻
[1] 許云祥等.熔模鑄鋼件熱烈的產生和防止[J],特種鑄造及有色合金,1998,(1):22-25.
[2] 柳建國等.熔模鑄鋼件裂紋改善措施研究與應用[J],金屬加工,2015,(7):78-81.
[3] 陳國楨等.鑄件缺陷和對策手冊[M]. 北京: 機械工業出版社,1996
[4] 王文清等.鑄造工藝學[M]. 北京: 機械工業出版社,2009
作者簡介:柳建國(1976-),男,內蒙古赤峰人,高級工程師,主要從事鑄造技術及節能減排研究工作。E-mail:liuyang139@163.com
附件下載:

-
地址:濟南市解放路134號 電話:0531-86401781 / 86952422 傳真:0531-86465075
郵箱:foundry-shandong@163.com 郵編:250013
版權所有 © 山東省鑄造協會 魯ICP備2021002429號
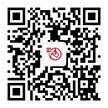
官方公眾號